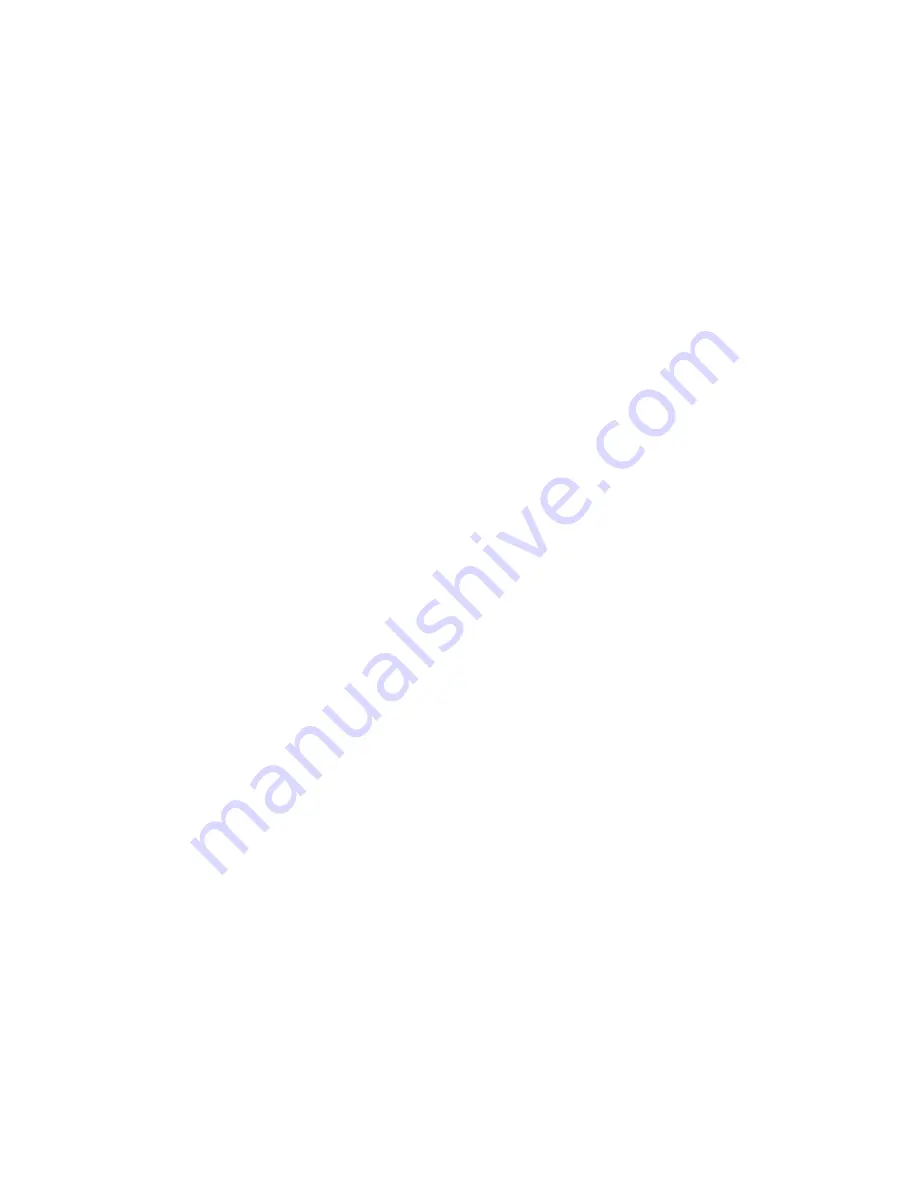
Model VLE10
Installation, Operation and Maintenance
Page 11
Rev. 03/28/2020
VL
E10-IOM-A.
doc
L
IFTING A
V
EHICLE
1) Ensure that the lifting arms are parked, out to full
drive thru position.
2) Center the vehicle between the columns in the
service bay and position the vehicle’s center of
gravity midpoint between the columns. NOTE:
the center of gravity is based on the weight
distribution and is not the same as the center
point of the vehicle.
D
O NOT EXCEED
2500
POUNDS PER ARM
.
D
O NOT ATTEMPT TO LIFT THE VEHICLE WITH ONLY TWO
ARMS
,
AS THIS WILL VOID THE WARRANTY
E
NSURE THAT THE HIGHEST POINT ON THE VEHICLE
WILL CONTACT THE
O
VERHEAD
L
IMIT
S
WITCH
B
AR
.
D
O NOT PLACE THE VEHICLE IN THE SERVICE BAY
BACKWARDS
.
R
EFER TO THE VEHICLE MANUFACTURERS SERVICE
MANUAL
,
TECHNICAL BULLETINS
,
“V
EHICLE
L
IFTING
P
OINTS
G
UIDE
”
(ALI/LP-G
UIDE
)
OR OTHER
PUBLICATIONS TO LOCATE THE RECOMMENDED LIFTING
POINTS
.
3) Position the arms and adapters so all four pads
contact the vehicle simultaneously.
The vehicle should remain level during lifting
.
4) Raise the lift until all four wheels are off the
ground. Test the stability of the vehicle by
attempting to rock the vehicle. Check adapters
for secure contact with vehicle lift points. If the
vehicle seems unstable, lower the lift and
readjust the arms. If the vehicle is stable, raise
the vehicle to a height a few inches above the
desired working height.
5) Lower the vehicle until the safety latches on both
columns engage. The vehicle should remain
level when both latches are engaged. If one side
engages and the other continues to descend,
stop lowering the vehicle, raise it several inches,
and try again to engage both latches.
Always lower lift into locks before entering the
area beneath the vehicle.
A
lways use safety stands when removing or
installing heavy components.
L
OWERING
A
V
EHICLE
1) Ensure that the area under the vehicle is clear of
personnel and tools.
2) Raise the vehicle until both latches are free.
3) Disengage the latches by pulling down and
holding the lock release lever.
4) Lower the vehicle by depressing the lowering
valve handle.
5) Continue to lower the vehicle until the carriages
stop against the base plate. Retract the
extension arms, and park them.
L
OSS OF POWER
If for any reason the lift will not raise off the locks or
the locks will not retract, consult factory authorized
personnel.
DO NOT OVERRIDE ANY SAFETY FEATURE IN
AN ATTEMPT TO LOWER THE LIFT.