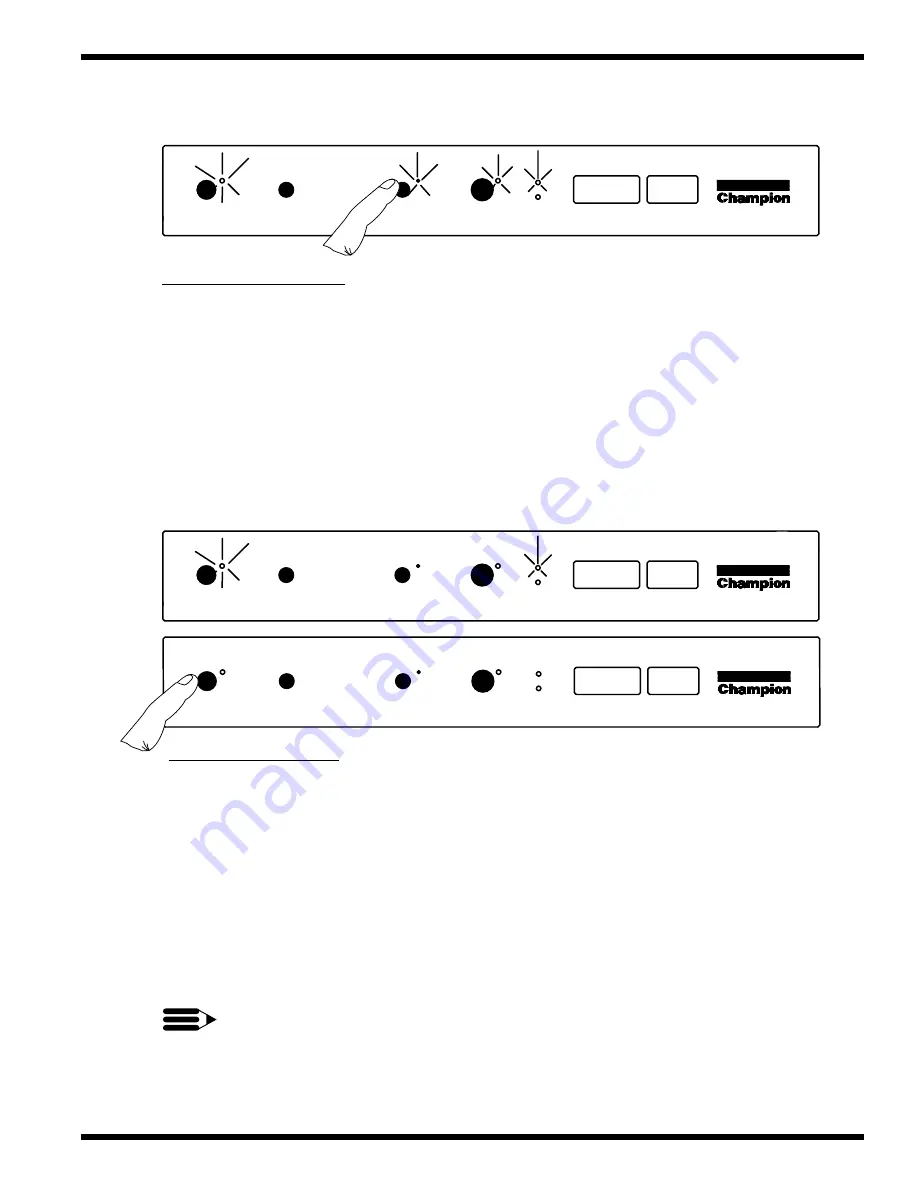
33
Part 3:
DAILY OPERATION
EXTENDED WASH FEATURE
The EXTENDED WASH button pauses the normal wash cycle and holds the dishwasher in a continuous
wash mode until the extended wash button is pushed again.
To activate the extended wash feature:
Push the START button to begin a cycle.
WAIT 16 seconds to allow the optional detergent pump time to inject detergent.
Push the EXTENDED WASH button.
The Extended Wash LED illuminates. The Power LED remains lit, the Start LED remains lit.
Dishwasher is held in continuous wash mode.
Push the EXTENDED WASH button again.
The Extended Wash LED goes out. The Power LED remains lit, the Start LED remains lit.
If the extended wash is deactivated before the 60-second wash cycle is complete, the dishwasher will
complete the normal wash cycle, drain and finish with a final rinse.
If the extended wash is deactivated after the 60-second wash cycle time has elapsed, then the
dishwasher will immediately drain, and finish with a final rinse.
3.5.1 Operating the UH-200B and UH-200 (Cont.)
AUTO-SHUTDOWN CYCLE
At the end of the day, pushing the POWER button initiates the Auto-shutdown cycle which includes an
automatic interior rinse down to aid in cleaning the machine. Pushing the POWER button when the
dishwasher is in cycle also will start the auto shutdown cycle.
To activate the auto shutdown cycle:
Push the POWER button.
All LED's go out.
The Temperature display and the Pressure display flash 888F.
The machine drains.
The fill valve opens to rinse down the interior of the dishwasher.
The machine drains completely.
All displays go out.
Dishwasher is OFF.
Begin cleaning operation or push POWER button to refill dishwasher.
NOTE:
If the dishwasher is idle for more than 4 hours, it will automatically enter the
auto-shutdown cycle.
This completes the basic operation for the UH-200B and UH-200.
START
POWER
PRIME
WASH
EXTENDED
WASH
RINSE
TEMPERATURE
PRESSURE
150F
START
POWER
PRIME
WASH
EXTENDED
WASH
RINSE
TEMPERATURE
PRESSURE
150F
START
POWER
PRIME
WASH
EXTENDED
WASH
RINSE
TEMPERATURE
PRESSURE
888F
888