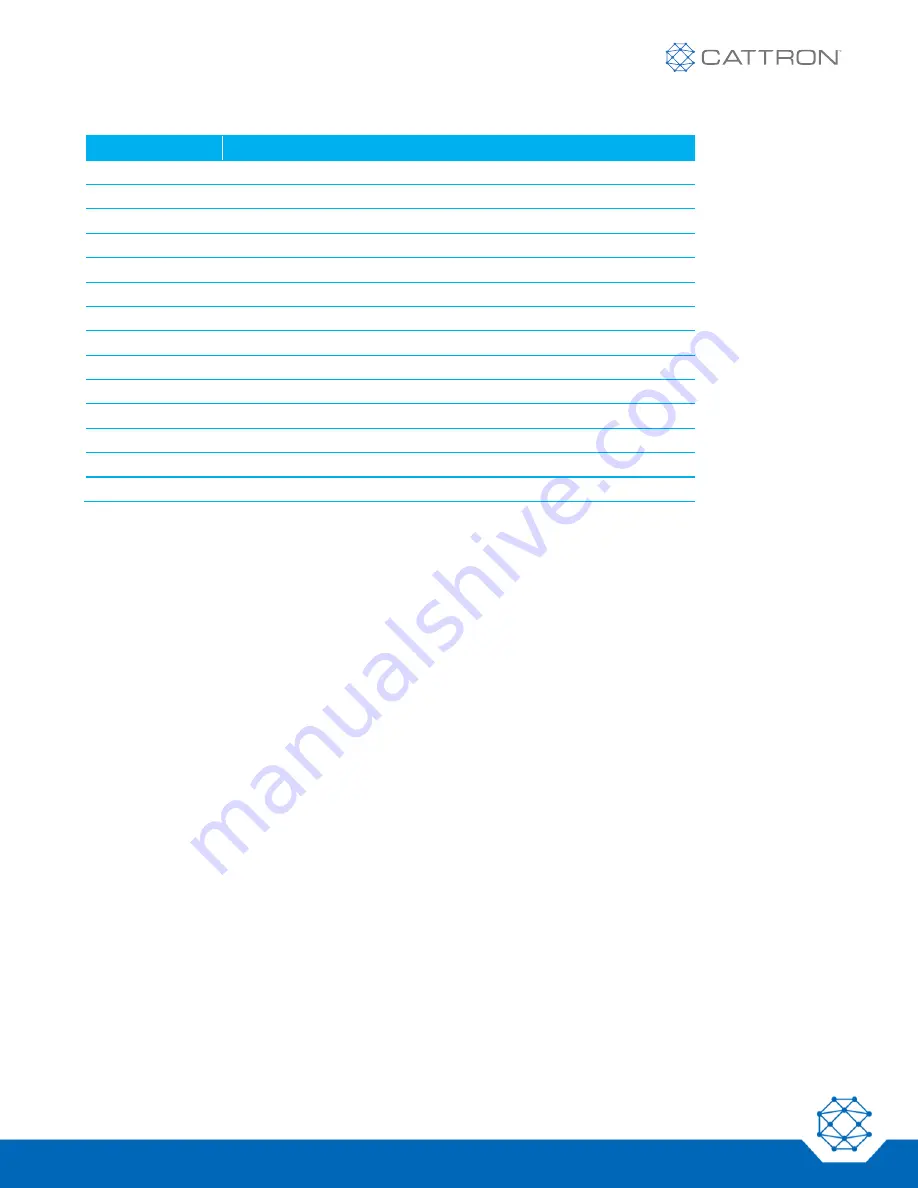
CANplus
TM
CP640 - EN
Control Panel Operation Manual
31
9M02-1000-A001-EN
Revision B
FMI
Description
8
Abnormal frequency, pulse width or period
9
Abnormal update rate
10
Abnormal rate of change
11
Failure mode not identifiable
12
Bad intelligent device or component
13
Out of calibration
14
Special instructions
15
Data valid but above normal operational range (least severe)
16
Data valid but above normal operational range (moderately severe)
17
Data valid but below normal operational range (least severe)
18
Data valid but below normal operational range (moderately severe)
19
Received network data in error
20 through 30
Reserved for future assignment
31
Not available or condition exists