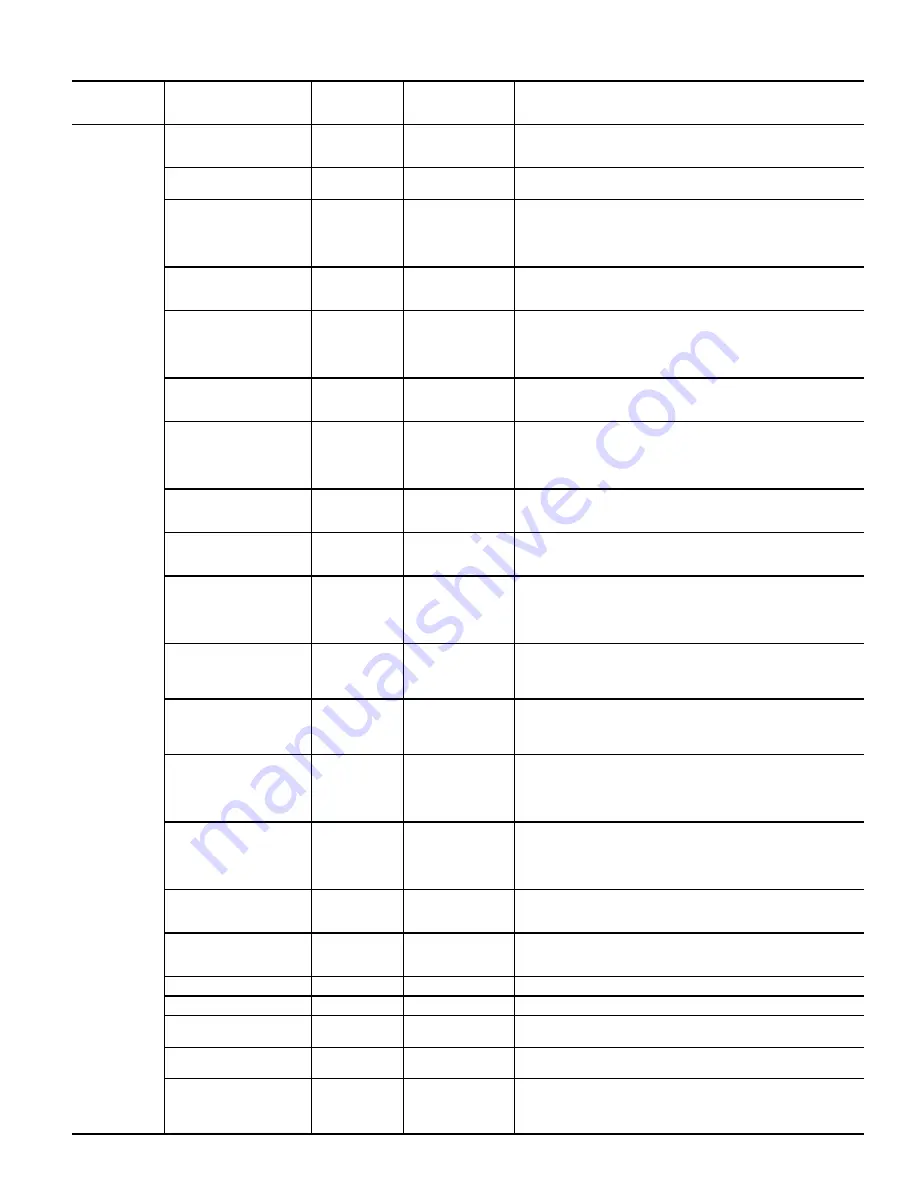
59
Table 7 — Menu Structure
MENU
PARAMETER
PARAMETER
DEFAULT
VALUE
PARAMETER
RANGE AND
INCREMENT
NOTES
STATUS
ECONO AVAIL
NO
YES/NO
FIRST STAGE COOLING DEMAND (Y1–IN)
YES = economizing available; the system can use outside air for
free cooling when required
ECONOMIZING
NO
YES/NO
FIRST STAGE COOLING RELAY OUTPUT
YES = outside air being used for 1 stage cooling
OCCUPIED
NO
YES/NO
OCCUPIED
YES = OCC signal received from space thermostat or
unitary controller
YES = 24 vac on terminal OCC
NO = 0 vac on terminal OCC
HEAT PUMP
N/A
COOL
HEAT
HEAT PUMP MODE
Displays COOL or HEAT when system is set to heat pump
(Non-conventional)
COOL Y1—IN
OFF
ON/OFF
FIRST STAGE COOLING DEMAND (Y1-IN)
Y1–I signal from space thermostat or unitary controller for
cooling stage 1.
ON = 24 vac on terminal Y1–I
OFF = 0 vac on terminal Y1–I
COOL Y1—OUT
OFF
ON/OFF
FIRST STAGE COOLING RELAY OUTPUT
Cool stage 1 Relay Output to stage 1 mechanical cooling
(Y1–OUT terminal)
COOL Y2—IN
OFF
ON/OFF
SECOND STAGE COOLING DEMAND (Y2–IN)
Y2–I signal from space thermostat or unitary controller for
second stage cooling.
ON = 24 vac on terminal Y2–I
OFF = 0 vac on terminal Y2–I
COOL Y2—OUT
OFF
ON/OFF
SECOND STAGE COOLING RELAY OUTPUT
Cool Stage 2 Relay Output to mechanical cooling
(Y2–OUT terminal)
MA TEMP
_ _ . _ F
0°F to 140°F
SUPPLY AIR TEMPERATURE, Cooling Mode
Displays value of measured mixed air from MAT sensor.
Displays _ _ . _ F if not connected, short or out-of-range.
DA TEMP
_ _ . _ F
0°F to 140°F
DISCHARGE AIR TEMPERATURE, after Heating section
Displays when Discharge Air sensor is connected and displays
measured discharge temperature.
Displays _ _ . _F if sensor sends invalid value, if not connected,
short or out-of-range.
OA TEMP
_ _ . _ F
-40°F to 140°F
OUTSIDE AIR TEMP
Displays measured value of outdoor air temperature.
Displays _ _ . _F if sensor sends invalid value, short or
out-of-range.
OA HUM
_ _ %
0 to 100%
OUTSIDE AIR RELATIVE HUMIDITY
Displays measured value of outdoor humidity from
OA sensor.
Displays _ _% if not connected short, or out-of-range.
RA TEMP
_ _ . _ F
0°F to 140°F
RETURN AIR TEMPERATURE
Displays measured value of return air temperature from
RAT sensor.
Displays _ _ . _ F if sensor sends invalid value, if not connected,
short or out-of-range
RA HUM
_ _ %
0 to 100%
RETURN AIR RELATIVE HUMIDITY
Displays measured value of return air humidity from
RA sensor.
Displays _ _% if sensor sends invalid value, if not connected,
short or out-of-range
IN CO2
_ _ _ ppm
0 TO 2000 ppm
SPACE/RETURN AIR CO
2
Displays value of measured CO
2
from CO
2
sensor. Invalid if not
connected, short or out-of-range
DCV STATUS
N/A
ON/OFF
DEMAND CONTROLLED VENTILATION STATUS
Displays ON if above setpoint and OFF if below setpoint, and
ONLY if a CO
2
sensor is connected.
DAMPER OUT
2.0v
2.0 TO 10.0v
Displays voltage output to the damper actuator.
ACT POS
N/A
0 to 100%
Displays actual position of outdoor air damper actuator
ACT COUNT
N/A
1 to 65535
Displays number of times actuator has cycled.
1 cycles equals 180 deg. of actuator movement in any direction.
ACTUATOR
N/A
OK/Alarm (on
Alarm menu)
Displays ERROR if voltage or torque is below actuator range.
EXH1 OUT
OFF
ON/OFF
EXHAUST STAGE 1 RELAY OUTPUT
Output of EXH1 terminal:
ON = relay closed
OFF = relay open
Summary of Contents for WeatherMaker 50TC07 Series
Page 4: ...4 Fig 2 Dimensional Drawing for Units Built on and After 4 15 19 Size 07 ...
Page 5: ...5 Fig 3 Dimensional Drawing for Units Built Prior to 4 15 19 Size 07 ...
Page 6: ...6 Fig 4 Corner Weights and Clearances Size 07 ...
Page 7: ...7 Fig 5 Base Rail Details Size 07 ...
Page 8: ...8 Fig 6 Thru the Base Charts Size 07 ...
Page 9: ...9 Fig 7 Unit Dimensional Drawing Size 08 09 12 ...
Page 10: ...10 Fig 7 Unit Dimensional Drawing Size 08 09 12 cont ...
Page 11: ...11 Fig 8 Unit Dimensional Drawing Size 14 ...
Page 12: ...12 Fig 8 Unit Dimensional Drawing Size 14 cont ...
Page 13: ...13 Fig 9 Unit Dimensional Drawing Size 16 Unit ...
Page 14: ...14 Fig 9 Unit Dimensional Drawing Size 16 Unit cont ...
Page 19: ...19 Fig 14 Roof Curb Details Size 16 Unit ...
Page 26: ...26 Fig 34 50TC 07 Control Wiring Diagram ...
Page 27: ...27 Fig 35 50TC 07 Power Wiring Diagram ...
Page 28: ...28 Fig 36 50TC M08 12 Control Wiring Diagram ...
Page 29: ...29 Fig 37 50TC D E Wiring Diagram 08 14 Size Units ...
Page 30: ...30 Fig 38 Single Stage Cooling without VFD Power Wiring Diagram Sizes 08 12 ...
Page 31: ...31 Fig 39 2 Stage Cooling with VFD Power Wiring Diagram Sizes 08 12 ...
Page 32: ...32 Fig 40 2 Stage Cooling with VFD Power Wiring Diagram Size 14 ...
Page 33: ...33 Fig 41 50TC 16 Wiring Diagram ...
Page 34: ...34 Fig 42 2 Stage Cooling with VFD Power Wiring Diagram Size 16 ...
Page 35: ...35 Fig 43 50TC 07 Units Wiring Diagram with Humidi MiZer System Option ...
Page 36: ...36 Fig 44 50TC 08 14 Units Wiring Diagram with Humidi MiZer System Option ...
Page 37: ...37 Fig 45 50TC 16 Wiring Diagram with Humidi MiZer System Option ...
Page 69: ...69 Fig 97 Typical PremierLink Control Wiring Diagram Size 07 Shown ...
Page 70: ...70 Fig 98 50TC M08 12 PremierLink Control Wiring Diagram ...
Page 71: ...71 Fig 99 Typical PremierLink Control Wiring Diagram Dual Compressor Sizes 08 12 shown ...
Page 72: ...72 Fig 100 Typical PremierLink Control Wiring Diagram with Humidi MiZer System Option ...
Page 73: ...73 Fig 101 Typical RTU Open Controller Wiring Diagram 50TC 07 Units ...
Page 74: ...74 Fig 102 50TC M08 12 RTU Open Controller Wiring Diagram ...
Page 75: ...75 Fig 103 Typical RTU Open Controller Wiring Diagram 50TC D E08 14 Units ...
Page 76: ...76 Fig 104 RTU Open Controller Wiring Diagram 50TC 16 Unit ...
Page 83: ...83 Fig 113 UltraTech Scroll Compressor ...
Page 84: ......
Page 85: ......