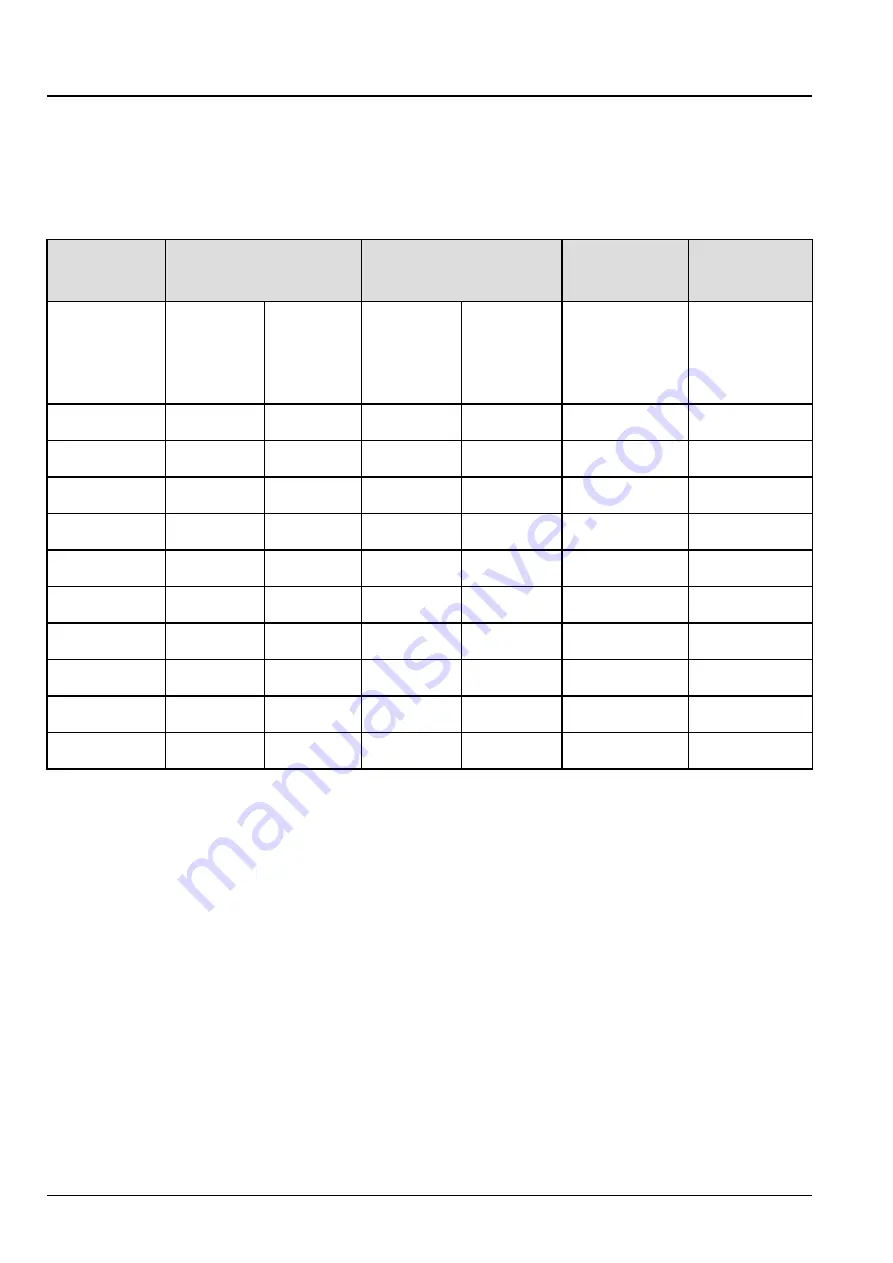
INTRODUCTION
1. Manufacturer's Identification
2. Property Class
3. Clock Marking of Property Class and Manufacturer's Identification (Optional), i.e. marks
60°
apart indicate Class
10 properties, and marks
120°
apart indicate Class 8.
INCH NON-FLANGED HARDWARE
NOMINAL
SIZE
SAE GRADE 5 BOLT
and NUT
SAE GRADE 8 BOLT
and NUT
LOCKNUT
GrB W/ Gr5
BOLT
LOCKNUT
GrC W/ Gr8
BOLT
UN-
PLATED
or
PLATED
SILVER
PLATED
W/ZnCr
GOLD
UN-
PLATED
or PLATED
SILVER
PLATED
W/ZnCr
GOLD
1/4
8 N·m
(
71 lb
in
)
11 N·m
(
97 lb
in
)
12 N·m
(
106 lb in
)
16 N·m
(
142 lb in
)
8.5 N·m
(
75 lb in
)
12.2 N·m
(
109 lb
in
)
5/16
17 N·m
(
150 lb in
)
23 N·m
(
204 lb in
)
24 N·m
(
212 lb in
)
32 N·m
(
283 lb in
)
17.5 N·m
(
155 lb
in
)
25 N·m
(
220 lb
in
)
3/8
30 N·m
(
22 lb
ft
)
40 N·m
(
30 lb ft
)
43 N·m
(
31 lb
ft
)
57 N·m
(
42 lb
ft
)
31 N·m
(
23 lb ft
)
44 N·m
(
33 lb ft
)
7/16
48 N·m
(
36 lb
ft
)
65 N·m
(
48 lb ft
)
68 N·m
(
50 lb
ft
)
91 N·m
(
67 lb
ft
)
50 N·m
(
37 lb ft
)
71 N·m
(
53 lb ft
)
1/2
74 N·m
(
54 lb
ft
)
98 N·m
(
73 lb ft
)
104 N·m
(
77 lb ft
)
139 N·m
(
103 lb ft
)
76 N·m
(
56 lb ft
)
108 N·m
(
80 lb
ft
)
9/16
107 N·m
(
79 lb ft
)
142 N·m
(
105 lb ft
)
150 N·m
(
111 lb ft
)
201 N·m
(
148 lb ft
)
111 N·m
(
82 lb ft
)
156 N·m
(
115 lb
ft
)
5/8
147 N·m
(
108 lb ft
)
196 N·m
(
145 lb ft
)
208 N·m
(
153 lb ft
)
277 N·m
(
204 lb ft
)
153 N·m
(
113 lb
ft
)
215 N·m
(
159 lb
ft
)
3/4
261 N·m
(
193 lb ft
)
348 N·m
(
257 lb ft
)
369 N·m
(
272 lb ft
)
491 N·m
(
362 lb ft
)
271 N·m
(
200 lb
ft
)
383 N·m
(
282 lb
ft
)
7/8
420 N·m
(
310 lb ft
)
561 N·m
(
413 lb ft
)
594 N·m
(
438 lb ft
)
791 N·m
(
584 lb ft
)
437 N·m
(
323 lb
ft
)
617 N·m
(
455 lb
ft
)
1
630 N·m
(
465 lb ft
)
841 N·m
(
620 lb ft
)
890 N·m
(
656 lb ft
)
1187 N·m
(
875 lb ft
)
654 N·m
(
483 lb
ft
)
924 N·m
(
681 lb
ft
)
NOTE:
For Imperial Units,
1/4 in
and
5/16 in
hardware torque specifications are shown in pound-inches.
3/8 in
through
1 in
hardware torque specifications are shown in pound-feet.
48194558 20/10/2017
44