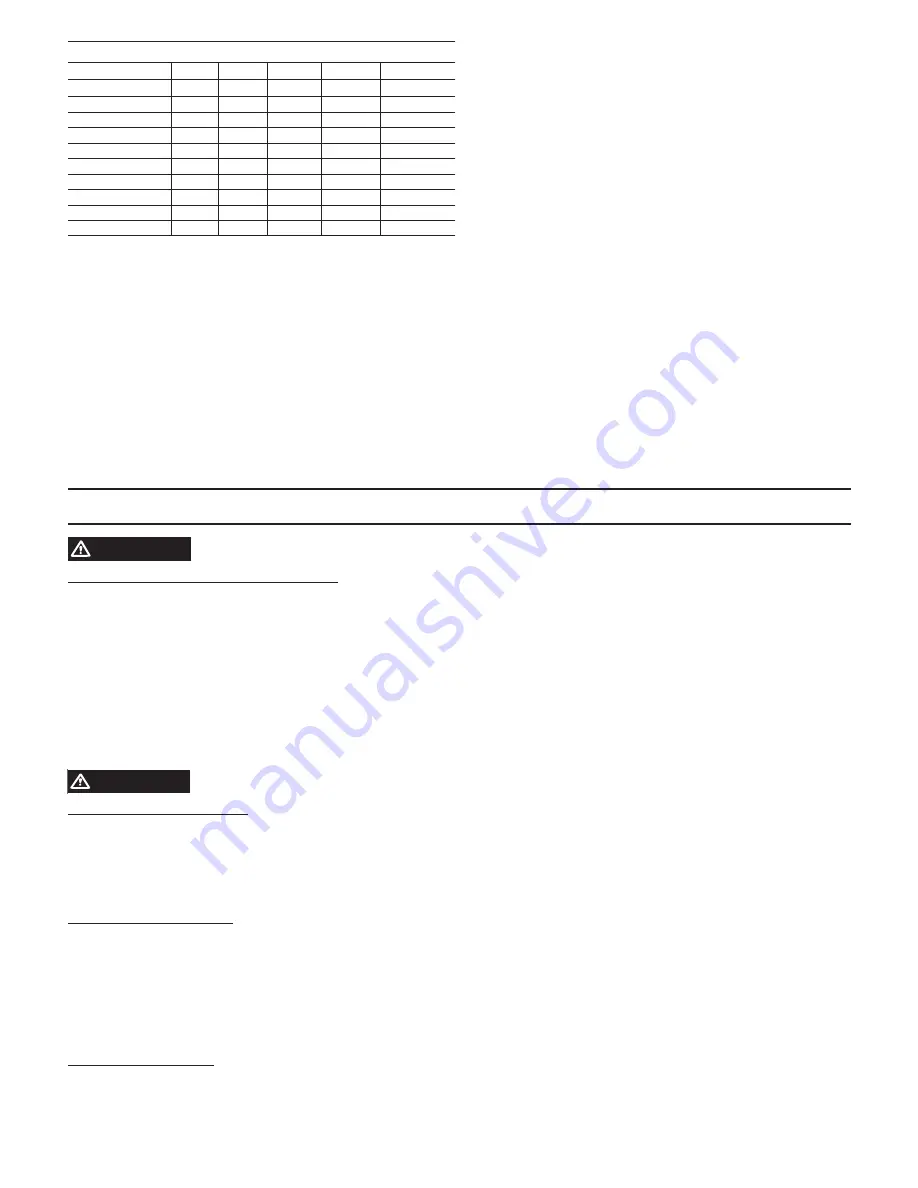
5
DANGER
A. FLAMMABLE OR EXPLOSIVE LIQUID HAZARD
Do not operate pump with flammable or explosive liquids unless extra ordinary safety precautions are observed. Leaks of flammable or
explosive liquids, if exposed to elevated temperatures, static electricity, sparks or other hazards, will result in flame or possible explosion,
causing serious personal injury, death or property damage.
1. Before operating pump with flammable or explosive liquids, ensure proper maintenance has been performed.
2. Do not operate pump with flammable or explosive liquids if leaks are detected.
3. Only pump flammable or explosive liquids that are compatible with pump component materials.
4. Do not operate pump with flammable or explosive liquids without safe guardsor safety systems to detect leaks, elevated temperatures, spark
prevention or any other hazards defined by the NFPA systems.
5. Do not remove Flammable Liquids Product Suitability Hang Tag to assure proper safety.
6. Follow ATEX guidelines for potentially explosive atmospheres.
WARNING
A. ELECTRICAL SHOCK HAZARD
Do not service pump or electrical equipment while energized. Electricity can cause personal injury, death or property damage.
1. Adhere to “Lock Out” and “Tag Out” procedures for electrical equipment.
2. Before commencing pump service, turn power supply off.
3. Keep water away from electrical outlets and electrical devices.
4. Electrical components must be installed by a qualified electrician toavoid risk of electrocution.
B. ROTATING PARTS HAZARD
Do not service pump while energized. Moving, rotating or reciprocating parts can crush and cut, causing personal injury, death or property
damage.
1. Adhere to “Lock Out” and “Tag Out” procedures for electrical equipment.
2. Before commencing pump service, turn power supply off, turn water supply off, squeeze trigger on gun to relieve system pressure.
3. For mobile equipment, be sure engines and hydraulics are turned offand secured to avoid accidental start.
4. Do not operate with safety guards removed.
5. Always use safety guards on all belt drives, couplings and shafts.
C. HOT SURFACE HAZARD
Do not touch pump, accessories or drive system while operating and until cool down is complete. Touching hot surface areas of the pump,
accessories or drive system can cause severe burns or personal injury.
PREVENATIVE MAINTENANCE CHECK-LIST
Check
Daily
Weekly
50 hrs.
500 hrs. * 1,000 hrs. **
Clean Filters
X
Oil Level/Quaility
X
Oil Leaks
X
Water Leaks
X
Plumbing
X
Initial Oil Change
X
Oil Change
X
Seal Change
X
Valve Change
X
Accessories
X
* If other than Cat Pumps special custom blend, ISO 68 hydraulic oil is used,
change cycle should be every 300 hours.
** Each system’s maintenance cycle will be exclusive. If system performance
decreases, check immediately. If no wear at 1000 hours, check again at
1500 hours and each 500 hours until wear is observed. Valves typically
require changing every other seal change.
Duty cycle, temperature, quality of pumped liquid and inlet feed
conditions all effect the life of pump wear parts and service cycle.
** Remember to service the regulator at each seal servicing and check all
system accessories and connections before resuming operation.
GENERAL SAFTEY INFORMATION AND SYMBOLS