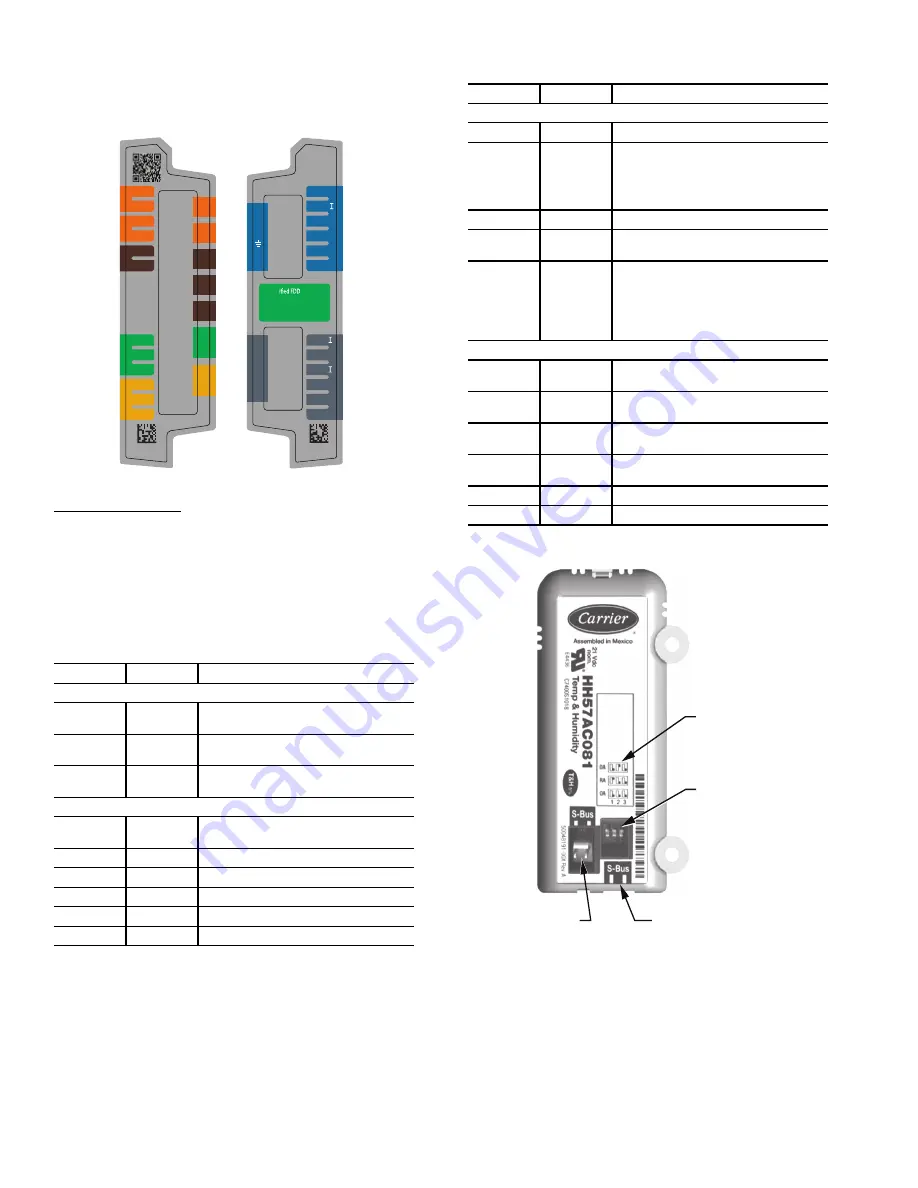
24
ECONOMIZER MODULE WIRING DETAILS — Use
Fig. 38 and Tables 9 and 10 to locate the wiring terminals for
the Economizer module.
NOTE: The four terminal blocks are removable. Slide out each
terminal block, wire it, and then slide it back into place.
Fig. 38 — W7220 Wiring Terminals
S-Bus Sensor Wiring — The labels on the sensors and con-
troller are color coded for ease of installation. Orange labeled
sensors can only be wired to orange terminals on the controller.
Brown labeled sensors can only be wired to S-bus (brown) ter-
minals. Use Fig. 38 and Table 9 to locate the wiring terminals
for each S-Bus sensor.
Use Fig. 38 and Table 12 to set the DIP switches for the de-
sired use of the sensor.
Table 9 — Economizer Module - Left Hand
Terminal Blocks
* Sylk is a registered trademark of Honeywell International Inc.
Table 10 — Economizer Module - Right Hand
Terminal Blocks
Use Fig. 39 and Table 11 to locate the wiring terminals for
each enthalpy control sensor.
Fig. 39 — S-Bus Sensor DIP Switches
LABEL
TYPE
DESCRIPTION
Top Left Terminal Block
MAT
MAT
20k NTC
and COM
Mixed Air Temperature Sensor (Polarity
Insensitive Connection)
OAT
OAT
20k NTC
and COM
Outdoor Air Temperature Sensor
(Polarity Insensitive Connection)
S-BUS
S-BUS
S-BUS
(Sylk* Bus)
Enthalpy Control Sensor
(Polarity Insensitive Connection)
Bottom Left Terminal Block
IAQ 2-10
2-10 vdc
Air Quality Sensor Input (e.g. CO
2
sensor)
IAQ COM
COM
Air Quality Sensor Common
IAQ 24V
24 vac
Air Quality Sensor 24 vac Source
ACT 2-10
2-10 vdc
Damper Actuator Output (2-10 vdc)
ACT COM
COM
Damper Actuator Output Common
ACT 24v
24 vac
Damper Actuator 24 vac Source
NA
AUX2-
OCC
E-GND
EXH1
AUX1-O
Y2-
Y1-
Y2-O
Y1-O
C
R
5004
88
4
8
-002
Rev. A
NA
A2
OCC
EX
A1
Y2I
Y2O
Y1I
Y1O
C
R
Cert
Prod
u
ct
C
a
liforni
a
Title 24, P
a
rt 6
HJW10
www.energy.c
a
.gov
MAT
MAT
OAT
OAT
S
-BU
S
S
-BU
S
IAQ 2-10
IAQ COM
IAQ 24V
ACT 2-10
ACT COM
ACT 24V
MA
MA
OA
OA
S
B
S
B
S
B
S
B
S
B
S
B
V
C
R
V
C
R
NA
50040
83
9-001
Rev. G
LABEL
TYPE
DESCRIPTION
Top Right Terminal Blocks
AUX2 I
24 vac IN
The first terminal is not used.
OCC
24 vac IN
Shut Down (SD) or HEAT (W)
Conventional only
and
Heat Pump Changeover (O-B) in Heat
Pump mode.
E-GND
E-GND
Occupied/Unoccupied Input
EXH1
24 vac
OUT
Exhaust Fan 1 Output
AUX1 O
24 vac
OUT
Programmable:
Exhaust fan 2 output
or
ERV
or
System alarm output
Bottom Right Terminal Blocks
Y2-I
24 vac IN
Y2 in - Cooling Stage 2 Input from
space thermostat
Y2-O
24 vac
OUT
Y2 out - Cooling Stage 2 Output to
stage 2 mechanical cooling
Y1-I
24 vac IN
Y1 in - Cooling Stage 2 Input from
space thermostat
Y1-O
24 vac
OUT
Y1 out - Cooling Stage 2 Output to
stage 2 mechanical cooling
C
COM
24 vac Common
R
24 vac
24 vac Power (hot)
DIP
SWITCH
LABEL
DIP
SWITCHES
(3)
S-BUS
2 PIN SIDE
CONNECTOR
S-BUS
TERMINALS
(1 AND 2)
Summary of Contents for WeatherMaker 48TC 04
Page 4: ...4 Fig 2 Unit Dimensional Drawing ...
Page 5: ...5 Fig 2 Unit Dimensional Drawing cont ...
Page 21: ...21 Fig 34 48TC B07 Unit with Humidi MiZer Adaptive Dehumidification System Humidistat Wiring ...
Page 39: ...39 Fig 45 PremierLink Wiring Schematic ...
Page 40: ...40 Fig 46 PremierLink Wiring Schematic with Humidi MiZer System ...
Page 48: ...48 Fig 65 Typical RTU Open System Control Wiring Diagram ...
Page 49: ...49 Fig 66 Typical RTU Open System Control Wiring Diagram with Humidi MiZer System ...