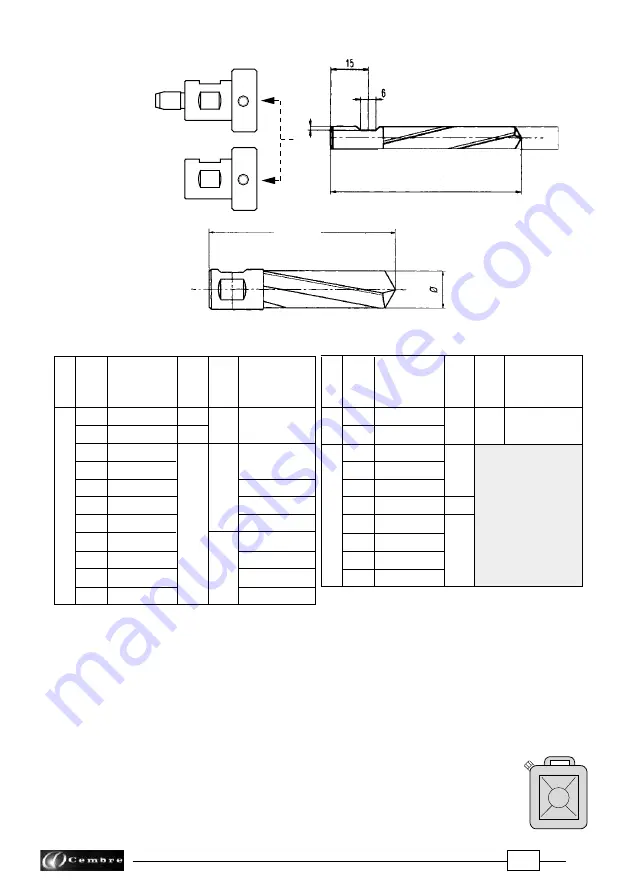
8
FIG. 1
FIG. 2
The drilling tools indicated in the table guarantee optimum results. For tools of other types, check the dimen-
sional compatibility (particularly the size of the attachment and the length).
3.10) LR2 BIODEGRADABLE LUBROCOOLANT
3 litre container to be used in a 5-10 % solution, for optimum operation of both broach cutters
and
spiral bits.
3.11) LR3 ANTIFREEZE CONCENTRATE
3 litre added to the lubrocoolant mixture in the right concentration will
maintain the lubrocoolant mixture fluid in negative temperature conditions.
– The special spiral bits in the
PE
range allow automatic cooling by means of the
SR5000
u
nit supplied with
the drilling machine.
– All spiral bits in the
PE
range allow drilling of
thicknesses up to 45 mm.
L max
ø
APED...
APE...
ø
L max
h
3.9) Spiral bits
7
7,1
8
8,5
9
9,5
10
11
12
13
13,5
SPECIAL SPIRAL BITS FOR RAILS IN STEEL QUALITY 700 - 900 - 1100 (UIC 860.0)
PE 140
PE 160
PE 170AR
PE 175
PE 180
PE 190AR
PE 210AR
PE 220
PE 240AR
PE 275AR
Ø
mm
14
16
17
17,5
18
19
21
22
24
27,5
Adaptor
ref.
Figur
e
h
mm
L
max
mm
APED 135/165
Spiral Bit
ref.
(*)
PE 70
PE 71
PE 80
PE 85
PE 90
PE 95
PE 100
PE 110
PE 120
PE 130AR
PE 135AR
Ø
mm
Adaptor
ref.
h
mm
L
max
mm
APE 90
APE 95
APE 100
APE 110
APE 120
APED 130
Figur
e
1
1
2
(*) PE
... AR
:
special high qualit
y spir
al bit
.
Spiral Bit
ref.
(*)
1,6
76
76
1,6
APED 70
1,2
88
85
88
APED 80
APED 135/165
76
72
1,4
3l