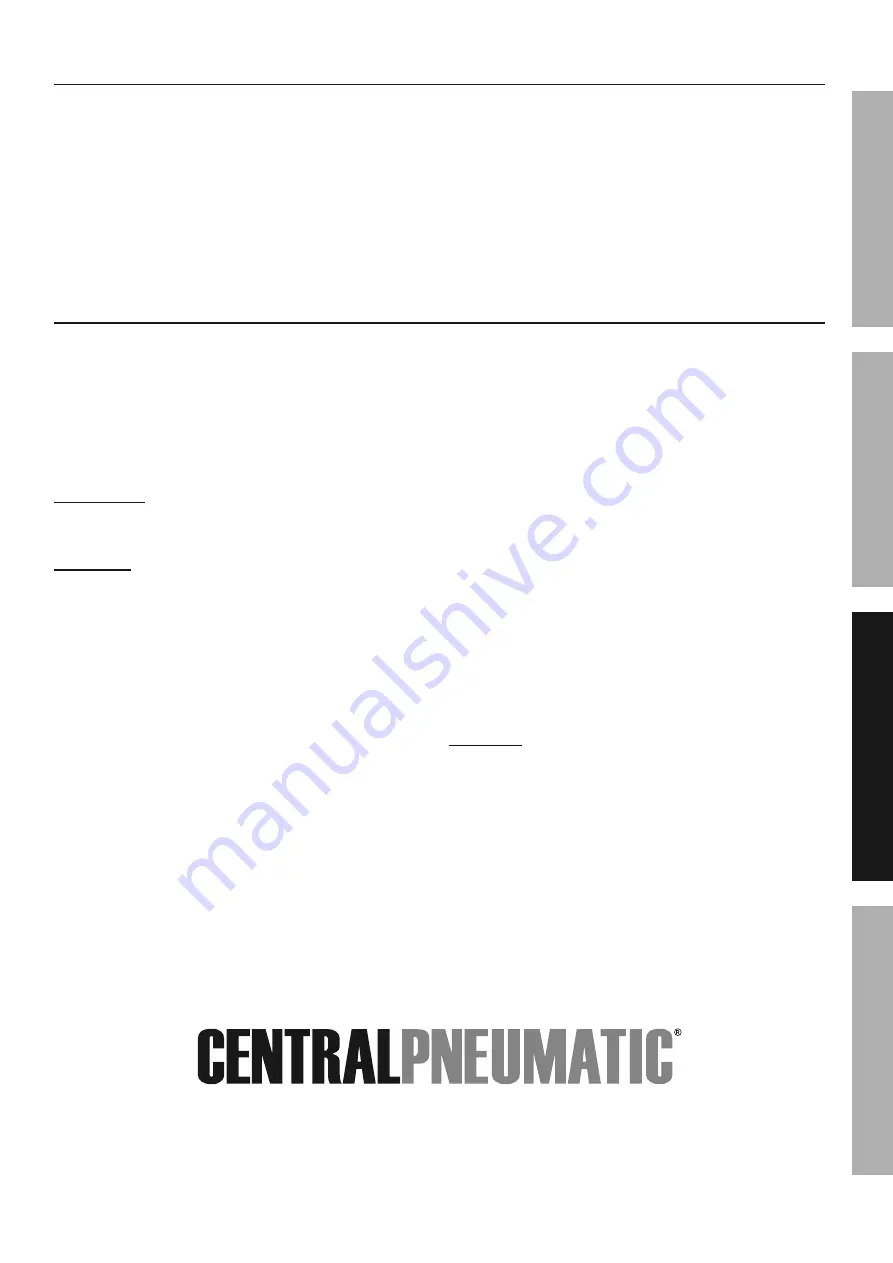
Page 11
For technical questions, please call 1-888-866-5797.
Item 93458
Workpiece and Work Area Set Up
1. Designate a work area that is clean and well-lit.
The work area must not allow access by children
or pets to prevent distraction and injury.
2. Route the air hose along a safe route to reach
the work area without creating a tripping hazard
or exposing the air hose to possible damage.
The air hose must be long enough to reach
the work area with enough extra length to
allow free movement while working.
3. Secure loose workpieces using a vise or clamps
(not included) to prevent movement while working.
4. There must not be hazardous objects
(such as utility lines or foreign objects) nearby
that will present a hazard while working.
General Operating Instructions
1. Secure the Pin Cap (23) firmly to the
Riveter by tightening the Pin Cap Nut (22).
While securing turn the slot in the Pin Cap
upward to avoid spilling used rivet pins.
2. Depending on the size of rivet’s pin used,
attach the corresponding Nosepiece size
(3/16″, 5/32″, 1/8″, or 3/32″) with the Wrench (36).
IMPORTANT:
When drilling rivet holes in a workpiece,
use the same diameter drill bit as the
outer diameter of rivet you will be using.
WARNING!
Verify that work surface has
no hidden utility lines before drilling.
3. Attach an air hose to the
Quick Connector (53) of the Riveter.
4. Turn on the air compressor, and set its regulator to
the needed pressure.
Do not exceed the tool’s
maximum air pressure rating.
5. Insert the small end of a rivet fully through
the Nosepiece (1A, 1B, 1C, or 1D).
CAUTION! Keep clear of the trigger
when inserting rivets.
6. Insert the rivet through the predrilled
hole in the workpiece.
7. Hold the Riveter firmly with both hands, and squeeze
the Trigger (40) to activate the Riveter. Repeat as
necessary. Then, release pressure on the Trigger.
8. Check to be sure the rivet looks soild and
securely locks the workpiece together.
• If the installed rivet is too loose then the
workpiece sections will move and not be locked
together. This indicates the rivet pin was not
adequately pulled through the workpiece. Either
the wrong size rivet was used or Riveter’s Jaw
Case is too loose and not gripping the rivet pin
well enough to pull it fully through the workpiece.
• A concave, deformed or broken rivet head
indicates the rivet pin was pulled too far into
the workpiece. Either the wrong size rivet was
used or Riveter’s Jaw Case is too tight and not
properly releasing the rivet pin during installation.
9. If the tool requires more force to accomplish
the task, verify that the tool receives sufficient,
unobstructed airflow (CFM) and increase the
pressure (PSI) output of the regulator up to the
maximum air pressure rating of this tool.
CAUTION! TO PREVENT INJURY FROM
TOOL OR ACCESSORY FAILURE:
Do not exceed the tool's
maximum air pressure rating.
If the tool still does not have sufficient force
at maximum pressure and sufficient airflow,
then a larger tool may be required.
10. To prevent accidents, turn off the tool, detach the air
supply, safely discharge any residual air pressure
in the tool, and release the trigger after use.
Clean external surfaces of the tool with clean,
dry cloth, and apply a thin coat of tool oil.
Then store the tool indoors out of children's reach.
SAFETY
OPERA
TION
MAINTENANCE
SETUP