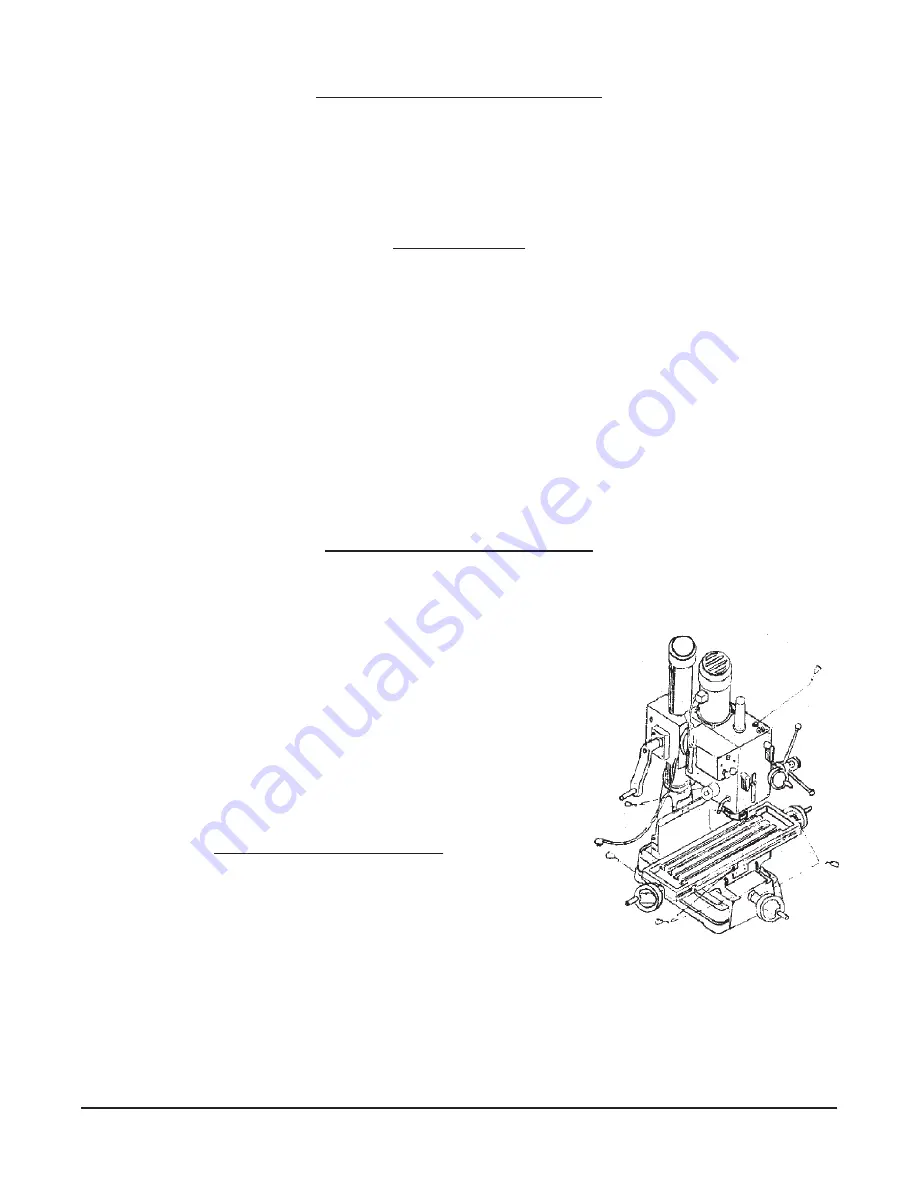
Page 6 SKU # 42827
UNPACKING AND INSTALLATION
1.
Remove protective crating and skids carefully. In the event of damage in transit, contact Harbor Freight
Tools immediately.
2.
Read the owner’s manual and become familiar with the parts and controls on the drawings before
using this machine, as familiarity with the controls will enhance your ability and safety in using it.
INSTALLATION
1.
It is important that the machine be located on a hard, solid, level floor. Find a location that
supplies easy access to 110 Volt electrical service. Make sure this machine is located in a well
lighted and well ventilated area. The floor should be resistant to vibration.
2.
Before moving the machine, be sure the head is fixed on the column. Before moving the machine, lower
the head as much as possible to lower the center of gravity. When moving the machine be careful to
keep it balanced, and not allow it to topple over.
3.
To set the machine on a solid concrete foundation, it’s advisable to apply a little grout to touch up
any uneveness in the concrete in order to get a solid foundation at all points.
4.
When setting machine on a floor that has any surface irregularities, shims should be used to
correct this condition to the greatest extent possible.
5.
There are 4 holes in the base for mounting the machine permanently to a smooth, solid, and level floor.
CLEANING AND LUBRICATION
1.
Thoroughly clean the machine with a commercial degreaser.
Do not use gasoline, kerosene or other flammable liquids.
Avoid getting solvent on rubber parts, or into the electrical
controls or motor.
2.
After cleaning, coat all bright metal with a light lubricant to
prevent corrosion.
3.
Lubricate all points indicated in
Figure 2
with a 10 weight
machine oil.
4.
Remove the oil filler plug and fill the reservoir with heavy motor
oil, until the oil level reaches the middle of the oil fluid level
indicator. Replace the plug.
LEVELING THIS MACHINE
1.
Before operation, it is critical to level the work surface both
lengthwise and crosswise, using a precision level. It will not be
possible to maintain accuracy of machined parts if the mill is not
properly leveled to start.
Figure 2. Lubrication Points.