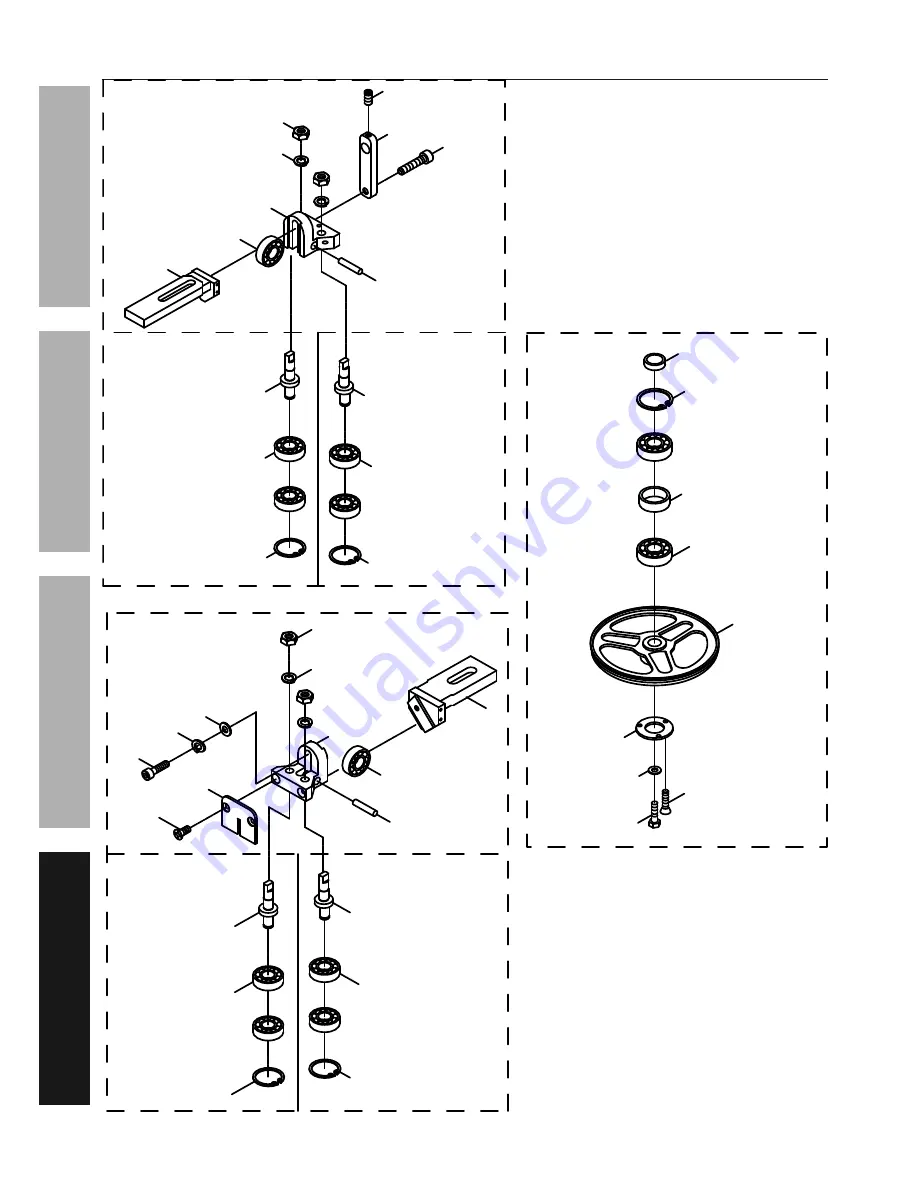
Page 26
For technical questions, please call 1-888-866-5797.
Item 63469
S
AFET
y
Op
ERA
TION
M
AINTENAN
c
E
S
ETU
p
Assembly Diagrams - continued
268-2(2)
268S
267-3
268-3
267S
250-3
271-1
250-8
250-9
250-6
267-2(2)
268-1
267-1
266-6
266-3
266-7(2)
266-10
266-11
266-2
266-5
266-4
266-1
250S
250-7(3)
271S
266S
266-8(2)
266-9(2)
271-3
270-3
270S
270-2(2)
271-2(2)
270-1
250-4(2)
250-1
250-5
269-7
269S
269-1
269-3
269-4
269-2
269-6(2)
269-5(2)
269-9
269-8
250-2