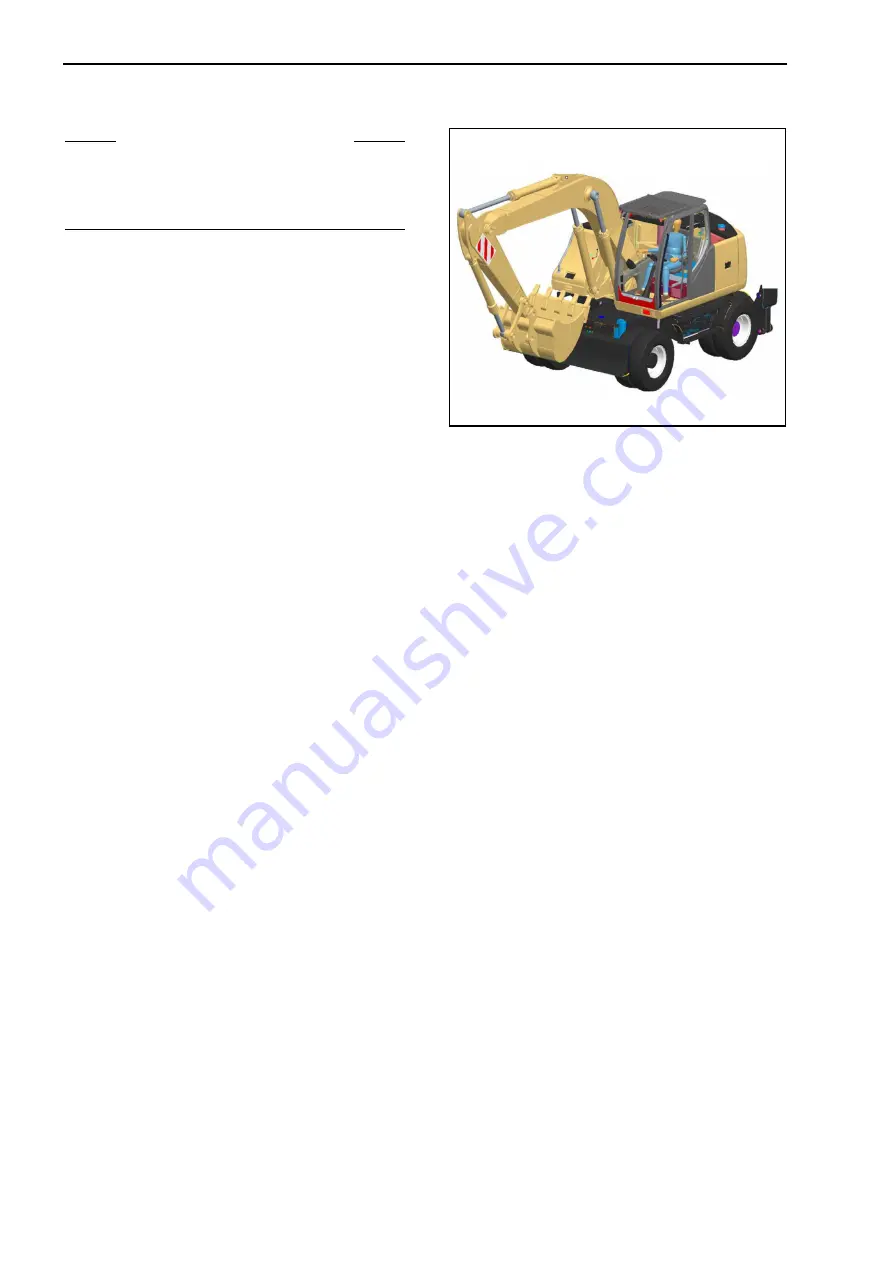
SECTION 1
1-6
OPERATOR PROTECTIVE STRUCTURE
The Protective Structure is a special safety compo-
nent of your machine.
DO NOT attach any device to the Protective Struc-
ture for pulling purposes. DO NOT drill holes to the
Protective Structure.
The Protective Structure and interconnecting com-
ponents are a certified system. Any damage, fire,
corrosion or modification will weaken the structure
and reduce your protection. If this occurs, the Pro-
tective Structure MUST be replaced so that it will
provide the same protection as a new Protective
Structure. Contact your dealer for Protective Struc-
ture inspection and replacement.
After an accident or fire that involve the cab and/or
machine tip or roll over, the following MUST be per-
formed by a qualified technician before returning the
machine to field or job site operation:
- the Protective Structure MUST be checked and
replaced if necessary;
- the mounting for the Protective Structure, operator
seat and seat belt, MUST be carefully inspected
for damages and replaced if necessary;
- all damaged parts MUST be replaced.
NOTE:
do not weld, drill holes, attempt to straighten
or repair the protective structure. Modification in any
way can reduce the structural integrity of the struc-
ture which could cause death or serious injury in the
event of fire, tip, rollover, collision or accident.
S
WARNING
S
Your machine is equipped with an operator Protec-
tive Structure, such as: a Rollover Protective Struc-
ture (ROPS) and Falling Object Protective Structure
(FOPS).
3