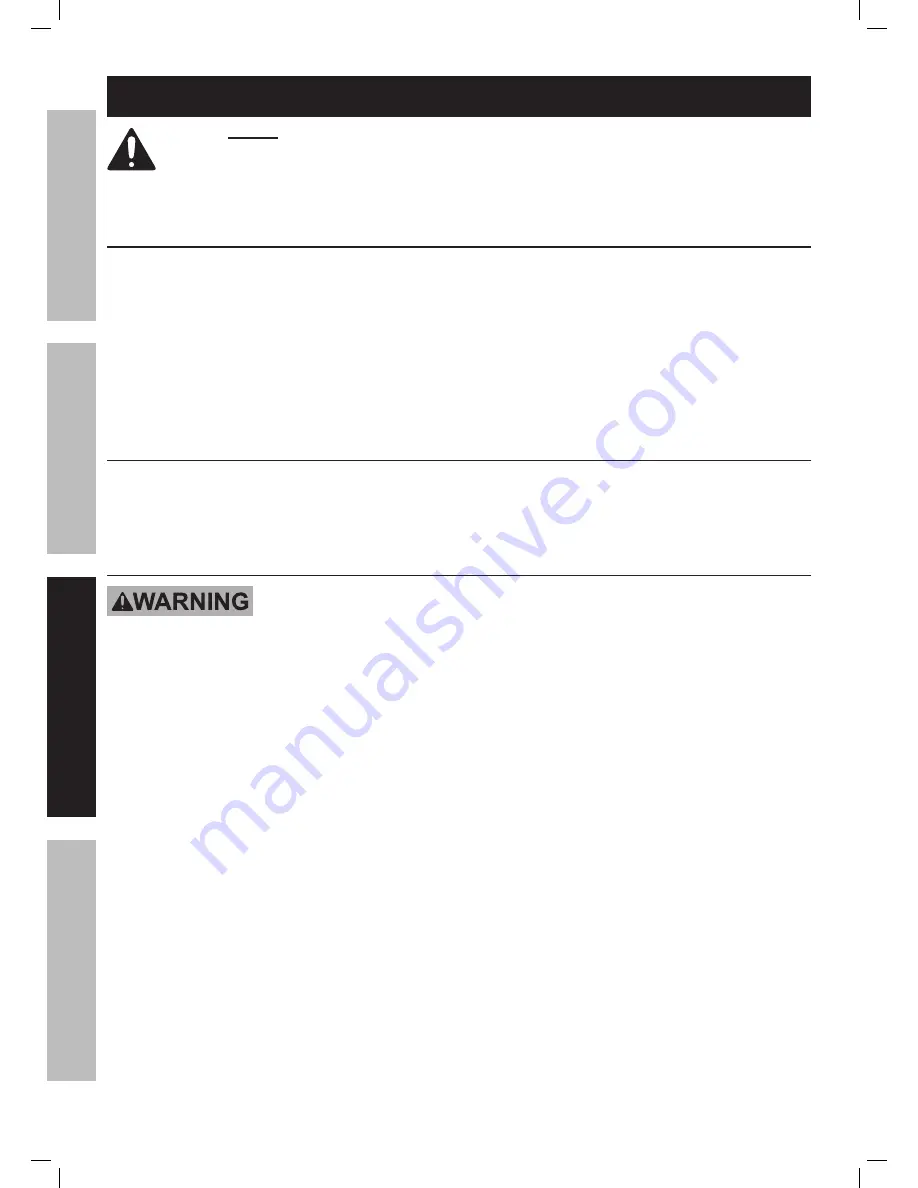
Page 10
For technical questions, please call 1-800-444-3353.
Item 68028
68068
Operating Instructions
Read the ENTIRE IMPORTANT SAFETY INFORMATION section at the beginning of this
manual including all text under subheadings therein before set up or use of this product.
Inspect tool before use, looking for damaged, loose, and missing parts.
If any problems are found, do not use tool until repaired.
Work Piece and Work Area Set Up
1. Designate a work area that is clean and well-lit.
The work area must not allow access by children
or pets to prevent distraction and injury.
2. Route the air hose along a safe route to reach
the work area without creating a tripping hazard
or exposing the air hose to possible damage.
The air hose must be long enough to reach
the work area with enough extra length to
allow free movement while working.
3. Secure loose workpieces using a vise or clamps
(not included) to prevent movement while working.
4. There must not be hazardous objects
(such as utility lines or foreign objects) nearby
that will present a hazard while working.
Single Sequential Safety Trip Mechanism Definition
This tool has a single sequential safety trip mechanism, which is designed to prevent inadvertent firing.
The tool should only fire if the Safety Nosepiece is pressed against the workpiece prior to
pulling the Trigger. It should only fire again if the trigger is released and squeezed again.
The Tool should not fire if the Safety Nosepiece is not pressed against an object.
Single Sequential Safety Trip Mechanism Testing Procedure
TO PREVENT SERIOUS INJURY FROM ACCIDENTAL OPERATION:
Empty the tool before this procedure. Point the tool at a piece of scrap wood when testing.
1. Disconnect the tool from the air supply.
2. Empty the magazine of fasteners.
3. Check that the Trigger and the Safety Nosepiece
move freely, without sticking.
4. Connect the air supply to the tool and
set within the Operating Air Pressure
indicated on the Specification chart.
5. Test the tool by pressing the Safety Nosepiece
against the workpiece without pulling the Trigger.
The tool must not cycle (fire).
If it cycles (fires),
stop immediately and have it repaired
by a qualified service technician.
6. Hold the tool away, or off of the workpiece.
The Safety Nosepiece should return to its original
position. Squeeze the Trigger.
The tool must not
cycle (fire).
If it cycles (fires), stop immediately
and take the tool to a qualified service technician.
7. Press the Safety Nosepiece against the workpiece
and squeeze the Trigger.
The tool must
cycle (fire) only once.
Release the trigger and
squeeze it again.
The tool must cycle (fire)
again only once.
With the Trigger held, carefully
lift the tool and press it against the workpiece
again.
The tool must not cycle (fire).
If it fails
to act in the manner explained in bold, have it
repaired by a qualified service technician.
SAFETY
OPERA
TION
MAINTENANCE
SETUP