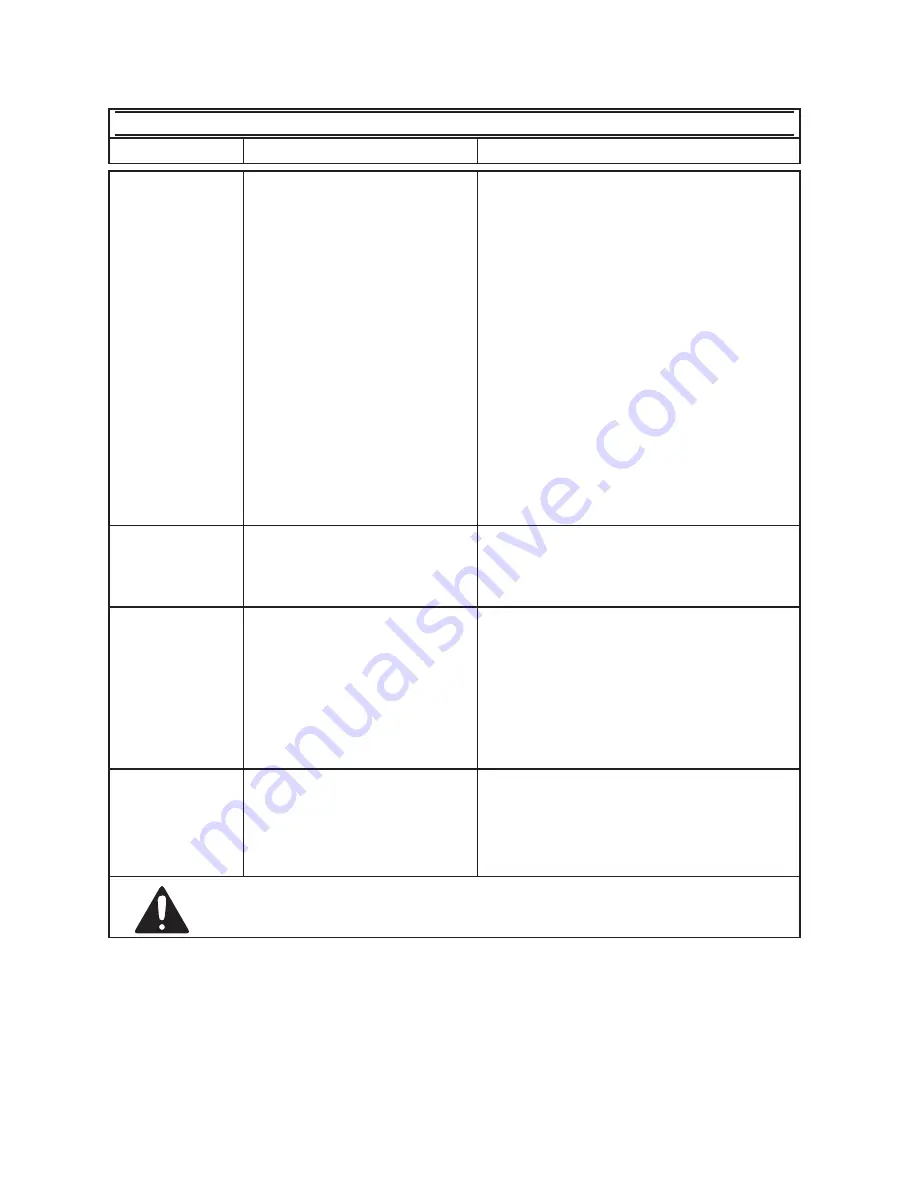
SKU 99637
For technical questions, please call 1-800-444-3353.
Page 14
TROUBLESHOOTING
Problem
Possible Causes
Possible Solutions
Decreased output. 1. Not enough air pressure and/
or air flow.
2. Obstructed trigger.
3. Incorrect lubrication or not
enough lubrication.
4. Blocked air inlet screen (if
equipped).
5. Air leaking from loose
housing.
6. Mechanism contaminated.
1. Vane wear or damage.
1. Check for loose connections and make
sure that air supply is providing enough air
flow (6 CFM) at required pressure (70-110
PSI) to the tool’s air inlet.
Do not exceed
maximum air pressure.
2. Clean around trigger to ensure free
movement.
3. Lubricate using air tool oil and grease
according to directions.
4. Clean air inlet screen of buildup.
5. Make sure housing is properly assembled
and tight.
6. Have qualified technician clean and
lubricate mechanism. Install in-line filter
in air supply as stated in Initial Set Up: Air
Supply.
7. Replace all vanes.
Housing heats
during use.
1. Incorrect lubrication or not
enough lubrication.
2. Worn parts.
1. Lubricate using air tool oil and grease
according to directions.
2. Have qualified technician inspect internal
mechanism and replace parts as needed.
Severe air
leakage.
(Slight air leakage
is normal,
especially on
older tools.)
1. Cross-threaded housing
components.
2. Loose housing.
3. Damaged valve or housing.
4. Dirty, worn or damaged valve.
1. Check for incorrect alignment and uneven
gaps. If cross-threaded, disassemble and
replace damaged parts before use.
2. Tighten housing assembly. If housing
cannot tighten properly, internal parts may
be misaligned.
3. Replace damaged components.
4. Clean or replace valve assembly.
Frequent
jamming.
1. Incorrect fasteners.
2. Damaged fasteners.
3. Magazine is dirty.
4. Driver is worn or damaged.
1. Use the correct fasteners.
2. Replace with undamaged fasteners.
3. Clean magazine.
4. Have a qualified service technician replace
driver.
Follow all safety precautions whenever diagnosing or servicing the
tool. Disconnect air supply before service.