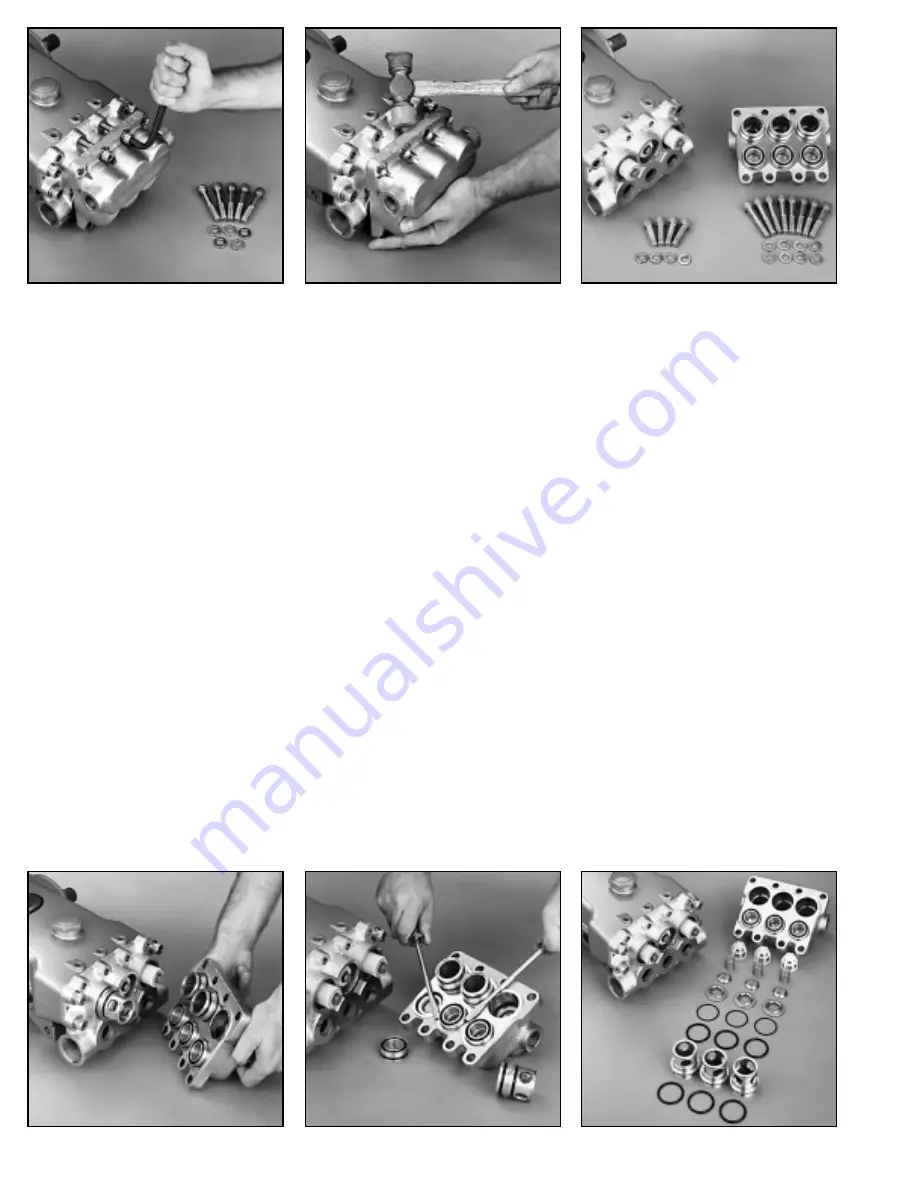
SERVICING THE VALVES
Disassembly
1. To service the Valves, the Discharge Manifold must be re-
moved. Using a M10 allen wrench remove the eight
Socket Head Screws.
2. Support the underside of the Discharge Manifold and
lightly tap the top back of the manifold with a soft mallet.
Two screwdrivers may be needed to further separate the
Discharge Manifold from the Inlet Manifold.
3. Remove the Discharge Manifold and place it crankcase
side up.
NOTE: The Discharge Valve Assembly is secured in
the upper chambers by the Discharge Valve Spacer,
while the Inlet Valve Assembly is secured in the lower
chambers by the Inlet Valve Adapter.
4. The Discharge Valve Spacers will remain in either the
Inlet Manifold or the Discharge Manifold. To remove the
Spacer from the manifold, insert two screwdrivers on
opposite sides under the machined lip on the outside of
the Spacer and pry out.
5. Use a reverse pliers to remove the Inlet Valve Adapters
from the Discharge Manifold or insert two screwdrivers
into the secondary groove on opposite sides of the
adapter and pry from valve chamber.
6. Both the Inlet and Discharge use the same Valve
Assembly. With a flat head screwdriver, carefully pry
the Seat, O-Ring, Valve, Spring and Retainer from the
manifold chamber.
CAUTION: Exercise caution to avoid scoring the
manifold chamber wall.
NOTE: This Valve Assembly does not snap together.
Reassembly
NOTE: For certain applications apply liquid gasket to
the O-Ring crevices and seal surfaces. See Tech
Bulletin 053 for model identification.
NOTE: EPDM elastomers require a silicone-base
lubricant.
1. Inspect the Spring Retainer for any scale buildup or wear
and replace as needed. Place the Spring Retainer into the
valve chamber.
Removal of Discharge Socket Head Screws
Separation of Discharge Manifold from Inlet Manifold
Discharge Manifold with both Inlet Valve Adapters and
Discharge Valve Spacers.
Removal of Discharge Valve Spacers
Removal of Inlet Valve Adapters
Discharge Valve Assembly
CAUTION: Before commencing with service, shut off drive (electric motor, gas or diesel engine) and turn off water supply to
pump. Relieve all discharge line pressure by triggering gun or opening valve in discharge line.
After servicing is completed, turn on water supply to pump, start drive, reset pressure regulating device and secondary valve, read
system pressure on the gauge at the pump head. Check for any leaks, vibration or pressure fluctuations and resume operation.