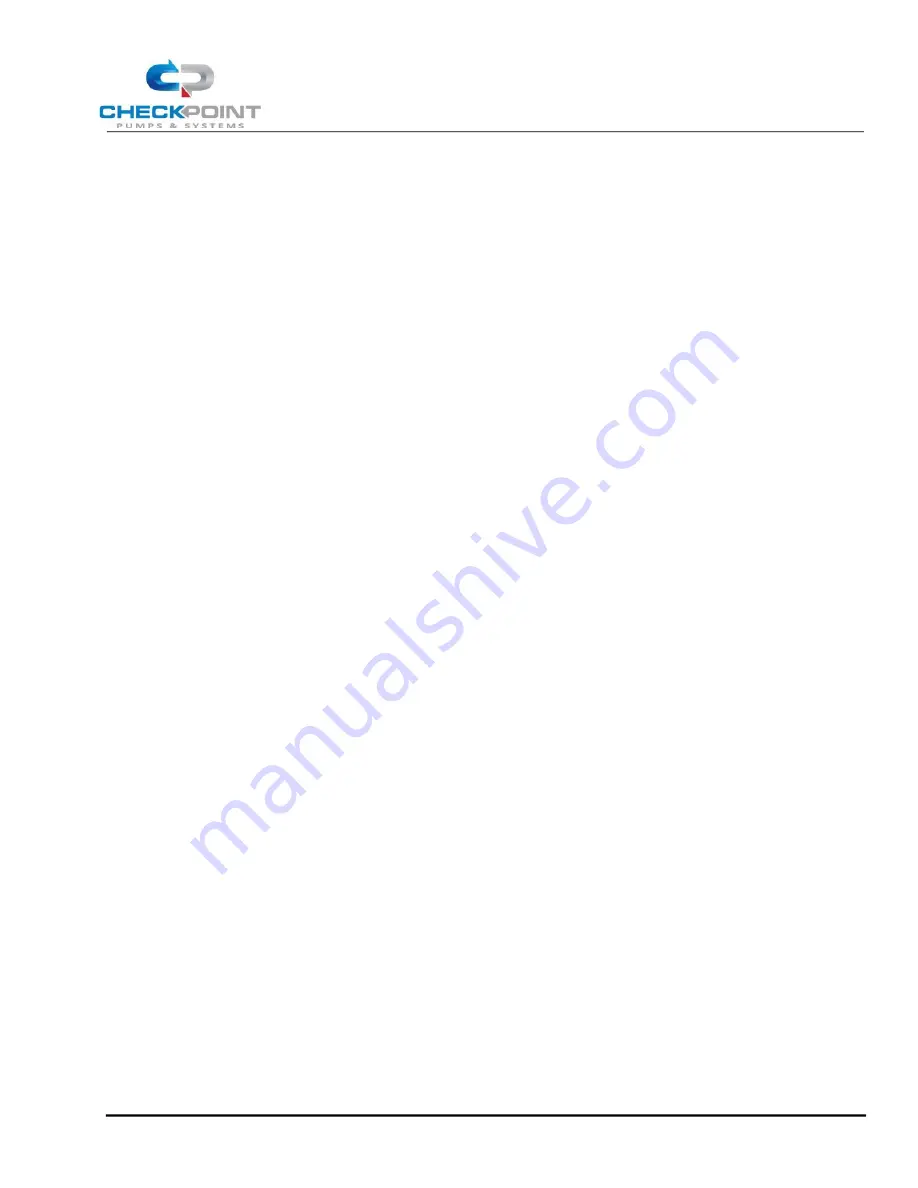
Series 1250 Pneumatic Chemical Injection Pump
Operating Manual
Page 18 of 19
6.1.5
Calibration gauge may reading incorrectly due to clogged air vent
If the calibration gauge is not reading
correctly, the user may be fooled into thinking the chemical is not getting into the process. Check for an obstruction
in the gauge or in the air vent atop the gauge.
6.2 Pump does not stroke
6.2.1
Pump speed control valve may not be turned on
Open the speed control valve fully (counterclockwise)
until pump actuates. Then set desired stroke rate as described in
Section 3.2
.
6.2.2
Air/Gas supply pressure may be too low to overcome the chemical discharge pressure
Open the bleed
port on the side of the chemical head. If the pump starts stroking, check to ensure that the supply air/gas pressure
is high enough to overcome the chemical discharge pressure. In many cases, a faulty pressure gauge or regulator is
at fault. See
Section 1.3.4
on page 7 to determine the minimum supply pressure for your discharge pressure.
6.2.3
Gas recovery pressure is too high relative to gas supply pressure (Gas Recovery pumps only)
In GR
pumps, the pump not only has to overcome the chemical discharge pressure but also the gas recovery pressure.
Refer to
Section 2.1.1
on page 8 to determine the appropriate recovery pressure.
6.2.4
Pump switching valve may be clogged or "gummed-up" with paraffin or trash
Disconnect air/gas supply,
then pour any type of oil or solvent into the pump air/gas inlet. Re-connect air/gas supply and open speed control
valve. Repeat two to three times if necessary. When pump is running normally, reset pump stroking rate as described
in
Section 3.2
on page 9.
6.2.5
Spool may be swollen
Occasionally, certain types of chemicals that are introduced into the motor through
the air/gas inlet may be absorbed by the standard spool material, causing it to swell. If, after removal of the housing
with the spool still inside, the spool will not move with light finger pressure inside the housing, call CheckPoint to
order a replacement spool made of a different material.
6.2.6
After a repair, alignment screw may have been incorrectly reinstalled
If care is not taken to replace the
alignment screw finger tight prior to tightening by wrench, it may be that it has been screwed into the plastic spool
rather than into the alignment slot in the spool. Normally this can be corrected by removal of the alignment screw
and replacement after properly repositioning the clock position of the spool inside its housing.
6.2.7
Seals may be worn in the motor
If the pump has been in service for some time, the motor seals may have
worn to the point where the pump can no longer switch. If air leakage is constant during stall, worn or damaged
seals are indicated. Performing an overhaul on the motor and replacing all seals is required.
6.3 Pump strokes erratically
6.3.1
Supply pressure may be fluctuating
Check supply pressure with an accurate pressure gauge to ensure
constant supply pressure. If fluctuations are observed, replace gas pressure regulator, or, if none exists, add a
pressure regulator ahead of the air/gas inlet.
6.4 Chemical leakage from packing nut
6.4.1
Packing nut may not be tight enough
Adjust packing nut per
Section 5.1
on page 14.
6.4.2
Packing may be worn
If tightening the packing does not stop leakage, worn or damaged packing is almost
certainly indicated. However, prior to replacing the packing, it is important to determine if wear is premature.
Common causes of prematurely worn packing are:
6.4.3
Packing nut may have been overtightened
Packing will appear smashed and the elastomer ring will be
nearly completely destroyed due to heating and compression.
CP/MAN-PRD-015 REV. 15 EFF. DATE: 07/08/2022