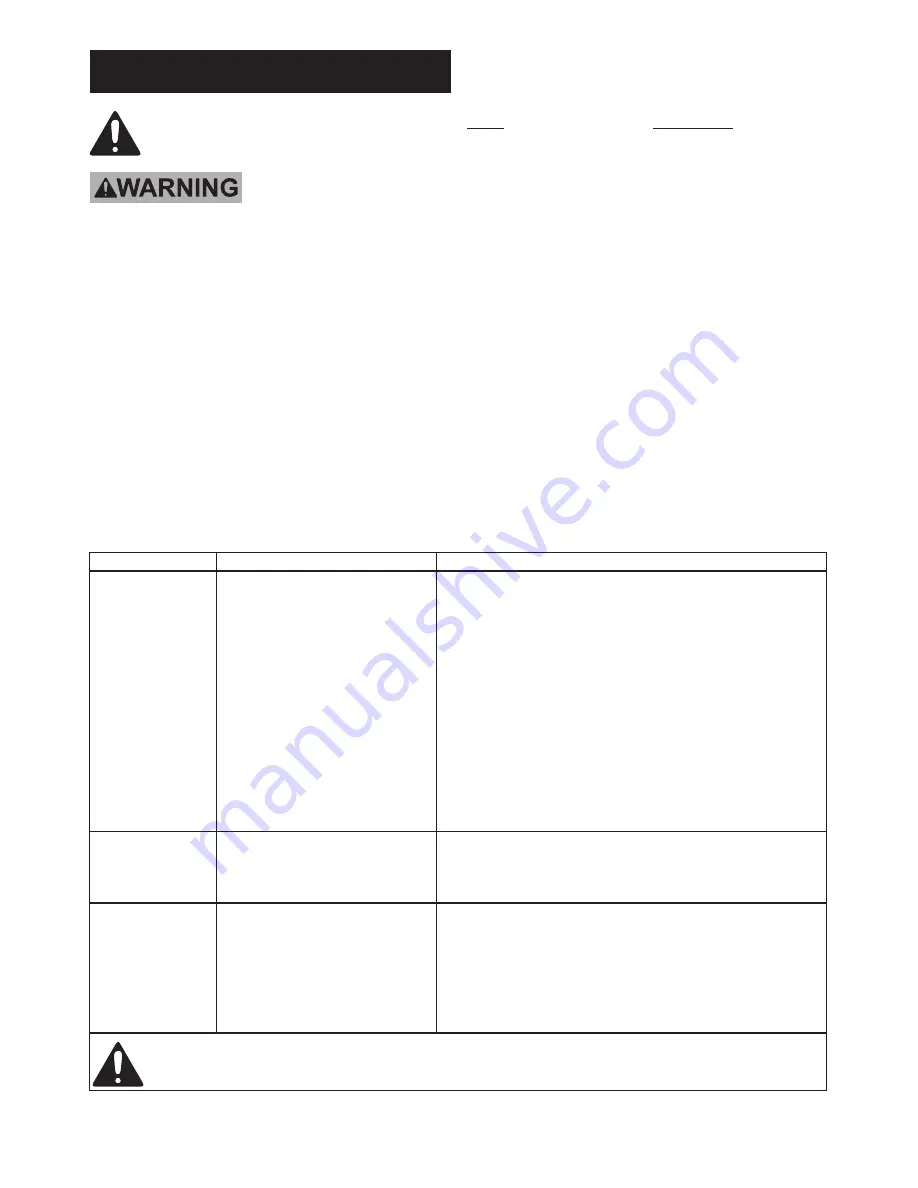
Page 9
For technical questions, please call 1-800-444-3353.
Air Ratchets
User-Maintenance Instructions
Procedures not specifically explained
in this manual must be performed
only by a qualified technician.
TO PREVENT SERIOUS INJURY FROM
ACCIDENTAL OPERATION:
Detach the air supply, safely discharge any residual
air pressure in the tool, and release the throttle and/
or turn the switch to its off position before performing
any inspection, maintenance, or cleaning procedures.
TO PREVENT SERIOUS INJURY
FROM TOOL FAILURE:
Do not use damaged equipment.
If abnormal noise, vibration, or leaking air occurs,
have the problem corrected before further use.
Cleaning, Maintenance,
and Lubrication
Note:
These procedures are in addition to the
regular checks and maintenance explained as part
of the regular operation of the air-operated tool.
1.
Daily - Air Supply Maintenance:
Every day, perform maintenance on the air supply
according to the component manufacturers’
instructions. The lubricator’s oil level needs to be
maintained and the moisture filter must be regularly
drained. Performing routine maintenance on
the air supply will allow the tool to operate more
safely and will also reduce wear on the tool.
2.
Weekly - Grease Lubrication:
Lubricate the internal mechanism of the tool, using
white lithium grease through the grease fittings.
Troubleshooting
Problem
Possible Causes
Likely Solutions
Decreased output. 1. Not enough air pressure and/
or air flow.
2. Obstructed trigger.
3. Incorrect lubrication or
not enough lubrication.
4. Blocked air inlet screen
(if equipped).
5. Air leaking from loose housing.
6. Mechanism contaminated.
7. Vane wear or damage.
1. Check for loose connections and make sure that
air supply is providing enough air flow (CFM)
at required pressure (PSI) to the tool’s air inlet.
Do not exceed maximum air pressure.
2. Clean around trigger to ensure free movement.
3. Lubricate using air tool oil and grease
according to directions.
4. Clean air inlet screen of buildup.
5. Make sure housing is properly assembled and tight.
6. Have qualified technician clean and lubricate
mechanism. Install in-line filter in air supply
as stated in Initial Set Up: Air Supply.
7. Replace all vanes.
Housing heats
during use.
1. Incorrect lubrication or
not enough lubrication.
2. Worn parts.
1. Lubricate using air tool oil and grease
according to directions.
2. Have qualified technician inspect internal
mechanism and replace parts as needed.
Severe air leakage.
(Slight air leakage
is normal,
especially on
older tools.)
1. Cross-threaded housing
components.
2. Loose housing.
3. Damaged valve or housing.
4. Dirty, worn or damaged valve.
1. Check for incorrect alignment and uneven gaps.
If cross-threaded, disassemble and
replace damaged parts before use.
2. Tighten housing assembly. If housing cannot tighten
properly, internal parts may be misaligned.
3. Replace damaged components.
4. Clean or replace valve assembly.
Follow all safety precautions whenever diagnosing or servicing the tool.
Disconnect air supply before service.