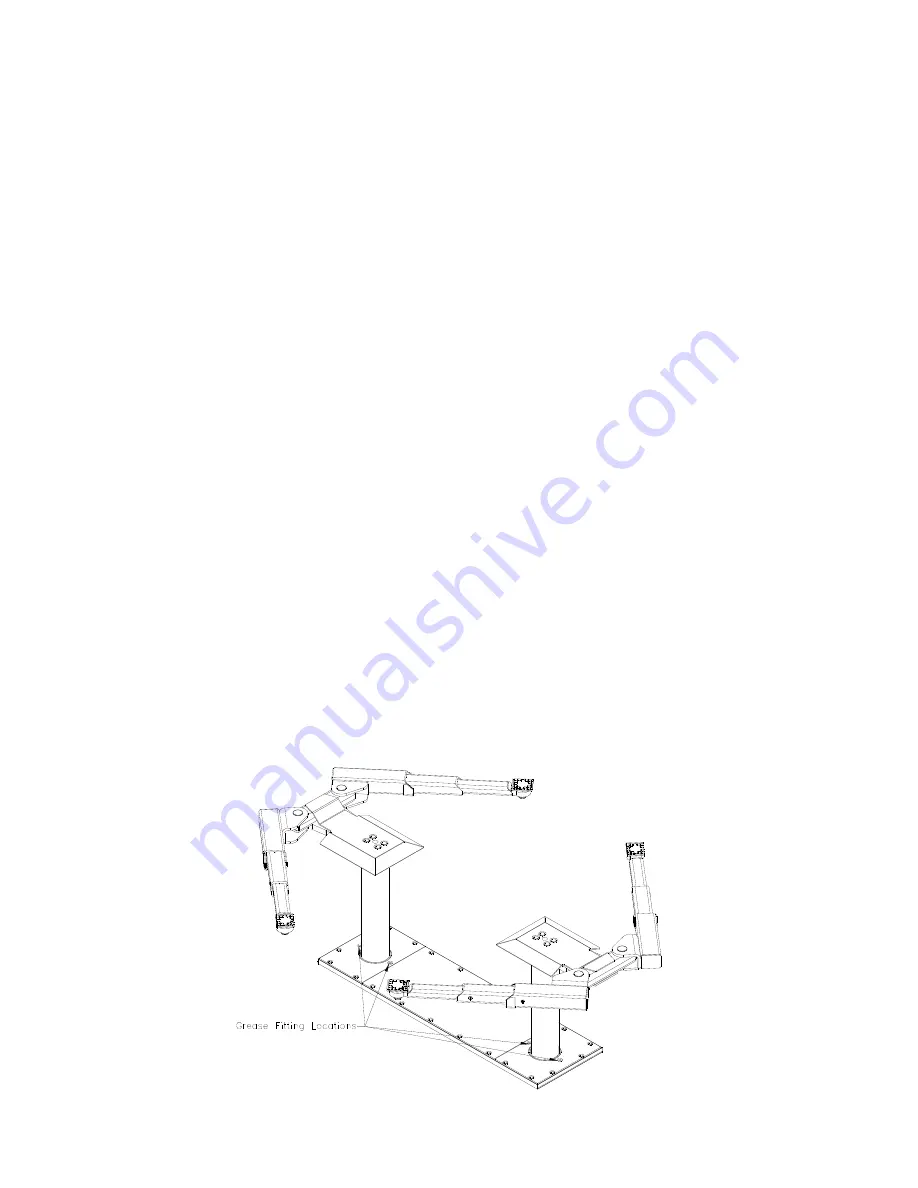
Models EV1020QC
Installation, Operation and Maintenance
Rev. 8/25/20
EVQC-IOM-A.doc
15
Maintenance
To avoid personal injury, permit only qualified personnel to perform maintenance on this equipment. Maintenance
personnel should follow lockout/tagout instructions per ANSI Z244.1.
The following maintenance points are suggested as the basis of a routine maintenance program. The actual maintenance
program should be tailored to the usage of the lift. See ANSI/ALI ALOIM booklet for periodic inspection checklist and
maintenance log sheet.
If lift stops short of full rise or chatters, check fluid level and bleed both cylinders per Installation Instructions.
Replace all Safety, Warning or Caution Labels if missing or damaged (
See Installation instructions page 3
.
)
Daily
Drain water from air supply to avoid contamination of lock release components.
Check lock operation. The lock operation should be heard as lift is raised.
Inspect lifting adapters for damage.
Keep area around lift / containment assembly clean and free of dirt, sand, water, etc. to
prevent scoring of the plunger.
Remove excess grease and debris from plunger by wiping them down with a clean cloth.
Monthly
Check fluid level in the power unit.
Check for proper torque on all superstructure bolts (120 ft-lbs.).
Clean and lubricate lifting arm pins and pads.
Quarterly
Grease Lift Guide bearings using Mobil, Mobilith SHC 1500 synthetic grease. Each guide
bearing is supplied with two grease zerk and should take 10-12 pumps (hand pump only) while
raising and lowering the lift empty.