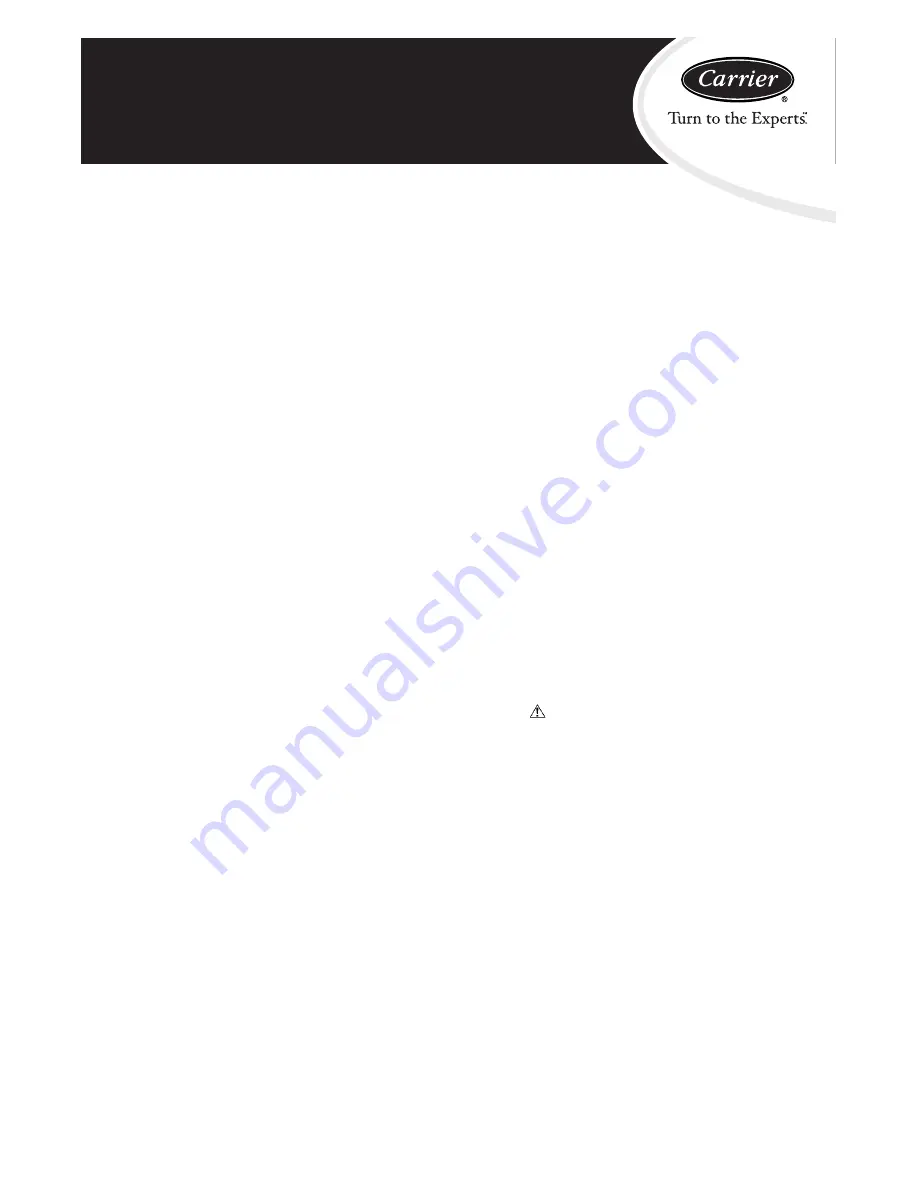
48TC*D08---D14
Nominal 7.5 to 12.5 Tons
With Puron
®
(R---410A) Refrigerant
Service and Maintenance Instructions
TABLE OF CONTENTS
SAFETY CONSIDERATIONS
1
. . . . . . . . . . . . . . . . . . . .
UNIT ARRANGEMENT AND ACCESS
2
. . . . . . . . . . .
SUPPLY FAN (BLOWER) SECTION
4
. . . . . . . . . . . . . .
COOLING
6
. . . . . . . . . . . . . . . . . . . . . . . . . . . . . . . . . . . .
PURON
R
(R--410A) REFRIGERANT
8
. . . . . . . . . . . . . .
COOLING CHARGING CHARTS
10
. . . . . . . . . . . . . . . .
CONVENIENCE OUTLETS
16
. . . . . . . . . . . . . . . . . . . .
SMOKE DETECTORS
17
. . . . . . . . . . . . . . . . . . . . . . . . .
PROTECTIVE DEVICES
24
. . . . . . . . . . . . . . . . . . . . . . .
GAS HEATING SYSTEM
25
. . . . . . . . . . . . . . . . . . . . . .
CONDENSER COIL SERVICE
35
. . . . . . . . . . . . . . . . . .
PREMIERLINK
t
CONTROL
36
. . . . . . . . . . . . . . . . . . .
RTU--MP CONTROL SYSTEM
44
. . . . . . . . . . . . . . . . . .
ECONOMI$ER SYSTEMS
57
. . . . . . . . . . . . . . . . . . . . . .
WIRING DIAGRAMS
66
. . . . . . . . . . . . . . . . . . . . . . . . .
PRE--START--UP
69
. . . . . . . . . . . . . . . . . . . . . . . . . . . . . .
START--UP, GENERAL
69
. . . . . . . . . . . . . . . . . . . . . . . .
START--UP, PREMIERLINK CONTROL
71
. . . . . . . . . .
START--UP, RTU--MP CONTROL
71
. . . . . . . . . . . . . . . .
OPERATING SEQUENCES
75
. . . . . . . . . . . . . . . . . . . . .
FASTENER TORQUE VALUES
85
. . . . . . . . . . . . . . . . .
APPENDIX I. MODEL NUMBER SIGNIFICANCE
87
.
APPENDIX II. PHYSICAL DATA
88
. . . . . . . . . . . . . . . .
APPENDIX III. FAN PERFORMANCE
90
. . . . . . . . . . .
APPENDIX IV. WIRING DIAGRAM LIST
96
. . . . . . . .
APPENDIX V. MOTORMASTER SENSOR
LOCATIONS
97
. . . . . . . . . . . . . . . . . . . . . . . . . . . . . . . . .
UNIT START-UP CHECKLIST
98
. . . . . . . . . . . . . . . . . .
SAFETY CONSIDERATIONS
Installation and servicing of air-conditioning equipment
can be hazardous due to system pressure and electrical
components. Only trained and qualified service personnel
should install, repair, or service air-conditioning
equipment. Untrained personnel can perform the basic
maintenance functions of replacing filters. Trained service
personnel should perform all other operations.
When working on air-conditioning equipment, observe
precautions in the literature, tags and labels attached to
the unit, and other safety precautions that may apply.
Follow all safety codes. Wear safety glasses and work
gloves. Use quenching cloth for unbrazing operations.
Have fire extinguishers available for all brazing
operations.
Follow all safety codes. Wear safety glasses and work
gloves. Use quenching cloth for brazing operations. Have
fire extinguisher available. Read these instructions
thoroughly and follow all warnings or cautions attached to
the unit. Consult local building codes and National
Electrical Code (NEC) for special requirements.
Recognize safety information. This is the safety--alert
symbol
. When you see this symbol on the unit and in
instructions or manuals, be alert to the potential for
personal injury.
Understand the signal words DANGER, WARNING, and
CAUTION. These words are used with the safety--alert
symbol. DANGER identifies the most serious hazards
which
will
result in severe personal injury or death.
WARNING signifies a hazard which
could
result in
personal injury or death. CAUTION is used to identify
unsafe practices which
may
result in minor personal
injury or product and property damage. NOTE is used to
highlight suggestions which
will
result in enhanced
installation, reliability, or operation.
Summary of Contents for WeatherMaker 48TC*D08
Page 10: ...10 COOLING CHARGING CHARTS C08669 Fig 10 Cooling Charging Charts D08 48TC ...
Page 11: ...11 COOLING CHARGING CHARTS C08670 Fig 11 Cooling Charging Charts D12 48TC ...
Page 12: ...12 COOLING CHARGING CHARTS C09151 Fig 12 Cooling Charging Charts D14 Circuit A 48TC ...
Page 13: ...13 COOLING CHARGING CHARTS C09152 Fig 13 Cooling Charging Charts D14 Circuit B 48TC ...
Page 37: ...37 C08665 Fig 43 Typical PremierLinkt System Control Wiring Diagram 48TC ...
Page 45: ...45 C07129 Fig 60 RTU MP Multi Protocol Control Board 48TC ...
Page 46: ...46 C09163 Fig 61 Typical RTU MP System Control Wiring Diagram 48TC ...
Page 67: ...67 C09156 Fig 84 48TC Typical Unit Wiring Diagram Power D08 208 230 3 60 48TC ...
Page 68: ...68 C09157 Fig 85 48TC Typical Unit Wiring Diagram Control D08 208 230 3 60 48TC ...