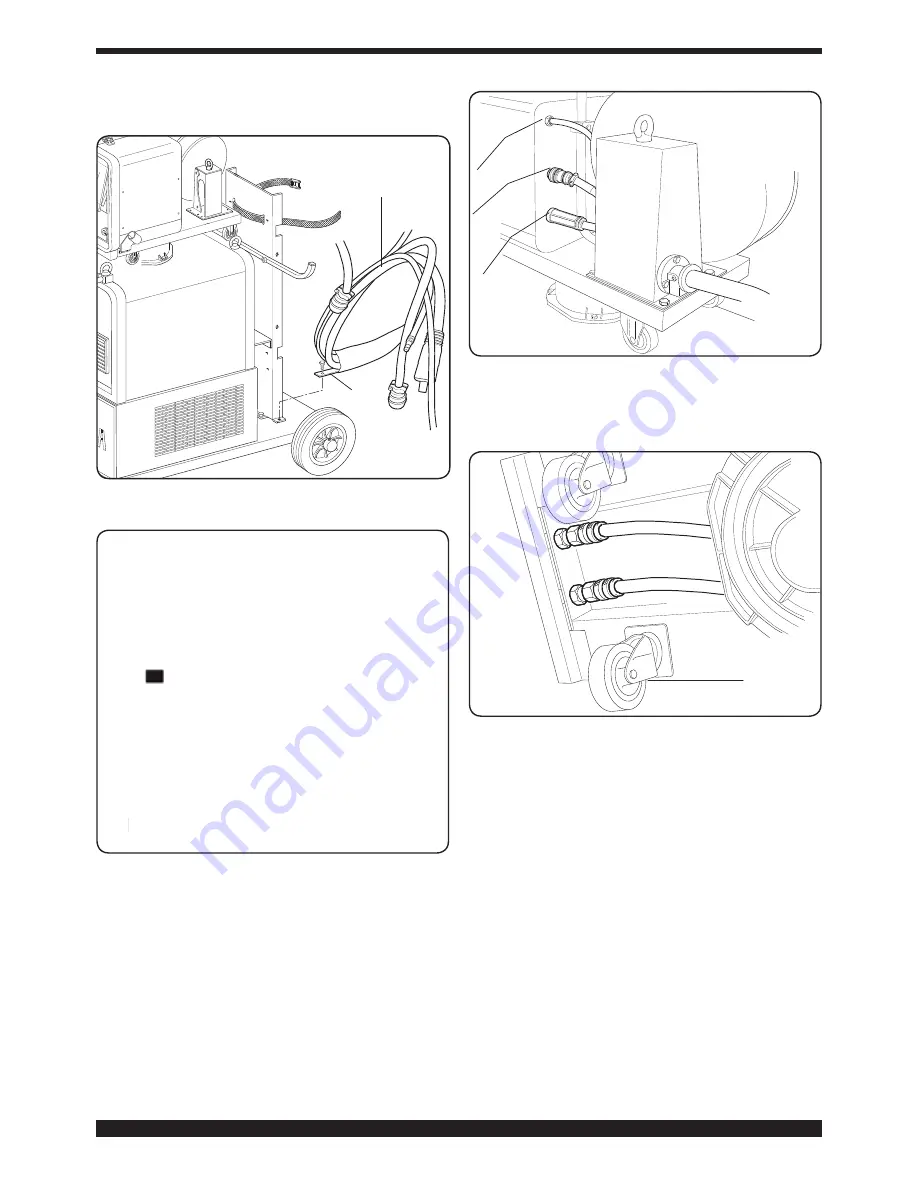
23
• Block one end of connection
BA
, by fi xing the tip
BB to
the bottom of the machine as shown in fi g. 4.
Fig. 4
BA
BB
• Connect all wiring on the back of the power source, as
shown in fi g. 5.
Fig. 5
• Avoid coiling the connection to reduce to a minimum
the inductive effects that could affect welding results.
• Connect the other end of connection BA to the wire
feeder trolley as shown in fi g. 6.
Fig. 6
11
20
19
• The coolant fl uid hoses must be connected to the
quick-fi tting valves located below the lower part of the
wire feeder trolley (see fi g. 7), by matching the colours
appearing on the trolley front side.
Fig. 7
• Position the cylinder on the support and fi x it with the 2
straps; ensure that the straps are secured tightly to the
cylinder to prevent dangerous tilting.
• Connect the gas hose to the outlet of the pressure regulator.
• Open the side door.
• Connect the power cord to the socket
4 and through
the clamp to the workpiece.
• Connect the earth lead clamp
4 to the piece to be welded.
• Fit the wire coil on the support inside the compartment.
The coil must be fi tted so that the wire unwinds in an
anticlockwise direction.
• Make sure the drive roller is correctly positioned according
to the diameter and type of wire used.
• Cut the welding wire with a well-sharpened tool, keeping
it between your fi ngers so that it cannot unwind, insert it
inside the pipe exiting from the gear motor and, with the aid
of a fi nger, insert it inside the steel tube until it comes out of
the adapter.
• Fit the welding torch.
After fi tting the reel and torch, switch on the machine, select
the suitable synergic curve, following the instructions given