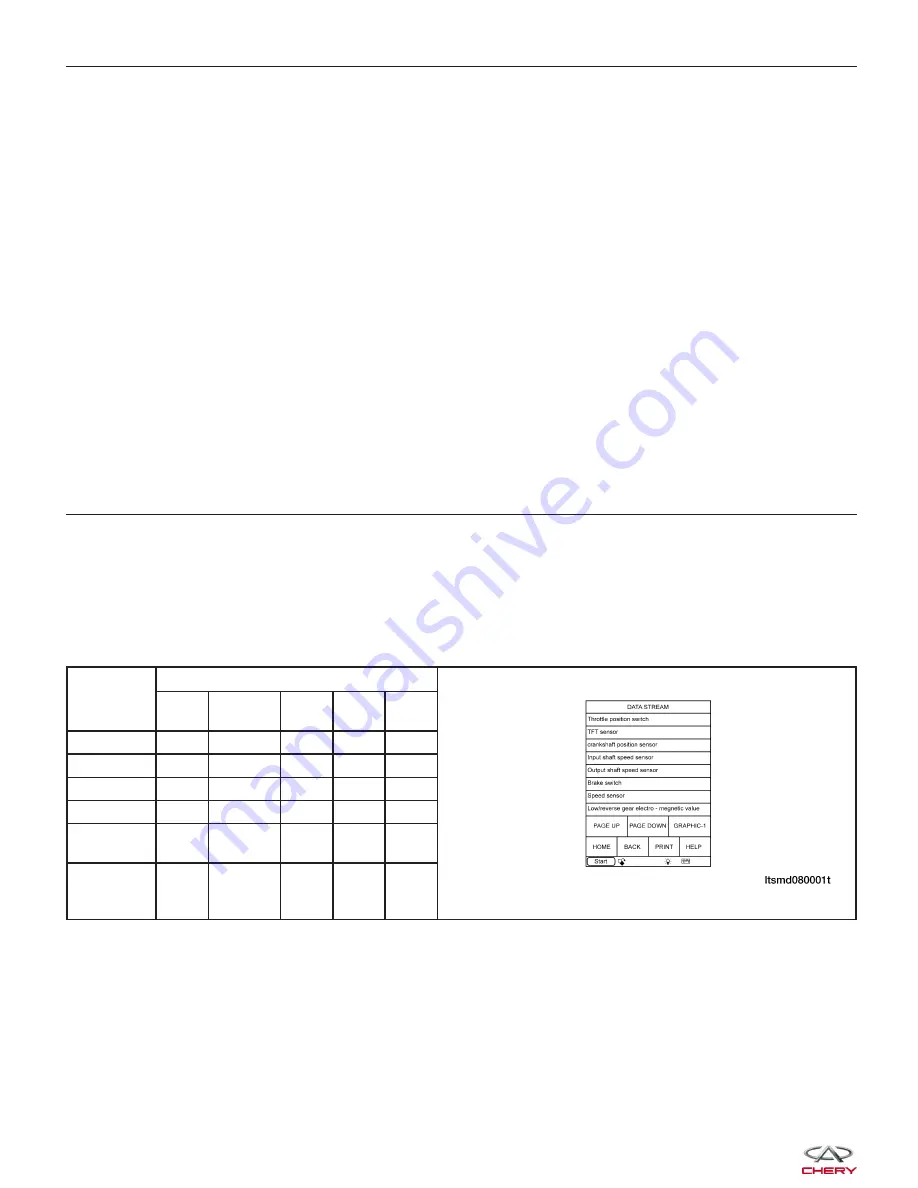
•
Turn ignition switch on, with the scan tool, view and erase stored DTCs in the TCM.
•
Start engine and warm it to normal operating temperature, then select
⬙
D
⬙
position.
•
Drive the vehicle in 1st, 2nd, 3rd and 4th gears.
•
With the scan tool, select view DTC and data stream.
•
If the DTC is detected, the DTC condition is current. Go to Diagnostic Procedure - Step 1.
•
If the DTC is not detected, the DTC condition is intermittent (See Diagnostic Help and Intermittent DTC Trou-
bleshooting in Section 08 Transaxle & Transfer Case for more information).
NOTE :
Checking the automatic transaxle fluid quality and fluid level is the most basic check of the automatic transaxle. The
fluid check is also an important inspection to determine if the transaxle will need to be disassembled.
CAUTION:
The burnt scent of ATF fluid indicates that the transaxle fluid is contaminated. The tiny particles in
the fluid pan indicate that the transaxle is worn out and it will be necessary to overhaul the trans-
axle.
NOTE :
While performing electrical diagnosis & testing, always refer to the electrical schematics for specific circuit
and component information.
Diagnostic Procedure
1.
CHECK FLUID QUALITY AND FLUID LEVEL AND DTC
•
Drive the vehicle, until the ATF reaches operating temperature (70° - 80°C).
•
Park the vehicle on level ground.
•
Shift the gear selector lever to all gear positions once, then shift to gear “N”.
•
Clean and check the outside of the dipstick and remove the dipstick to check the fluid level.
•
With the scan tool, select view DTC and data stream for A/T.
•
Start the engine.
•
Monitor the value of the gear position as indicated in the following table while driving:
GEAR
POSITION
ELECTRO-MAGNETIC VALVE
L/R
GEAR
2
UD
OD
DCC
(REF)
Gear 1
Off
On
Off
On
Off
Gear 2
On
Off
Off
On
On
Gear 3
On
Off
Off
Off
On
Gear 4
On
Off
On
Off
On
Reverse
gear
Off
On
On
On
Off
Neutral
gear/
Parking
Off
On
On
On
Off
Is DTC 22 or 23 present?
Yes
>>
If DTC 22 present, see diagnostic procedure for DTC 22 in 08 - Transaxle & Transfer Case
If DTC 23 present, see diagnostic procedure for DTC 23 in 08 - Transaxle & Transfer Case.
No
>>
Go to the next step.
DIAGNOSIS & TESTING
08–
214
Chery Automobile Co., Ltd.
Summary of Contents for Tiggo 2009
Page 291: ...Compression Gauge Fuel Pressure Gauge GENERAL INFORMATION 03 03 7 Chery Automobile Co Ltd...
Page 314: ...DIAGNOSIS TESTING LTSMW030043T 03 30 Chery Automobile Co Ltd...
Page 320: ...DIAGNOSIS TESTING LTSMW030046T 03 36 Chery Automobile Co Ltd...
Page 330: ...DIAGNOSIS TESTING LTSMW030055T 03 46 Chery Automobile Co Ltd...
Page 336: ...DIAGNOSIS TESTING LTSMW030055T 03 52 Chery Automobile Co Ltd...
Page 363: ...DIAGNOSIS TESTING LTSMW030058T 03 03 79 Chery Automobile Co Ltd...
Page 369: ...DIAGNOSIS TESTING LTSMW030052T 03 03 85 Chery Automobile Co Ltd...
Page 397: ...DIAGNOSIS TESTING LTSMW030055T 03 03 113 Chery Automobile Co Ltd...
Page 402: ...P0171 Fuel Trim System Too Lean DIAGNOSIS TESTING LTSMW030052T 03 118 Chery Automobile Co Ltd...
Page 403: ...DIAGNOSIS TESTING LTSMW030058T 03 03 119 Chery Automobile Co Ltd...
Page 404: ...DIAGNOSIS TESTING LTSMW030048T 03 120 Chery Automobile Co Ltd...
Page 405: ...DIAGNOSIS TESTING LTSMW030049T 03 03 121 Chery Automobile Co Ltd...
Page 416: ...DIAGNOSIS TESTING LTSMW030058T 03 132 Chery Automobile Co Ltd...
Page 417: ...DIAGNOSIS TESTING LTSMW030048T 03 03 133 Chery Automobile Co Ltd...
Page 418: ...DIAGNOSIS TESTING LTSMW030049T 03 134 Chery Automobile Co Ltd...
Page 427: ...DIAGNOSIS TESTING LTSMW030049T 03 03 143 Chery Automobile Co Ltd...
Page 434: ...DIAGNOSIS TESTING LTSMW030045T 03 150 Chery Automobile Co Ltd...
Page 442: ...DIAGNOSIS TESTING LTSMW030049T 03 158 Chery Automobile Co Ltd...
Page 449: ...DIAGNOSIS TESTING LTSMW030049T 03 03 165 Chery Automobile Co Ltd...
Page 482: ...DIAGNOSIS TESTING LTSMW030066T 03 198 Chery Automobile Co Ltd...
Page 487: ...DIAGNOSIS TESTING LTSMW030045T 03 03 203 Chery Automobile Co Ltd...
Page 495: ...DIAGNOSIS TESTING LTSMW030044T 03 03 211 Chery Automobile Co Ltd...
Page 517: ...Compression Gauge Fuel Pressure Gauge GENERAL INFORMATION 03 03 233 Chery Automobile Co Ltd...
Page 540: ...DIAGNOSIS TESTING LTSMW030024T 03 256 Chery Automobile Co Ltd...
Page 546: ...DIAGNOSIS TESTING LTSMW030027T 03 262 Chery Automobile Co Ltd...
Page 610: ...P0171 Fuel Trim System Too Lean DIAGNOSIS TESTING LTSMW030033T 03 326 Chery Automobile Co Ltd...
Page 611: ...DIAGNOSIS TESTING LTSMW030029T 03 03 327 Chery Automobile Co Ltd...
Page 612: ...DIAGNOSIS TESTING LTSMW030030T 03 328 Chery Automobile Co Ltd...
Page 620: ...P0172 Fuel Trim System Too Rich DIAGNOSIS TESTING LTSMW030033T 03 336 Chery Automobile Co Ltd...
Page 621: ...DIAGNOSIS TESTING LTSMW030029T 03 03 337 Chery Automobile Co Ltd...
Page 622: ...DIAGNOSIS TESTING LTSMW030030T 03 338 Chery Automobile Co Ltd...
Page 630: ...DIAGNOSIS TESTING LTSMW030030T 03 346 Chery Automobile Co Ltd...
Page 644: ...DIAGNOSIS TESTING LTSMW030030T 03 360 Chery Automobile Co Ltd...
Page 651: ...DIAGNOSIS TESTING LTSMW030030T 03 03 367 Chery Automobile Co Ltd...
Page 662: ...P0324 Knock Control System Error DIAGNOSIS TESTING LTSMW030028T 03 378 Chery Automobile Co Ltd...
Page 684: ...P0645 A C Clutch Relay Circuit DIAGNOSIS TESTING LTSMW030063T 03 400 Chery Automobile Co Ltd...
Page 685: ...DIAGNOSIS TESTING LTSMW030064T 03 03 401 Chery Automobile Co Ltd...
Page 690: ...DIAGNOSIS TESTING LTSMW030026T 03 406 Chery Automobile Co Ltd...
Page 698: ...DIAGNOSIS TESTING LTSMW030025T 03 414 Chery Automobile Co Ltd...
Page 704: ...U0001 High Speed CAN Defective DIAGNOSIS TESTING LTSMW030038T 03 420 Chery Automobile Co Ltd...
Page 730: ...Compression Gauge Fuel Pressure Gauge GENERAL INFORMATION 03 446 Chery Automobile Co Ltd...
Page 748: ...DIAGNOSIS TESTING LTSMW030004T 03 464 Chery Automobile Co Ltd...
Page 754: ...DIAGNOSIS TESTING LTSMW030017T 03 470 Chery Automobile Co Ltd...
Page 760: ...12 Air Flow Sensor DIAGNOSIS TESTING LTSMW030013T 03 476 Chery Automobile Co Ltd...
Page 766: ...13 Air Temperature Sensor DIAGNOSIS TESTING LTSMW030013T 03 482 Chery Automobile Co Ltd...
Page 771: ...14 Throttle Position Sensor DIAGNOSIS TESTING LTSMW030014T 03 03 487 Chery Automobile Co Ltd...
Page 777: ...21 Coolant Temperature Sensor DIAGNOSIS TESTING LTSMW030005T 03 03 493 Chery Automobile Co Ltd...
Page 782: ...22 Crankshaft Position Sensor DIAGNOSIS TESTING LTSMW030012T 03 498 Chery Automobile Co Ltd...
Page 788: ...23 Camshaft Position Sensor DIAGNOSIS TESTING LTSMW030011T 03 504 Chery Automobile Co Ltd...
Page 794: ...25 Atmosphere Pressure Sensor DIAGNOSIS TESTING LTSMW030013T 03 510 Chery Automobile Co Ltd...
Page 799: ...31 Knock Sensor DIAGNOSIS TESTING LTSMW030006T 03 03 515 Chery Automobile Co Ltd...
Page 803: ...41 Injector DIAGNOSIS TESTING LTSMW030008T 03 03 519 Chery Automobile Co Ltd...
Page 809: ...44 Ignition Signal DIAGNOSIS TESTING LTSMW030007T 03 03 525 Chery Automobile Co Ltd...
Page 864: ...Canister Control Valve 2 0L GENERAL INFORMATION LTSMW030031T 03 580 Chery Automobile Co Ltd...
Page 865: ...Canister Control Valve 2 4L GENERAL INFORMATION LTSMW030009T 03 03 581 Chery Automobile Co Ltd...
Page 881: ...Fuel Delivery System Page 3 of 6 GENERAL INFORMATION LTSMW040003T 04 8 Chery Automobile Co Ltd...
Page 902: ...Starting System Page 2 of 2 GENERAL INFORMATION LTSMW050003T 05 05 5 Chery Automobile Co Ltd...
Page 912: ...Charging System Page 2 of 2 GENERAL INFORMATION LTSMW050004T 05 05 15 Chery Automobile Co Ltd...
Page 922: ...Cooling System Page 2 of 5 GENERAL INFORMATION LTSMW060002T 06 06 7 Chery Automobile Co Ltd...
Page 923: ...Cooling System Page 3 of 5 GENERAL INFORMATION LTSMW060003T 06 8 Chery Automobile Co Ltd...
Page 924: ...Cooling System Page 4 of 5 GENERAL INFORMATION LTSMW060004T 06 06 9 Chery Automobile Co Ltd...
Page 925: ...Cooling System Page 5 of 5 GENERAL INFORMATION LTSMW060005T 06 10 Chery Automobile Co Ltd...
Page 955: ...Automatic Transaxle Page 3 of 8 GENERAL INFORMATION LTSMW080035T 08 12 Chery Automobile Co Ltd...
Page 957: ...Automatic Transaxle Page 5 of 8 GENERAL INFORMATION LTSMW080036T 08 14 Chery Automobile Co Ltd...
Page 959: ...Automatic Transaxle Page 7 of 8 GENERAL INFORMATION LTSMW080038T 08 16 Chery Automobile Co Ltd...
Page 966: ...A T Fluid Temperature Sensor DIAGNOSIS TESTING LTSMW080018T 08 08 23 Chery Automobile Co Ltd...
Page 993: ...P0730 Ratio Of Transaxle Error DIAGNOSIS TESTING LTSMW080016T 08 50 Chery Automobile Co Ltd...
Page 1042: ...P0840 Pressure Sensor DIAGNOSIS TESTING LTSMW080015T 08 08 99 Chery Automobile Co Ltd...
Page 1073: ...U0001 CAN Communication Error DIAGNOSIS TESTING LTSMW080019T 08 130 Chery Automobile Co Ltd...
Page 1089: ...Transaxle Hydraulic Schematics GENERAL INFORMATION LTSM080165T 08 146 Chery Automobile Co Ltd...
Page 1106: ...22 Input Speed Sensor DIAGNOSIS TESTING LTSMW080006T 08 08 163 Chery Automobile Co Ltd...
Page 1111: ...23 Output Speed Sensor Fault DIAGNOSIS TESTING LTSMW080007T 08 168 Chery Automobile Co Ltd...
Page 1179: ...54 Electrical Relay Open Circuit DIAGNOSIS TESTING LTSMW080003T 08 236 Chery Automobile Co Ltd...
Page 1252: ...GENERAL INFORMATION LTSM080109 08 08 309 Chery Automobile Co Ltd...
Page 1291: ...GENERAL INFORMATION Description LTSM160027 09 09 17 Chery Automobile Co Ltd...
Page 1443: ...DIAGNOSIS TESTING LTSMW120011T 12 48 Chery Automobile Co Ltd...
Page 1444: ...DIAGNOSIS TESTING LTSMW120002T 12 12 49 Chery Automobile Co Ltd...
Page 1445: ...DIAGNOSIS TESTING LTSMW120003T 12 50 Chery Automobile Co Ltd...
Page 1450: ...DIAGNOSIS TESTING LTSMW120004T 12 12 55 Chery Automobile Co Ltd...
Page 1455: ...DIAGNOSIS TESTING LTSMW120005T 12 60 Chery Automobile Co Ltd...
Page 1460: ...DIAGNOSIS TESTING LTSMW120006T 12 12 65 Chery Automobile Co Ltd...
Page 1465: ...DIAGNOSIS TESTING LTSMW120007T 12 70 Chery Automobile Co Ltd...
Page 1541: ...DIAGNOSIS TESTING LTSMW140003T 14 12 Chery Automobile Co Ltd...
Page 1558: ...B2501 Warning Lamp Fault Open DIAGNOSIS TESTING LTSMW140008T 14 14 29 Chery Automobile Co Ltd...
Page 1571: ...DIAGNOSIS TESTING LTSMW140003T 14 42 Chery Automobile Co Ltd...
Page 1590: ...Audio System Page 2 of 3 AUDIO SYSTEM LTSMW150002T 15 6 Chery Automobile Co Ltd...
Page 1591: ...Audio System Page 3 of 3 AUDIO SYSTEM LTSMW150085T 15 15 7 Chery Automobile Co Ltd...
Page 1602: ...CAN Vehicle Communications Page 2 of 2 LTSMW150032T 15 18 Chery Automobile Co Ltd...
Page 1604: ...Electrical Schematics Chime Page 1 of 9 CHIME LTSMW150068T 15 20 Chery Automobile Co Ltd...
Page 1605: ...Chime Page 2 of 9 CHIME LTSMW150069T 15 15 21 Chery Automobile Co Ltd...
Page 1606: ...Chime Page 3 of 9 CHIME LTSMW150070T 15 22 Chery Automobile Co Ltd...
Page 1607: ...Chime Page 4 of 9 CHIME LTSMW150071T 15 15 23 Chery Automobile Co Ltd...
Page 1608: ...Chime Page 5 of 9 CHIME LTSMW150072T 15 24 Chery Automobile Co Ltd...
Page 1609: ...Chime Page 6 of 9 CHIME LTSMW150073T 15 15 25 Chery Automobile Co Ltd...
Page 1610: ...Chime Page 7 of 9 CHIME LTSMW150074T 15 26 Chery Automobile Co Ltd...
Page 1611: ...Chime Page 8 of 9 CHIME LTSMW150075T 15 15 27 Chery Automobile Co Ltd...
Page 1612: ...Chime Page 9 of 9 CHIME LTSMW150076T 15 28 Chery Automobile Co Ltd...
Page 1615: ...Power Door Lock System Page 2 of 5 DOOR LOCKS LTSMW150052T 15 15 31 Chery Automobile Co Ltd...
Page 1616: ...Power Door Lock System Page 3 of 5 DOOR LOCKS LTSMW150053T 15 32 Chery Automobile Co Ltd...
Page 1617: ...Power Door Lock System Page 4 of 5 DOOR LOCKS LTSMW150054T 15 15 33 Chery Automobile Co Ltd...
Page 1618: ...Power Door Lock System Page 5 of 5 DOOR LOCKS LTSMW150055T 15 34 Chery Automobile Co Ltd...
Page 1640: ...Instrument Cluster Page 3 of 8 INSTRUMENT CLUSTER LTSMW150102T 15 56 Chery Automobile Co Ltd...
Page 1642: ...Instrument Cluster Page 5 of 8 INSTRUMENT CLUSTER LTSMW150104T 15 58 Chery Automobile Co Ltd...
Page 1644: ...Instrument Cluster Page 7 of 8 INSTRUMENT CLUSTER LTSMW150106T 15 60 Chery Automobile Co Ltd...
Page 1651: ...DIAGNOSIS TESTING LTSMW150038T 15 15 67 Chery Automobile Co Ltd...
Page 1671: ...Interior Lamps Page 2 of 5 INTERIOR LAMPS LTSMW150062T 15 15 87 Chery Automobile Co Ltd...
Page 1672: ...Interior Lamps Page 3 of 5 INTERIOR LAMPS LTSMW150063T 15 88 Chery Automobile Co Ltd...
Page 1673: ...Interior Lamps Page 4 of 5 INTERIOR LAMPS LTSMW150064T 15 15 89 Chery Automobile Co Ltd...
Page 1674: ...Interior Lamps Page 5 of 5 INTERIOR LAMPS LTSMW150086T 15 90 Chery Automobile Co Ltd...
Page 1682: ...Power Window System Page 2 of 3 POWER WINDOW LTSMW150047T 15 98 Chery Automobile Co Ltd...
Page 1683: ...Power Window System Page 3 of 3 POWER WINDOW LTSMW150048T 15 15 99 Chery Automobile Co Ltd...
Page 1734: ...BODY DIMENSIONS LTSM150003 15 150 Chery Automobile Co Ltd...
Page 1738: ...Vehicle Clearance Front View BODY DIMENSIONS LTSM150005 15 154 Chery Automobile Co Ltd...
Page 1741: ...Body Side View BODY DIMENSIONS LTSM150011 15 15 157 Chery Automobile Co Ltd...
Page 1747: ...Rear View BODY DIMENSIONS LTSM150026 15 15 163 Chery Automobile Co Ltd...
Page 1764: ...Headlamp Aiming System Page 2 of 2 EXTERIOR LAMPS LTSMW150016T 15 180 Chery Automobile Co Ltd...
Page 1767: ...Fog Lamps Page 1 of 2 EXTERIOR LAMPS LTSMW150020T 15 15 183 Chery Automobile Co Ltd...
Page 1768: ...Fog Lamps Page 2 of 2 EXTERIOR LAMPS LTSMW150021T 15 184 Chery Automobile Co Ltd...
Page 1771: ...Stop Lamps Page 1 of 1 EXTERIOR LAMPS LTSMW150017T 15 15 187 Chery Automobile Co Ltd...
Page 1772: ...Backup Lamp Page 1 of 1 EXTERIOR LAMPS LTSMW150024T 15 188 Chery Automobile Co Ltd...
Page 1791: ...Electrical Schematics Horn Page 1 of 1 HORN LTSMW150003T 15 15 207 Chery Automobile Co Ltd...
Page 1795: ...Power Mirrors Page 2 of 2 MIRRORS LTSMW150008T 15 15 211 Chery Automobile Co Ltd...
Page 1796: ...Heated Mirrors Page 1 of 2 MIRRORS LTSMW150009T 15 212 Chery Automobile Co Ltd...
Page 1797: ...Heated Mirrors Page 2 of 2 MIRRORS LTSMW150010T 15 15 213 Chery Automobile Co Ltd...
Page 1808: ...SUNROOF Description BESM150008 15 224 Chery Automobile Co Ltd...
Page 1810: ...Electrical Schematics Sunroof Page 1 of 2 SUNROOF LTSMW150033T 15 226 Chery Automobile Co Ltd...
Page 1811: ...Sunroof Page 2 of 2 SUNROOF LTSMW150034T 15 15 227 Chery Automobile Co Ltd...
Page 1865: ...Overview Power Fuse Box GENERAL INFORMATION LTSMW170004T 16 16 39 Chery Automobile Co Ltd...
Page 1884: ...Main Harness VEHICLE HARNESS ROUTING MAPS LTSMW170014T 16 58 Chery Automobile Co Ltd...
Page 1887: ...Body Harness VEHICLE HARNESS ROUTING MAPS LTSMW170015T 16 16 61 Chery Automobile Co Ltd...