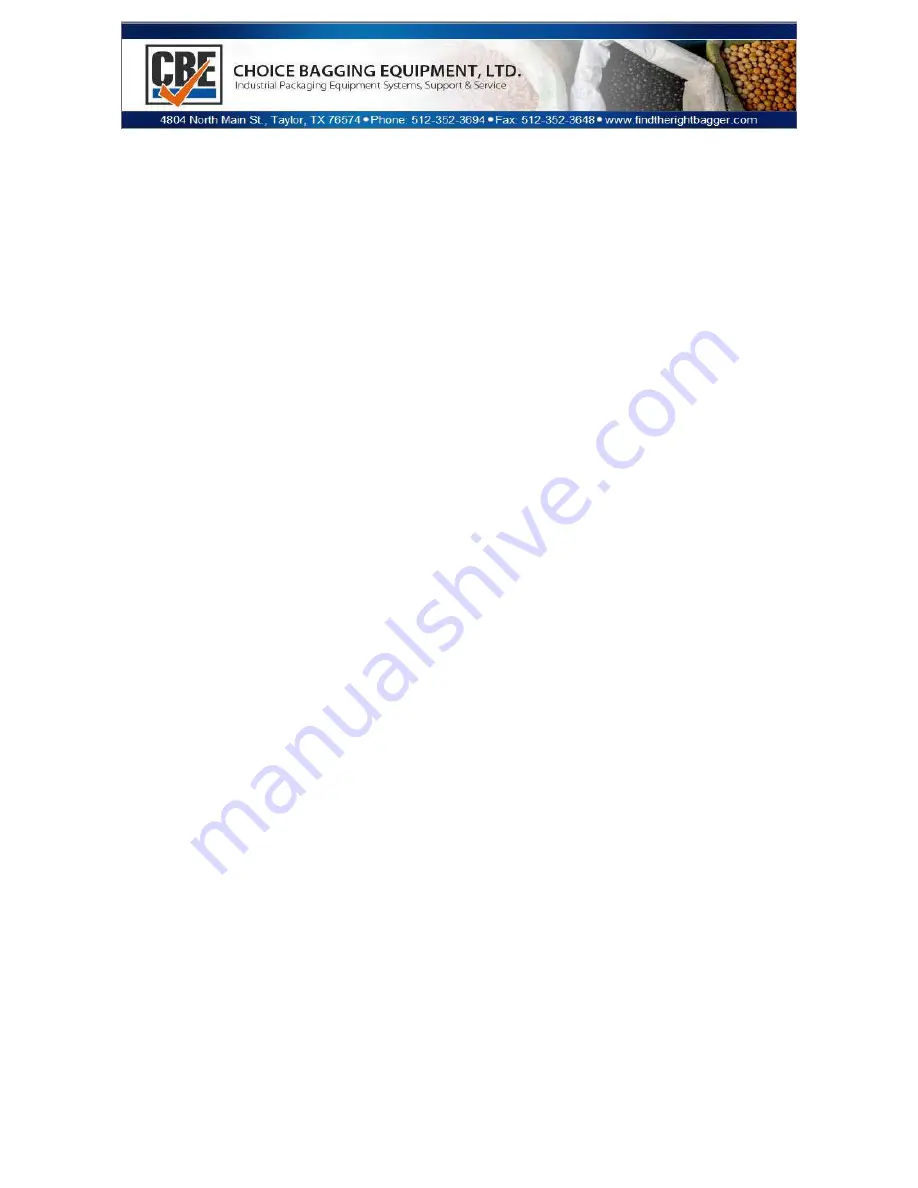
230 Series Auger Packer
1 OF 115
Customer Name
Project#: INPAK SYSTEMS/CERTIS USA
Customer PO#: 0130369-3
Serial#: 140726
Model: 230 Auger Packer/ Certis USA Project
Controller: Avery ZM405
Electrical Controls: 220/440/ other_
Electrical Motors:
Air Requirements:
Special Features: CLASS 2, Division 2, Group 2 Electrical
Summary of Contents for 230
Page 12: ...230 Series Auger Packer 12 OF 115 CHAPTER 1 RECEIPT OF EQUIPMENT ...
Page 15: ...230 Series Auger Packer 15 OF 115 CHAPTER 2 INSTALLATION ...
Page 18: ...230 Series Auger Packer 18 OF 115 CHAPTER 3 OPERATION ...
Page 21: ...230 Series Auger Packer 21 OF 115 CHAPTER 4 COMPONENT DESCRIPTION ...
Page 27: ...230 Series Auger Packer 27 OF 115 CHAPTER 5 Startup Instructions Adjustments ...
Page 34: ...230 Series Auger Packer 34 OF 115 CHAPTER 6 Non Influencing Fill Spout ...
Page 38: ...230 Series Auger Packer 38 OF 115 CHAPTER 7 PLC TIMER ADJUSTMENTS ...
Page 41: ...230 Series Auger Packer 41 OF 115 CHAPTER 8 MAINTENANCE ...
Page 47: ...230 Series Auger Packer 47 OF 115 CHAPTER 9 TROUBLESHOOTING ...
Page 53: ...230 Series Auger Packer 53 OF 115 ILLUSTRATED PARTS ...
Page 55: ...230 Series Auger Packer 55 OF 115 ...
Page 56: ...230 Series Auger Packer 56 OF 115 ...
Page 64: ...230 Series Auger Packer 64 OF 115 ...
Page 65: ...230 Series Auger Packer 65 OF 115 ...
Page 66: ...230 Series Auger Packer 66 OF 115 ...
Page 67: ...230 Series Auger Packer 67 OF 115 CHAPTER 10 WEIGH CONTROLLER ADJUSTMENTS ...
Page 75: ...230 Series Auger Packer 75 OF 115 ...
Page 76: ...230 Series Auger Packer 76 OF 115 ...
Page 77: ...230 Series Auger Packer 77 OF 115 ...
Page 78: ...230 Series Auger Packer 78 OF 115 ...
Page 79: ...230 Series Auger Packer 79 OF 115 ...
Page 80: ...230 Series Auger Packer 80 OF 115 ...
Page 81: ...230 Series Auger Packer 81 OF 115 ...
Page 82: ...230 Series Auger Packer 82 OF 115 ...
Page 83: ...230 Series Auger Packer 83 OF 115 ...
Page 84: ...230 Series Auger Packer 84 OF 115 ...
Page 85: ...230 Series Auger Packer 85 OF 115 ...
Page 86: ...230 Series Auger Packer 86 OF 115 ...
Page 87: ...230 Series Auger Packer 87 OF 115 ...
Page 88: ...230 Series Auger Packer 88 OF 115 ...
Page 89: ...230 Series Auger Packer 89 OF 115 ...
Page 90: ...230 Series Auger Packer 90 OF 115 ...
Page 91: ...230 Series Auger Packer 91 OF 115 ...
Page 92: ...230 Series Auger Packer 92 OF 115 ...
Page 93: ...230 Series Auger Packer 93 OF 115 ...
Page 94: ...230 Series Auger Packer 94 OF 115 ...
Page 95: ...230 Series Auger Packer 95 OF 115 ...
Page 96: ...230 Series Auger Packer 96 OF 115 ...
Page 97: ...230 Series Auger Packer 97 OF 115 ...
Page 98: ...230 Series Auger Packer 98 OF 115 ...
Page 99: ...230 Series Auger Packer 99 OF 115 ...
Page 100: ...230 Series Auger Packer 100 OF 115 ...
Page 101: ...230 Series Auger Packer 101 OF 115 ...
Page 102: ...230 Series Auger Packer 102 OF 115 ...
Page 103: ...230 Series Auger Packer 103 OF 115 ...
Page 104: ...230 Series Auger Packer 104 OF 115 ...
Page 105: ...230 Series Auger Packer 105 OF 115 ...
Page 106: ...230 Series Auger Packer 106 OF 115 ...
Page 107: ...230 Series Auger Packer 107 OF 115 ...
Page 108: ...230 Series Auger Packer 108 OF 115 ...
Page 109: ...230 Series Auger Packer 109 OF 115 SCHEMATICS DRAWINGS ...
Page 110: ...230 Series Auger Packer 110 OF 115 ...
Page 111: ...230 Series Auger Packer 111 OF 115 ...
Page 112: ...230 Series Auger Packer 112 OF 115 GENERAL ARRANGEMENT DRAWING ...
Page 113: ...230 Series Auger Packer 113 OF 115 ...