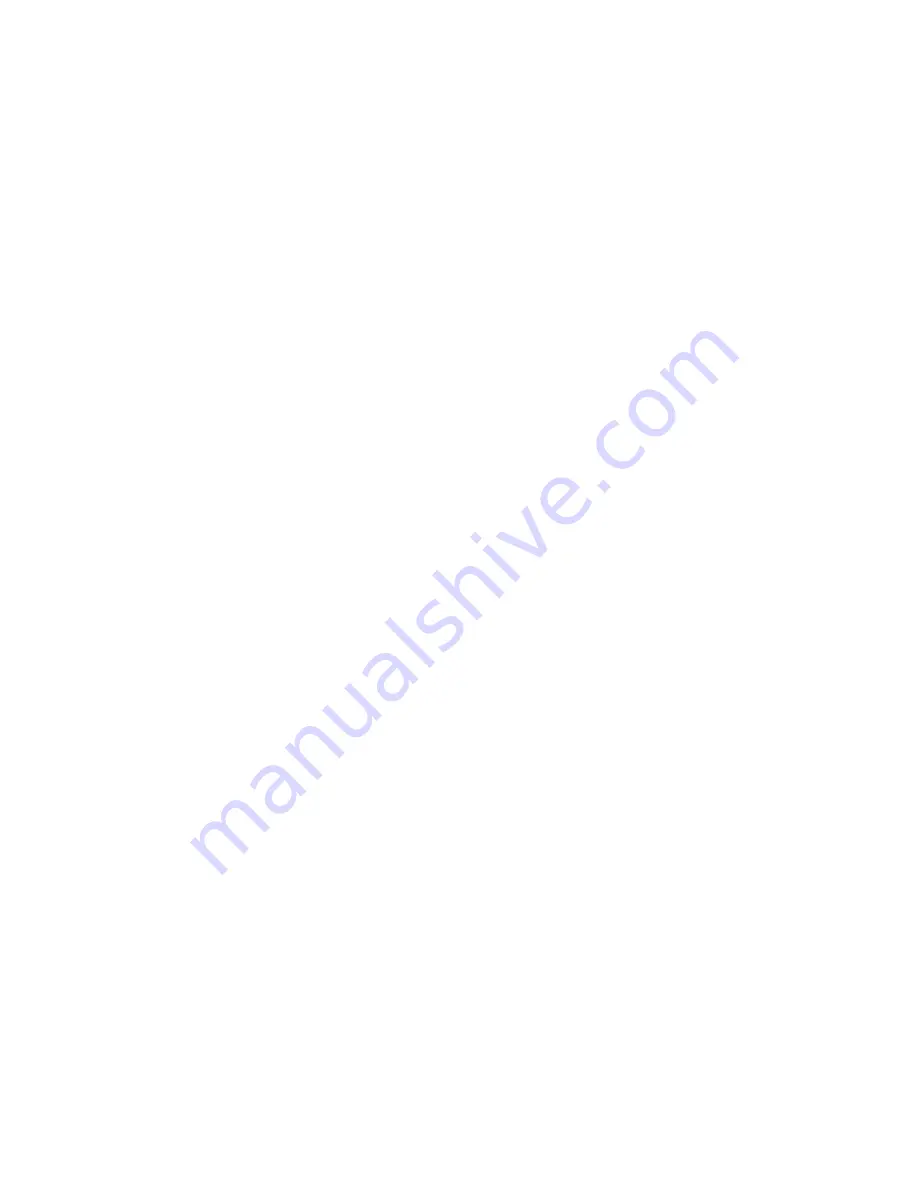
Page 3
SKU 44846
5.
do not force tool
. It will do the job better and more safely at the rate for which it
was intended. Do not use inappropriate attachments in an attempt to exceed the tool
capacity.
6.
use the right tool for the job
. Do not attempt to force a small tool or attachment to
do the work of a larger industrial tool. There are certain applications for which this tool
was designed. Do not modify this tool and do not use this tool for a purpose for which
it was not intended.
7.
dress properly
. Do not wear loose clothing or jewelry as they can be caught in
moving parts. Protective, electrically non-conductive clothes and non-skid footwear
are recommended when working. Wear restrictive hair covering to contain long hair.
8.
use eye and ear protection
. Always wear ANSI approved impact safety goggles.
Wear a full face shield if you are producing metal filings or wood chips. Wear an ANSI
approved dust mask or respirator when working around metal, wood, and chemical
dusts and mists.
9.
do not overreach
. Keep proper footing and balance at all times. Do not reach over or
across running machines.
10.
Maintain tools with care
. Keep tools sharp and clean for better and safer
performance. Follow instructions for lubricating and changing accessories. Inspect tool
cords periodically and, if damaged, have them repaired by an authorized technician.
The handles must be kept clean, dry, and free from oil and grease at all times.
11.
disconnect power
. Unplug when not in use.
12.
remove adjusting keys and wrenches
. Check that keys and adjusting wrenches
are removed from the tool or machine work surface before plugging it in.
13.
avoid unintentional starting
. Be sure the switch is in the Off position when not in
use and before plugging in.
14.
stay alert
. Watch what you are doing, use common sense. Do not operate any tool
when you are tired.
15.
take caution as some woods contain preservatives such as copper chromium
arsenate (cca) which can be toxic
. When cutting these materials extra care should
be taken to avoid inhalation and minimize skin contact.
16.
check for damaged parts
. Before using any tool, any part that appears damaged
should be carefully checked to determine that it will operate properly and perform its
intended function. Check for alignment and binding of moving parts; any broken parts
or mounting fixtures; and any other condition that may affect proper operation. Any
part that is damaged should be properly repaired or replaced by a qualified technician.
Do not use the tool if any switch does not turn On and Off properly.
17.
guard against electric shock
. Prevent body contact with grounded surfaces such as
pipes, radiators, ranges, and refrigerator enclosures.
18.
replacement parts and accessories
. When servicing, use only identical