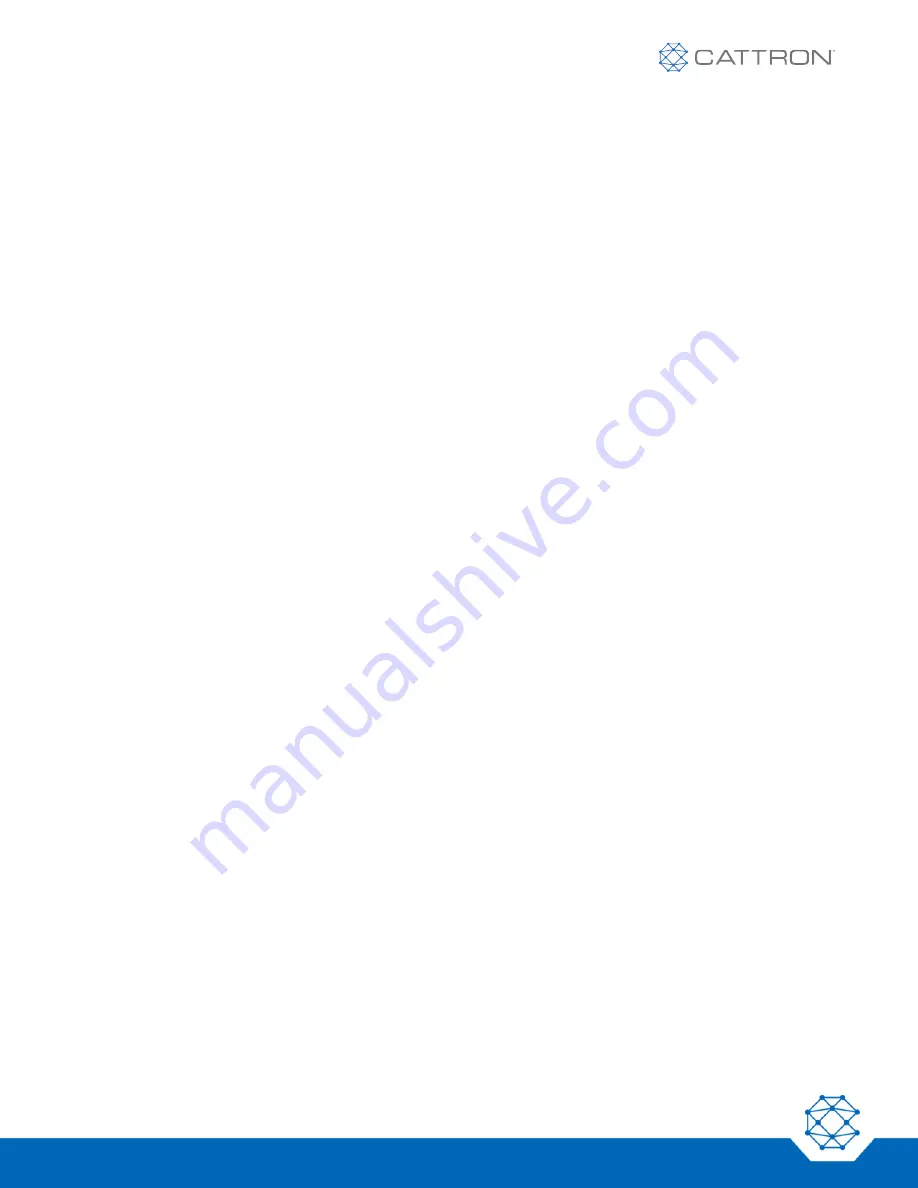
CT24 MCU
User Manual
49
9M02-7608-A001-EN
Version 2.0
CS is possible with only a single antenna, but where a crane passes over large machinery, it may be necessary to
have two antennas, so that at least one antenna has direct sight of a convenient and potentially safer operating
area; otherwise, it might not be possible to gain control of the crane.
7.4.3.2 Range Limit
Range Limit (RL) imposes some restrictions on the maximum distance that an operator may be from a machine
before operation is stopped. This distance has to be a reliable operating zone where the RL will not interrupt
normal use.
A typical RL reliable range would be about 15 m (50 ft). This by implication means that intermittent operation may
be possible at 30 m (100 ft). If the pre-set RSS is exceeded for a preset time, the operation will be brought to a
stop and the operator would have to move into a reliable RL region to regain control, or, if CS is enabled, would
have to reinitiate a CS before operation could resume. RL does not work well on cranes over 10 m (32 ft) in
height. RL also requires antenna diversity; two antennas are needed due to the need for increased precision.
7.4.4 Notes on the Differences between IR and RF Close Start
These range control features, and in particular Close Start, are possible using RF as described here or Infra-Red.
There are some notable differences between RF and IR and hence the RF and IR Range Control features differ in
the following ways:
•
IR requires the addition of one or more IR transmitters and receivers on the machine and the OCU; RF
uses the radios already being used for the data transmission so it is inherently simpler and may cost less.
•
RF is not directional, but IR is very directional and requires the OCU to be well aligned with a clear line of
sight before a CS is possible, while RF only requires a general alignment.
•
IR has a relatively short range, which is good for Close Start and Zone Control; RF has a relatively long
range making Close Start and Range Limit possible.
•
IR may be blocked by some light sources such as welding; RF will not.
7.5
Delayed Shutoff (LRC OCUs only)
The Delayed Shutoff function is an optional feature.
Delayed Shutoff enables a controlled OCU shutdown mode that allows a user to switch from remote operating
mode to a local operating mode, without the machine going into a shutdown.
For example, this allows a diesel engine driven hydraulic machine to continue to run for this short transfer period
rather than the operator going through a machine/engine start sequence to get it back into manual mode. This is
typically required when the OCU is left in a storage location remote from the vehicle cab; one example may be
underground mining machines.
In this mode, an OCU remains active for a predefined time delay between 30 seconds and 5 minutes after the
ON/OFF switch turns off. During this “DSO period”, all OCU controls are disabled except for the STOP and TILT
functions.
The OCU turns off when one of the following events is true:
•
The DSO period expires
•
The STOP button is pressed
•
A TILT event occurs (if configured)