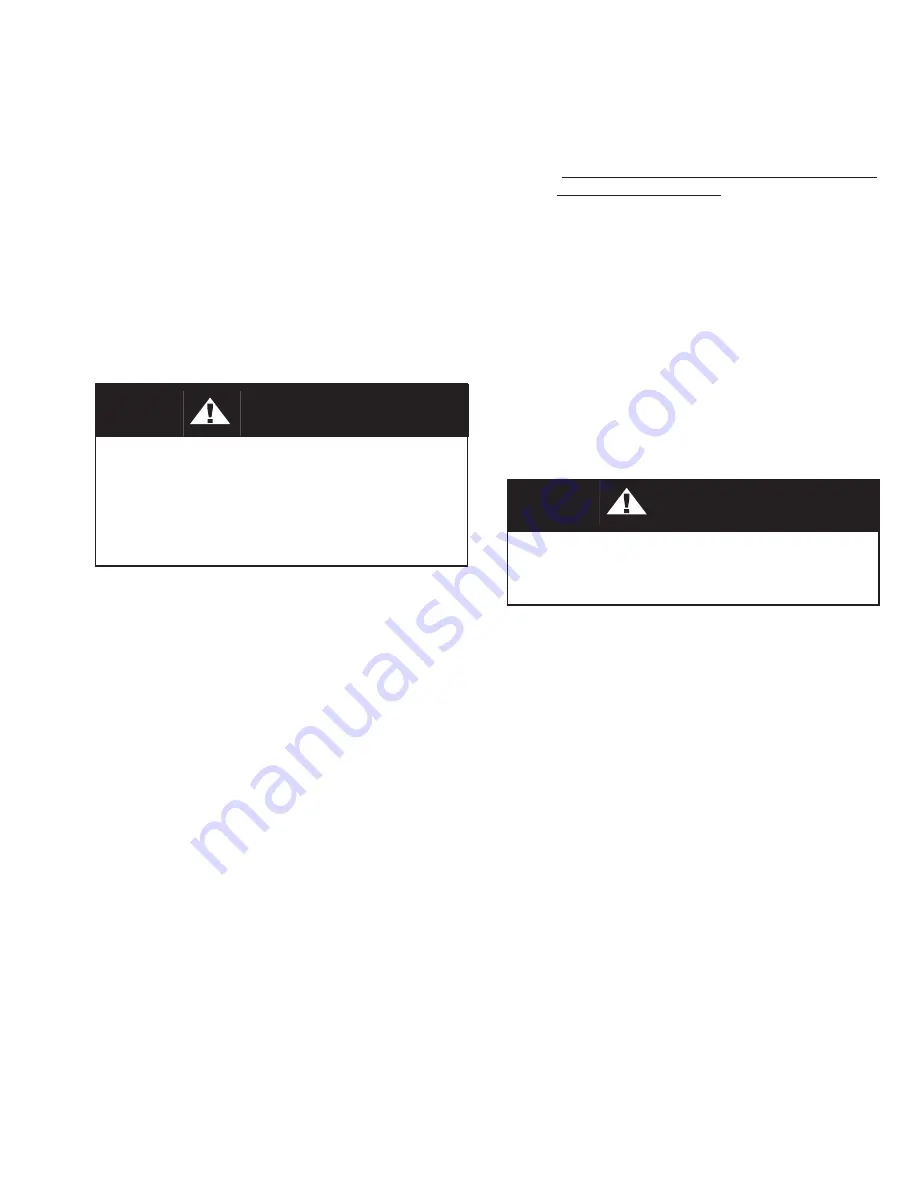
IOM-764P / PD
5
Do not rotate the needle valve (3) CW be yond this
location as the unit will be ren dered in op er a tive.
Rotate needle valve (3) CCW approximately 1/8 of
a rev o lu tion in cre ments at each adjustment. 1-1/2
rev o lu tions are the max i mum ro ta tion avail able
from the 3 per cent min i mum PB position to the
20% max i mum PB position.
SECTION IV
IV. STARTUP
1. Prior to pressurizing through the airset, dis con nect
the instrument air supply (IAS) at the airset inlet,
open the IAS block valve and blow the piping clear
of any debris. Reconnect the piping and open the
isolation valve. Set the airset to 18 psig (1.2 Barg).
2. The unit is shipped with the proportional band
(PB) set at a minimum value of approximately 3
percent. Matchmarks are factory placed on the
housing (1) and the PB needle valve (3) head
approximately perpendicular to the screw driv er
slot of the needle valve (3) head.
4. Start the process, observing the output gauge of
the controller and the process pressure gauge.
(For 764PD's, always pressure the HIGH pres sure
before the LOW pressure.) As sure that the out put
is chang ing (de creas ing from 18 psig (1.2 Barg)
if reverse acting, or in creas ing from 0 psig (0.0
Barg) is direct acting) as the controller ap proach es
setpoint. Con firm prop er action of con trol valve.
Vary the process flow and observe the reaction
of the controller to the dis tur banc es.
5. If the controller seems to be “hunting” with
over shoot and undershoot of setpoint, ad di tion al
PB should be add ed. Rotate the nee dle valve
(3) CCW in increments of 1/8 rev o lu tion. NOTE:
When PB is adjusted, setpoint will nor mal ly re quire
slight resetting; rotate the adjusting screw (2.3) as
re quired. Repeat until best stability is ob tained, or
up to the maximum of 1-1/2 rev o lu tions.
3. Units are factory calibrated to ap prox i mate ly mid-
range; i.e. 50-150 psig (3.4-10.3 Barg) range will
have setpoint at approximately 100 psig (6.9 Barg).
It is rec om mend ed that the unit be field calibrated
following in stal la tion and prior to startup. (See
Sec tion VI. CAL I BRA TION for de tailed pro ce dure.)
Direct Action:
Adjust setpoint by rotating
ad just ing screw CCW to de crease setpoint or turn
CW to increase setpoint.
Reverse Action:
Adjust setpoint by rotating
ad just ing screw CW to de crease setpoint or turn
CCW to increase setpoint.
Always make ad just ments in small in cre ments and
wait un til reactions can be ob served be fore making
fur ther ad just ments.
6. If “hunting” persists after com ple tion of Step 5, the
controller can be slowed down by reducing airset
supply pres sure down to 16 psig (1.1 Barg) in 1 psi
(0.07 Bar) increments. If this procedure is used,
repeat Step 5.
7. If “hunting” persists after completion of Step 6,
rotate the needle valve on the sensing line “to wards
closed” to provide “snub bing” action. DO NOT
FULLY CLOSE SENSING NEEDLE VALVE.
SECTION V
V. MAINTENANCE
A. General:
1. Refer to Figure 12 for basic pressure con trol ler.
Refer to Figure 13 for differential pressure
controller.
2. Maintenance pro
ce dures hereinafter are
based on removal from the process piping
system where in stalled. When removing the
tubing, put a tag on the tubing which port, “A”
or “B”, was utilized.
3. If complete overhaul is undertaken, it is
rec om mend ed that the pneumatic circuit
over haul be completed prior to diaphragm
re place ment.
4. Lightly grease all sensor sub-assembly (2)
O-rings (5) (6) upon re place ment with lith i um
grease; cloth wipe all excess grease.
B. Diaphragm Replacement:
1. If diaphragm (12) has cracked and leaked,
com plete unit must be overhauled including
the pneumatic circuit portion.
CAUTION
CAUTION