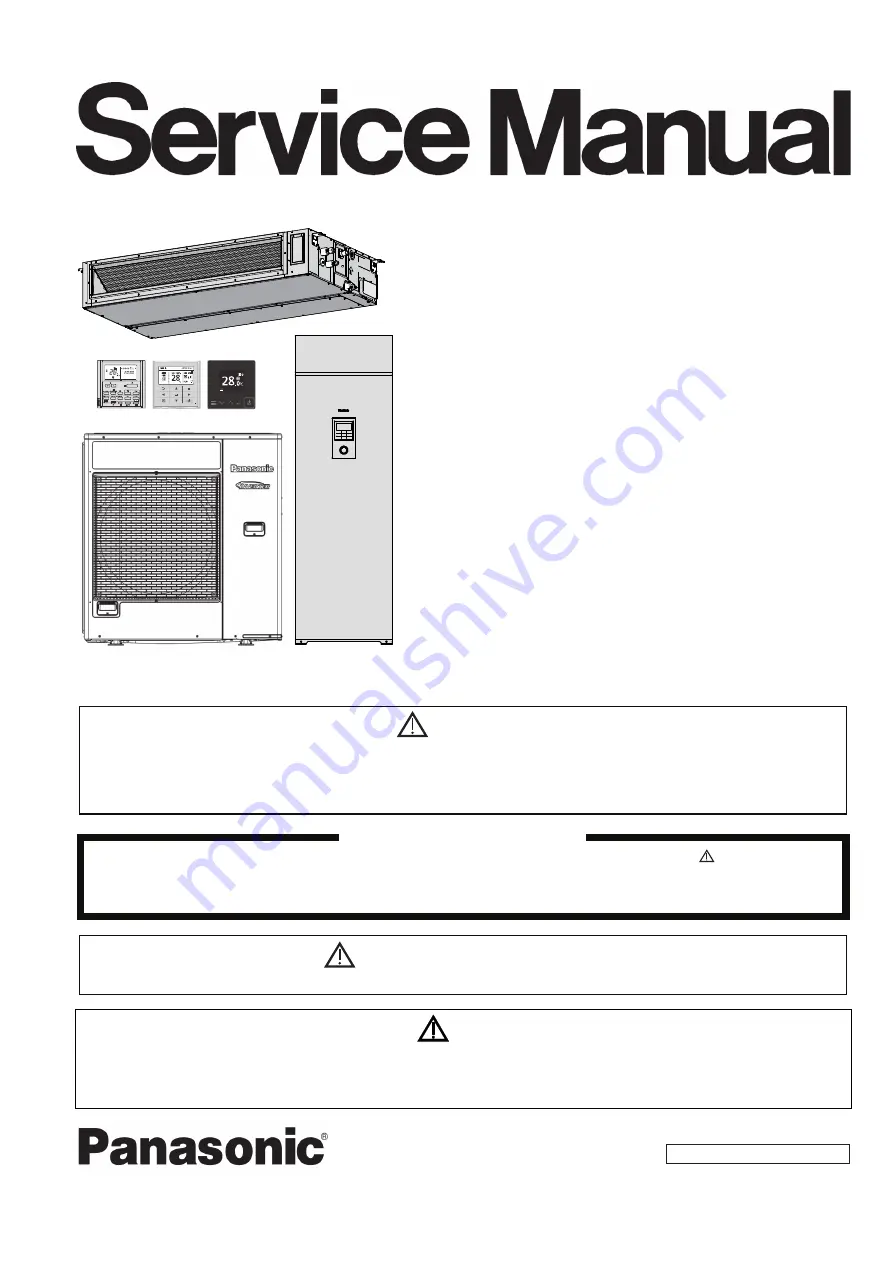
© Panasonic Corporation 2022
Order No: PAPAMY2203084CE
Air Conditioner
A
°
Indoor Unit
Outdoor Unit
WH-ADF0309J3E5CM
S-71WF3E
CU-2WZ71YBE5
Destination
Europe
WARNING
This service information is designed for experienced repair technicians only and is not designed for use by the general public.
It does not contain warnings or cautions to advise non-technical individuals of potential dangers in attempting to service a product.
Products powered by electricity should be serviced or repaired only by experienced professional technicians. Any attempt to
service or repair the products dealt with in this service information by anyone else could result in serious injury or death.
There are special components used in this equipment which are important for safety. These parts are marked by in the Schematic
Diagrams, Circuit Board Diagrams, Exploded Views and Replacement Parts List. It is essential that these critical parts should be
replaced with manufacturer’s specified parts to prevent shock, fire or other hazards. Do not modify the original design without permission
of manufacturer.
IMPORTANT SAFETY NOTICE
In order to avoid frostbite, be assured of no refrigerant leakage during the installation or repairing of refrigerant circuit.
PRECAUTION OF LOW TEMPERATURE
CAUTION
R32 REFRIGERANT
– This Air Conditioner contains and operates with refrigerant R32.
THIS PRODUCT MUST ONLY BE INSTALLED OR SERVICED BY QUALIFIED PERSONNEL.
Refer to National, State, Territory and local legislation, regulations, codes, installation & operation manuals, before the installation,
maintenance and/or service of this product.