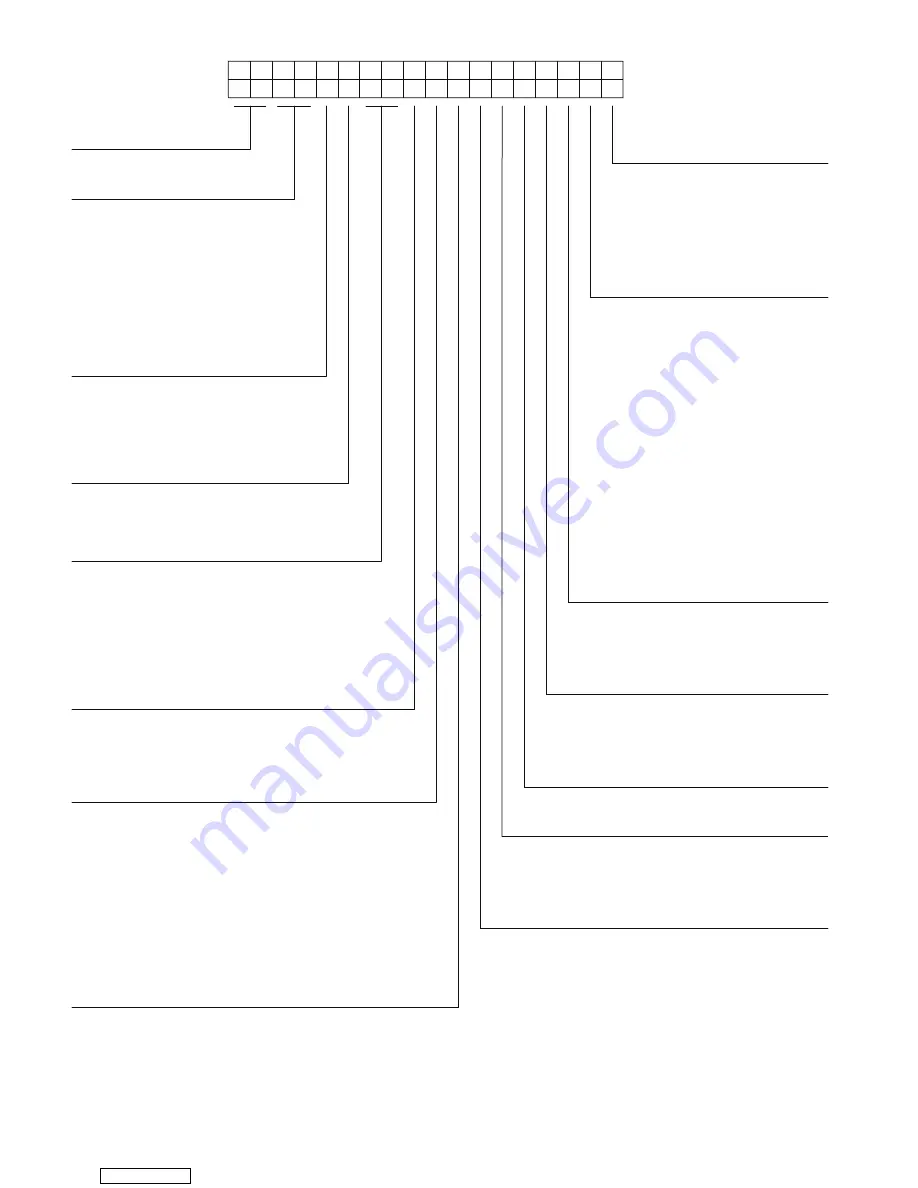
4
Fig. 1 — 48HC 04-06 Model Number Nomenclature (Example)
4
8
H
C
E
A
0
4
A
2
A
6
A
0
A
3
B
0
Cooling Tons
04 - 3 ton
05 - 4 ton
06 - 5 ton
1
Example:
Position:
2
3
4
5
6
7
8
9
10 11 12 13 14 15 16 17 18
Heat Options
D = Low Gas Heat
E = Medium Gas Heat
F = High Gas Heat
L = Low NOx — Low Gas Heat
M = Low NOx — Medium Gas Heat
N = Low NOx — High Gas Heat
S = Low Heat w/ Stainless Steel Exchanger
R = Medium Heat w/ Stainless Steel Exchanger
T = High Heat w/ Stainless Steel Exchanger
(Low NOx models include — Stainless Steel HX)
Sensor Options
A = None
B = RA Smoke Detector
C = SA Smoke Detector
D = RA + SA Smoke Detector
E = CO
2
F = RA Smoke Detector and CO
2
G = SA Smoke Detector and CO
2
H = RA + SA Smoke Detector and CO
2
Indoor Fan Options
0 = Electric (Direct) Drive x13 Motor (non Humidi-MiZer
®
models only)
1 = Standard Static Option - Belt Drive (Humidi-MiZer
®
models only)
2 = Medium Static Option - Belt Drive
3 = High Static Option - Belt Drive
Coil Options (RTPF) (Outdoor - Indoor - Hail Guard)
A = Al/Cu - Al/Cu
B = Precoat Al/Cu - Al/Cu
C = E-coat Al/Cu - Al/Cu
D = E-coat Al/Cu - E-coat Al/Cu
E = Cu/Cu - Al/Cu
F = Cu/Cu - Cu/Cu
M = Al/Cu -Al/Cu — Louvered Hail Guard
N = Precoat Al/Cu - Al/Cu — Louvered Hail Guard
P = E-coat Al/Cu - Al/Cu — Louvered Hail Guard
Q = E-coat Al/Cu - E-coat Al/Cu — Louvered Hail Guard
R = Cu/Cu - Al/Cu — Louvered Hail Guard
S = Cu/Cu - Cu/Cu — Louvered Hail Guard
Voltage
1 = 575/3/60
3 = 208-230/1/60
5 = 208-230/3/60
6 = 460/3/60
Design Revision
A = Factory Design Revision
Base Unit Controls
0 = Base Electromechanical Controls
1 = PremierLink
TM
Controller
2 = RTU Open Multi-Protocol Controller
D = ComfortLink Controls
Intake / Exhaust Options
A = None
B = Temperature Economizer w/ Barometric Relief
F = Enthalpy Economizer w/ Barometric Relief
K = 2-Position Damper
Service Options
0 = None
1 = Unpowered Convenience Outlet
2 = Powered Convenience Outlet
3 = Hinged Access Panels
4 = Hinged Access Panels and
Unpowered Convenience Outlet
5 = Hinged Panels and
Powered Convenience Outlet
C = Foil Faced Insulation
D = Foil Faced Insulation and
Unpowered Convenience Outlet
E = Foil Faced Insulation and
Powered Convenience Outlet
F = Foil Faced Insulation and
Hinged Access Panels
G = Foil Faced Insulation, Hinged Access Panels
and Unpowered Convenience Outlet
H = Foil Faced Insulation, Hinged Access Panels
and Powered Convenience Outlet
Factory Assigned
0 = Standard
1 = LTL
Electrical Options
A = None
B = HACR Breaker
C = Non-Fused Disconnect
D = Thru-The-Base Connections
E = HACR and Thru-The-Base Connections
F = Non-Fused Disconnect and
Thru-The-Base
Connections
Refrig. Systems Options
A = Single stage cooling models
B = Single stage cooling models
with
Humidi-MiZer
®
System
F = Single stage cooling models with
MotorMaster
®
Low Ambient Controller
Note: On single phase (-3 voltage code) models, the
following are not available as a factory installed option:
-
Humidi-MiZer
®
System
- Coated Coils or Cu Fin Coils
- Louvered Hail Guards
- Economizer or 2 Position Damper
- Powered 115 Volt Convenience Outlet
Unit Heat Type
48 - Gas Heat Packaged Rooftop
Model Series - WeatherMaster
®
HC - High Efficiency
Downloaded from
Summary of Contents for WeatherMaster 48HC Series
Page 7: ...7 Fig 4 48HC 04 06 Corner Weights and Clearances Downloaded from ManualsNet com search engine ...
Page 8: ...8 Fig 5 48HC 04 06 Base Rail Details Downloaded from ManualsNet com search engine ...
Page 9: ...9 Fig 6 48HC 04 06 Thru the Base Charts Downloaded from ManualsNet com search engine ...
Page 33: ...33 Fig 56 48HC 04 06 Control Wiring Diagram Downloaded from ManualsNet com search engine ...