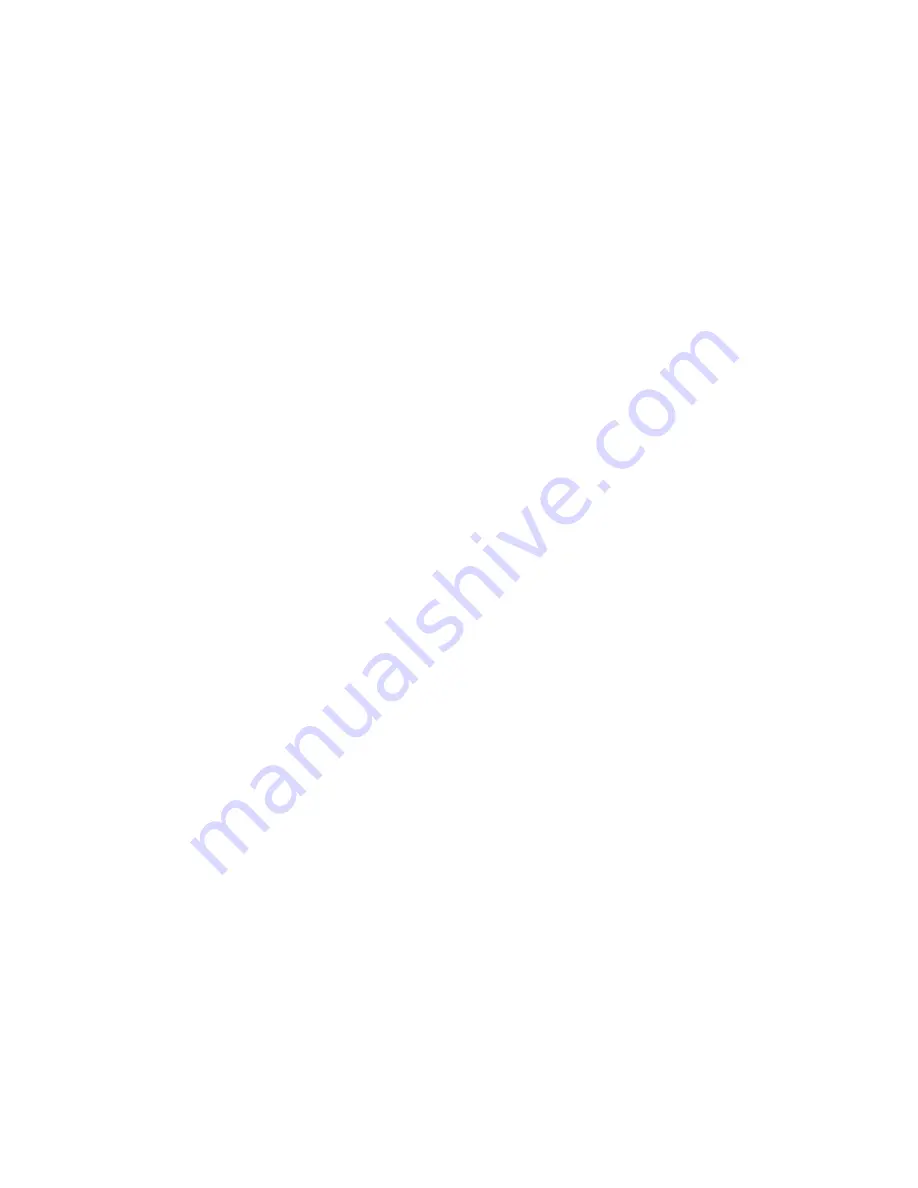
17
DISASSEMBLY AND RE-ASSEMBLY PROCEDURES
WARNING:
Work must be performed only by thoroughly trained and qualified
personnel to assure quality repair and to reduce the possibilities of
injury to personnel and/or damage to equipment. If you do not
have personnel who are capable of safe quality repair of this equip-
ment, we advise you to return the equipment to DEAN PUMP to be
repaired.
When it is necessary to open the pump and/or the pumping system
the fluid will be exposed to the atmosphere and personnel in the
area. For the safety of all involved, the risk of exposure of personnel
to the hazards of the pumpage can be reduced by flushing the entire
system with a compatible, nontoxic, non-hazardous, stable liquid
before opening the pump or the system. In all cases, where the sys-
tem is flushed or not, use the utmost care around the pumpage and
the pumping system.
Always wear the appropriate protective apparel when working on
or around the pumping equipment. Safety glasses with side shields,
heavy work gloves (use insulated work gloves when handling hot
items), steel-toed shoes, hard hat, and any other protective gear as
needed for protection. One example of other gear would be breath-
ing apparatus when working near toxic materials.
Use only top quality tools.
a) Stop the pump. Turn off the power supply (electricity, steam,
etc.) to the pump driver (motor, turbine, engine, etc.) and lock
the switching device so that it can not be restarted. Tag the
switching device so that no one will attempt to restart the unit.
b) Close the suction and discharge valves completely to isolate the
pump from the system. Lock the valves in the closed position
and tag them so that no one will attempt to open them.
c) Turn off, lock out, and tag all sub-systems and auxiliary equip-
ment and auxiliary supply lines to isolate the pumping unit from
any and all power, energy, and/or fluids.
WARNING:
Do not attempt to perform any work on the unit until you are confi-
dent that the pump and its contents have been stabilized at ambient
temperature, and atmospheric pressure.
Put on protective wear to protect human tissue from attack by the
fluids contained in the pump and any sub-systems, and from any
vapors or fumes that could possibly be released from these fluids.
This could mean breathing apparatus face shields, heavy long sleeve
rubber gloves, rubber apron, hood, and possibly more, dependent,
of course, on the properties of the fluids involved and the installed
drain and vent piping arrangement. Personal injury and/or death
can occur if adequate precautions are not taken with regard to the
fluid, the installation and the possibilities of the release of fluid,
vapors, and/or fumes.
d) Remove the coupling guard(s).
e) If the pump and driver are independently mounted to a
common baseplate (not connected to each other with a motor
support (83)), remove the spacer section of the coupling.
Remove the two bolts that secure the bearing housing foot (9) to
the baseplate. Go to step (j).
f) If the pump and driver (motor or turbine) are connected togeth-
er by a “C” faced motor support (83), disconnect the power
supply from the driver. Remove any conduit and/or piping from
the driver. Place wood blocks and wedges, under the rear feet
of motors sizes 143TC through 215TC, or under the motor sup-
port (83) of motors sizes 254TC thru 365TC. These blocks are
to be positioned so as to support the weight of the motor and
the motor support (83) when they are separated from the
pump. Hook a lifting hoist to the lifting eye(s) of the motor and
take the slack out of the cable or chain. Make sure that all of
the components of the lifting apparatus are capable of lifting
the weight.
g) For units with motor sizes 143TC through 215TC, remove the
two bolts that fasten the motor support (83) to the baseplate.
For units with motor sizes 254TC trough 365TC, remove the
two bolts that fasten the rear feet of the motor to the baseplate.
h) Remove the four bolts that fasten the motor support (83) to the
back of the pump. Be careful to support the weight of the motor
and motor support (83) as you are removing these bolts.
Carefully move the motor and motor support (83) assembly hor-
izontally and axially away from the pump, guiding the assem-
bly to clear the pump coupling hub.
i) Remove the coupling elastomer, from the coupling hub. The
elastomer may be in either the pump hub or the motor hub.
j) Drain all the fluids from all the auxiliary sub-systems (lubrication,
cooling, heating, seal barrier, etc.) that are connected to the
pump. Drain each fluid into a separate container. Use caution
required for each fluid after reading the MSDS (Material Safety
Data Sheet) for each.
k) Flush each sub-system with a compatible, non-toxic, non-haz-
ardous, stable liquid. Drain into individual containers for each
fluid. Disconnect and remove all auxiliary piping.
l) Carefully bleed off any pressure remaining in the pump.
Pressure remaining in the pump will be dependent upon the
pressure in the system when the pump was stopped; the quality,
type, and condition of the isolation valves; the thermal expan-
sion values of the fluid and the pump material; and the change
in the vapor pressure of the fluid between the temperature at the
time the isolation valves were closed and the ambient tempera-
ture. Bleeding must be through a valved drain line piped to a
closed container mounted lower than the pump. The container
must be arranged with a relief passage to some point where
pressure and fumes will not be harmful to personnel. The con-
tainer must also have a level device so that determination can
be made that sufficient fluid has been drained to empty the
pump cavity and the volume of fluid that was contained in the
run of suction and discharge pipe between the isolation valves
and the pump. After the initial rush of fluid from the pump
relieves the pressure, the drain valve can be opened further to
speed the draining operation. When fluid quits running into the
drain tank, gage the volume to see if it is sufficient to have fully
drained the contents of the pump and the suction and dis-
charge pipes between the isolation valves.
If the system was constructed without any drain connections, it
will be necessary to consult the designers of the system for safe
draining procedures.
m) Now drain any small piping, that contains the fluid pumped,
from all low points into the same container used to drain the
pump. Do not drain any other fluids (different than the
pumpage) into this container as they may not be compatible.
Personal injury, death, and/or equipment damage could occur.
WARNING:
Even though it might appear that the cavity being drained has com-
pletely drained, be extremely careful about opening the system
and/or opening the pump. If something solid in the pumpage moves
to the vicinity of the drain connection, it could seal-off the drain and
maintain pressure in the cavity thought to have been drained. It is