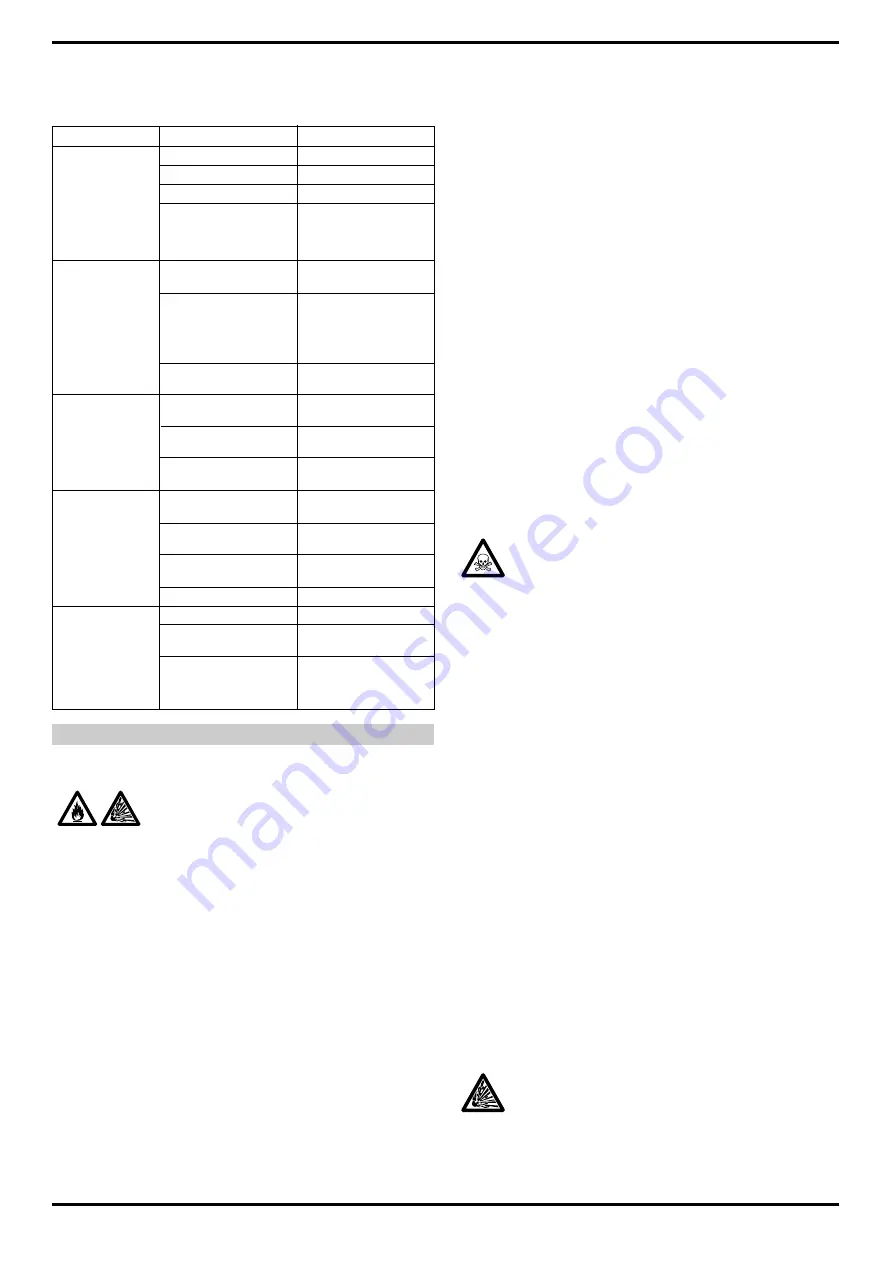
tect your skin against burns caused by ultraviolet radiation
given off by the arc, and from weld metal sparks and slag.
l
Wear protective clothing-gauntlet gloves designed for
use in welding, hat and high safety-toe shoes. Button shirt
collar and pocket flaps, and wear cuff-less trousers to
avoid entry of sparks and slag.
l
Wear helmet with safety goggles and glasses with side
shields underneath, appropriate filter lenses or plates
(protected by clear cover glass). This is a MUST for wel-
ding to protect the eyes from radiant energy and flying
metal. Replace cover glass when broken, pitted, or spat-
tered.
l
Avoid oil or greasy clothing. A spark may ignite them.
Hot metal such as electrode stubs and workpieces should
never be handled without gloves.
l
First-aid facilities and a qualified first-aid person should
be available for each shift unless medical facilities are
close by for immediate treatment of flash burns of the eyes
and skin burns.
l
Ear plugs should be worn when working on overhead or
in a confined space. A hard hat should be worn when
others work overhead.
l
Flammable hair preparations should not be used by per-
sons intending to weld or cut.
7.3 FUMES
Welding operations give off harmful fumes and
metal dusts which may be hazardous to your
health, therefore:
l
Work in a well-ventilated area.
l
Keep your head out of fumes.
l
In closed areas, use suitable exhaust fans.
l
If ventilation is not enough, use breathing sets approved
for this procedure.
l
Clean the material to be welded of any solvents or halo-
gen degreasers giving rise to toxic gases. Some clorine
solvents may decompose with the radiation emitted by the
arc, and create phosgene gas.
l
Do not weld plated metals or those containing lead,
graphite, cadmium, zink, chrome, mercury or beryllium,
unless you have the proper breathing set.
l
The electric arc creates ozone. A long exposure to high
concentrations may cause headaches, nasal, throat and
eye irritation as well as serious congestions and chest
pains.
IMPORTANT: DO NOT USE OXYGEN FOR VENTILA-
TION.
l
Gas leaks in a confined space should be avoided.
Leaked gas in large quantities can change oxygen con-
centration dangerously. Do not bring gas cylinders into a
confined space.
l
DO NOT WELD where solvent vapors can be drawn into
the welding atmosphere or where the radiant energy can
penetrate to atmospheres containing even minute
amounts of trichloroethylene or perchloroethylene.
7.4 EXPLOSIONS
Do not weld above or near containers under pres-
sure.
l
Do not weld in environments containing explosi-
ve dusts, gases or vapours.
This welding machine uses inert gases such as CO2,
ARGON, or a mixture of ARGON + CO2 for the protection
5
6.3 TROUBLESHOOTING GUIDE GUIDE
7 SAFETY PRECAUTIONS
7.1 FIRE
l
Avoid causing fire because of sparks,
slag, hot metal or pieces.
l
Make sure that suitable fire-fighting equip-
ment is available close to welding area.
l
Remove all flammable and combustible material from
the welding area and its surrounding (32 ft minimum).
l
Do not weld containers of combustible or flammable
material, even when empty. These must be carefully clea-
ned before being welded.
l
Allow the welded material to cool down before touching
it or putting it in contact with combustible or flammable
material.
l
Do not weld parts with hollow spaces, containing flam-
mables.
l
Do not work under conditions with high concentrations of
combustible vapours, gases, or flammable dust.
l
Always check the work area half an hour after welding
so as to make sure that no fire has started.
l
Do not keep any combustible material such as lighters or
matches in your pockets.
7.2 BURNS
l
Wear fire-proof clothing all over your body in order to pro-
ROUBLE
The welding machi-
ne supplies limited
current
Welding with a lot
of metal spatter
The wire jams or
entangles between
the drive rolls and
the torch infeed wire
guide
No wire feed or irre-
gular wire feed
Porosity in the wel-
ding seam
PROBABLE CAUSE
Line fuse blown
Burnt out diode or diodes
Burnt out electronic board
Loosened torch or earth
connections or any other
electrical power connec-
tions
Voltage adjustment switch
has a loose contact
Improper adjustment of
welding parameters
Insufficient grounding
Contact tip with wrong dia-
meter
Misalignment of the drive
roll groove
Obstructed or clogged
liner
Drive roll with too large a
groove
Obstructed or clogged
liner
Wire holding roller not
completely tightened
Clogged contact tip
Insufficient shielding gas
Excess oxidation of the
edges to be welded
Gas nozzle partially or
completely clogged by
spatter
REMEDY
Replace line fuse
Replace
Replace
Tighten all connections
Replace the switch
Select the correct parame-
ters through the welding-
voltage switch and the
wire-speed adjustment
potentiometer
Check grounding connec-
tions
Replace
Realign
Remove and clean
Replace the drive roll
Remove and clean
Tighten all the way
Replace
Increase gas delivery
Thoroughly clean the
edges with a metal brush
Remove and clean or
replace being careful not
to clog the gas outlets
Summary of Contents for MIG WELDER
Page 8: ...8 ...