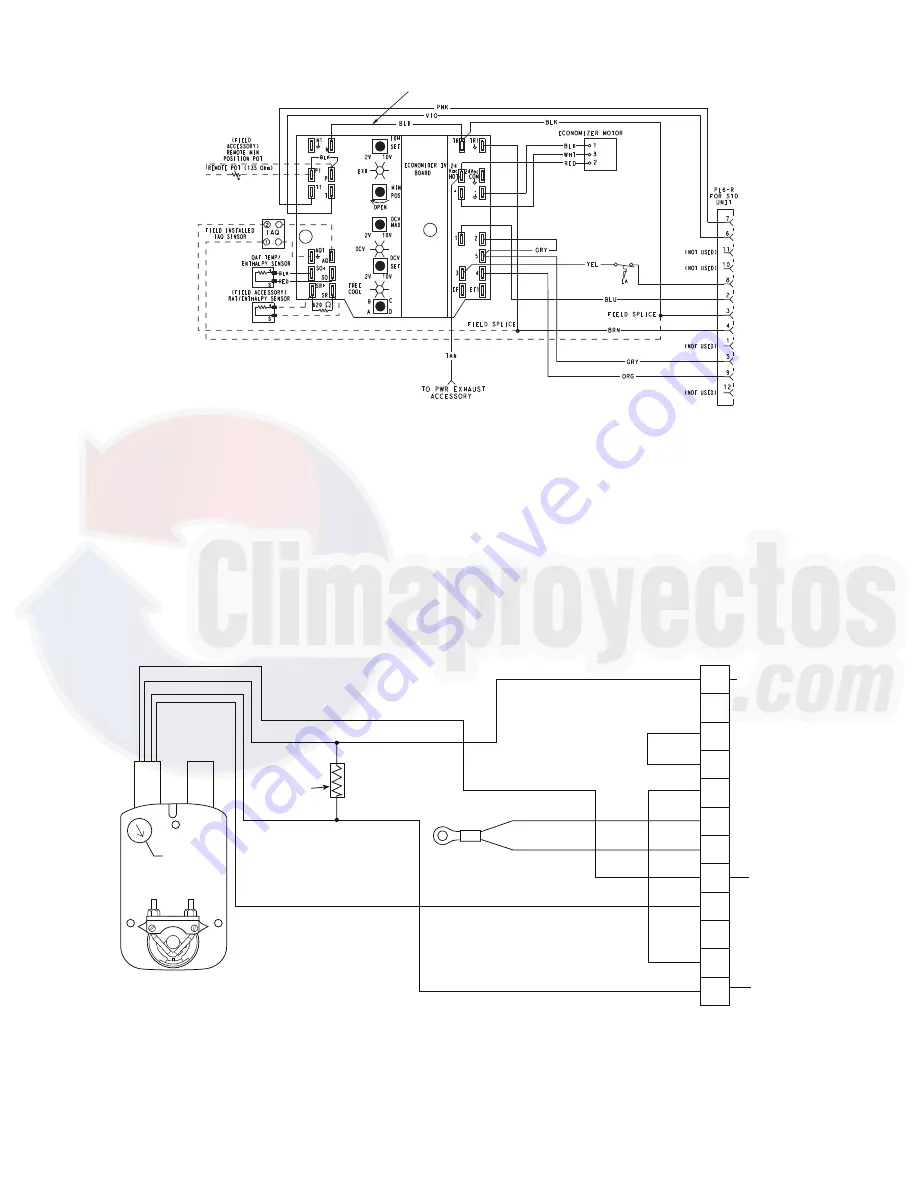
37
Potentiometer
Defaults Settings:
Power Exhaust
Middle
Minimum Pos.
Fully Closed
DCV Max.
Middle
DCV Set
Middle
Enthalpy
C Setting
NOTES:
1. 620 ohm, 1 watt 5% resistor should be removed only when using
differential enthalpy or dry bulb.
2. If a separate field-supplied 24 v transformer is used for the IAQ
sensor power supply, it cannot have the secondary of the trans-
former grounded.
3. For field-installed remote minimum position POT, remove black
wire jumper between P and P1 and set control minimum position
POT to the minimum position.
Fig. 55 —
EconoMi$er IV Wiring
NOTES:
1. Switch on actuator must be in run position for economizer to operate.
2.
PremierLink™ control requires that the standard 50HJ540569 out
-
side-air sensor be replaced by either the CROASENR001A00 dry
bulb sensor or HH57A077 enthalpy sensor.
3. 50HJ540573 actuator consists of the 50HJ540567 actuator and a
harness with 500-ohm resistor.
Fig. 56 —
EconoMi$er2 with 4 to 20 mA Control Wiring
FOR OCCUPANCY CONTROL
REPLACE JUMPER WITH
FIELD-SUPPLIED TIME CLOCK
8
7
LEGEND
DCV
— Demand Controlled Ventilation
IAQ
— Indoor Air Quality
LA
— Low Ambient Lockout Device
OAT
— Outdoor Air Temperature
POT
— Potentiometer
RAT
— Return Air Temperature
4
3
5
2
8
6
7
1
10
11
9
12
PINK
VIOLET
BLACK
BLUE
YELLOW
RUN
RED
WHITE
ECONOMI$ER2 PLUG
DIRECT DRIVE
ACTUATOR
4-20mA SIGNAL
OAT SENSOR
ACTUATOR
CONTROL
(4-20mA)
ACTUATOR
FEEDBACK
(2-10VDC)
TRANSFORMER
GROUND
ORANGE
500 OHM
RESISTOR
Summary of Contents for WeatherMaker 50TCQ 17-24 Series
Page 35: ...35 Fig 53 RTU Open Overlay for Economizer Wiring ...
Page 36: ...36 Fig 54 VFD Overlay for W2770 Controller Wiring ...
Page 68: ...68 Fig B 50TCQD17 24 Control Wiring Diagram APPENDIX D WIRING DIAGRAMS ...
Page 69: ...69 Fig C 50TCQD17 24 Power Wiring Diagram 208 230 3 60 Units APPENDIX D WIRING DIAGRAMS ...
Page 70: ...70 Fig D 50TCQD17 24 Power Wiring Diagram 460 3 60 575 3 60 Units APPENDIX D WIRING DIAGRAMS ...
Page 71: ...71 Fig E RTU Open Overlay APPENDIX D WIRING DIAGRAMS ...
Page 72: ...72 Fig F PremierLink Overlay APPENDIX D WIRING DIAGRAMS ...