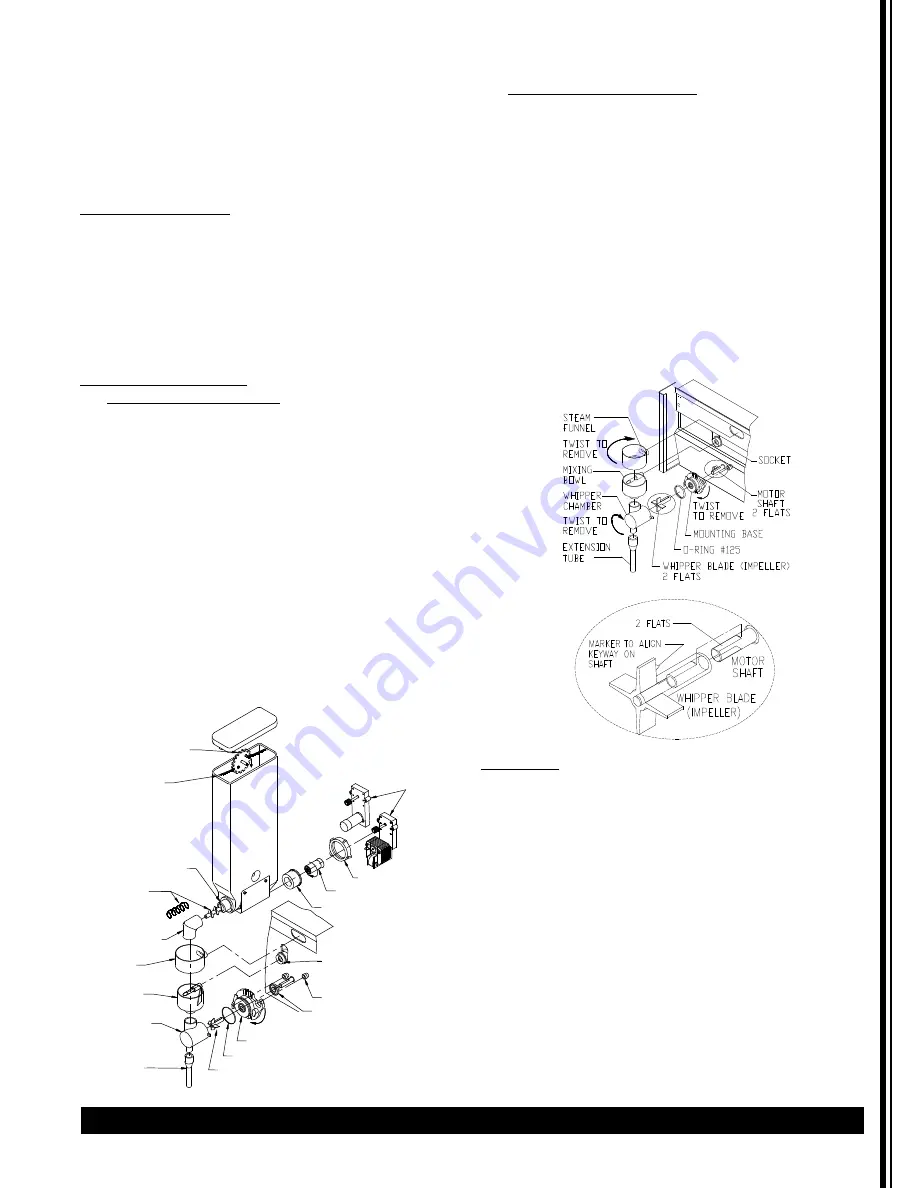
GB Series
Cecilware
®
7
NOTICE:
All sanitizing agents in the food zone must
comply with 21 CFR 178.1010.
Sanitize all food dispensing units periodically. All parts
to be sanitized must be cleaned first. Cleaning and
sanitizing frequency must follow state and local health
department regulations.
Daily maintenance:
1. Rinse whipper chambers
• Position a container under dispense tubes.
• Move rinse switch to "rinse".
• Push and hold each dispense button 10 seconds.
• Move rinse switch to "serve".
2. Empty drip tray, wash, rinse, and sanitize.
3. The outside of the machine can be cleaned with
warm soapy water and a damp cloth.
Weekly maintenance:
1. Product hopper cleaning
• Rotate product guides up, remove hoppers from
machine.
• Empty powder into pans.
• Pull off product guides.
• Remove agitator wheels.
• Unscrew and remove front and back auger locks.
• Remove auger.
• Wash, rinse, sanitize, and air dry all small parts.
• Wash & scrub hoppers and agitator wheel recesses
with bristle brush. Rinse, sanitize, and allow to air
dry.
• Reassemble all hoppers.
• Pour powder into hoppers.
• Install all hoppers into unit.
2. Whipper chamber cleaning
• Remove dispense caps by turning and lifting.
• Remove mixing bowls by lifting and pulling.
• Remove product tubes by pulling down.
• Twist off whipping chambers clockwise.
• Pull off whipper blades.
• Twist off whipper chamber mounts clockwise.
• Remove O-rings.
• Remove tray by pulling levers down.
• Remove both powder trays by pulling levers out.
• Wash, rinse, and sanitize small parts and interior
machine surfaces.
• Reassemble all small parts.
Note:
When reassembling, align flat keyway inside
blade with flat keyway of motor shaft. Push the
whipper blade all the way on.
Sanitizing
1. Prepare a sanitizing solution in accordance with
local health department regulations. You may also
refer to the US Food and Drug Administration
regulation 21 CFR 178.1010 “Sanitizing Solutions”
and US Environmental Protection Agency 40 CFR
18.940 “Tolerance exemptions for active and inert
ingredients for use in antimicrobial formulations
(Food-contact surface sanitizing solutions)”.
2
Follow the instructions provided with the sanitizing
agent.
3 Let all sanitized parts drain and air dry. DO NOT
WIPE THEM DRY.
Cleaning
A
U
G
E
R
B
U
SH
I
NG
-
BAC
K
AG
I
TATOR
G
E
AR
AG
I
TATOR
W
I
R
E
A
U
G
E
R
B
U
SH
I
NG
F
RONT
A
U
G
E
R
PROD
U
CT
G
UI
D
E
D
I
SP
E
NS
E
C
U
P
M
I
X
I
NG
CHAMB
E
R
WH
I
PP
E
R
CHAMB
E
R
WH
I
PP
E
R
B
L
AD
E
'
O
'-
R
I
NG
#125
MO
U
NT
I
NG
BAS
E
TW
I
ST
TO
R
E
MOV
E
S
LI
NG
E
R
D
I
SC
BAS
E
MO
U
NT
GROMM
E
T
M
I
X
BOW
L
SOC
KE
T
A
U
G
E
R
MOTOR
N
U
T
[2]
E
XT
E
NS
I
ON
T
U
B
E
FL
ANG
E/
N
U
T