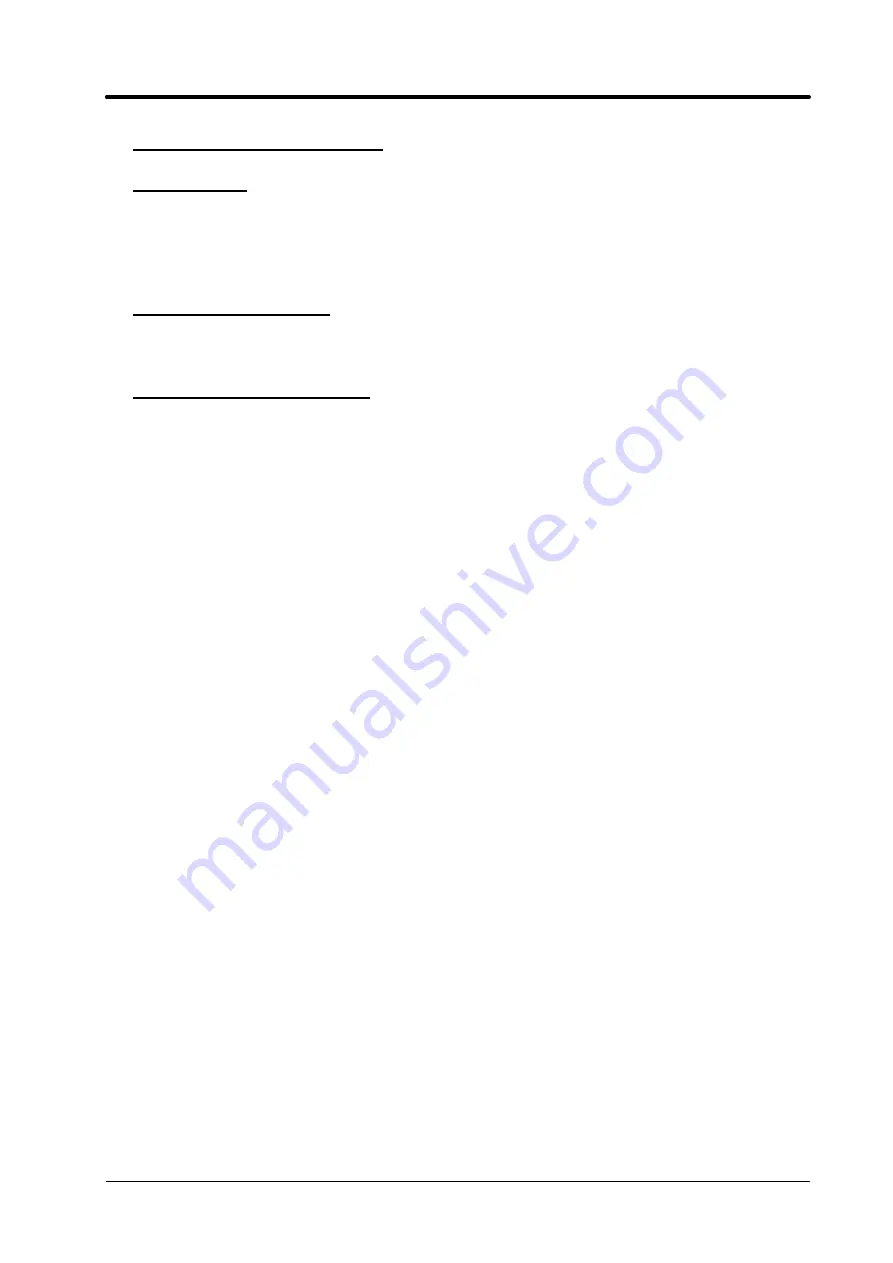
CEBORA S.p.A.
4
3.302.155
22/01/04
2
- SYSTEM DESCRIPTION
2.1
- Introduction.
The BRAVO MIG system is made up of equipment for welding mild steel, stainless steel and
aluminum using the MIG process. Each piece of equipment essentially consists of an electric
power source with built-in wire feed unit.
The power sources that make up the series include arts. 574, 575, 591 and 593.
2.2
- Technical specifications.
To verify the technical specifications, see the machine plate, Instruction Manual, and Sales
Catalogue.
2.3
- Description of power sources.
The articles in the BRAVO MIG series described in the present manual are direct current
power sources, essentially electromechanical, made up of a single-phase (art. 574) or three-phase
transformer (arts. 575, 591 and 593) and a rectifier bridge.
Referring to the electrical diagrams in par. 5, the figs. in par. 4 and fig. 3.2.1 you can see the
main blocks that make up the power sources.
In power sources arts. 574 and 575, the switch (E) (50) acts as both the main switch and
output voltage selector for the power source. Depending on its position, the supply voltage is
applied to the various intermediate sockets of the primary winding of the transformer (30), for
the purpose of altering the voltage on the secondary winding and thus at the power source output.
This adapts the output current of the power source to specific welding needs.
In power sources arts. 591 and 593 the switch (E) (51) acts as a main switch, while the output
voltage is selected via the combined action of the two switches (F)(50) and (E)(51).
The mains voltage is applied to the power transformer (30) only after the contactor (47) is
closed as controlled by the control board (42) based on the operating conditions of the power
source.
The switches (50) or (51) directly affect the service transformer (44), which powers the
control board (42), which contains all circuits that manage all of the power source functions,
included the wire feeder motor speed control.
The wire speed is adjusted manually, thus regardless of the position of switches (50) and (51),
and may be adjusted from 0 to approximately 20 m/min. using knob (D).
The motor speed is adjusted by the electronic regulator present on the control board (42),
which is powered with the same supply voltage as the control board (42), supplied by the service
transformer (44).
On power source control panel is the knob (A) for adjusting welding spot time. With this
knob rotated in maximum contrary-clockwise, a build in switch disables the timing function and
allows the welding as long as the pressure on the start button lasts.
The secondary transformer circuit (30) is connected to the rectifier bridge (24), which rectifies
the welding current.
The choke (49) inserted downstream from the rectifier bridge (24) in arts. 574 and 591 serves
to level the welding current.
The intermediate socket in art. 591 maximize the welding quality for the various materials to
be welded, and the resistor (18) improves the welding start.
The polarity selector switch (61) provided on arts. 574 and 575 makes it possible to use these
power sources with flux-cored wire.
The power source power outputs are gathered together on the front panel. A central adapter
(H) (39) is set up for the torch with a built-in power socket, two contacts for the start command,
and a pneumatic socket for gas.