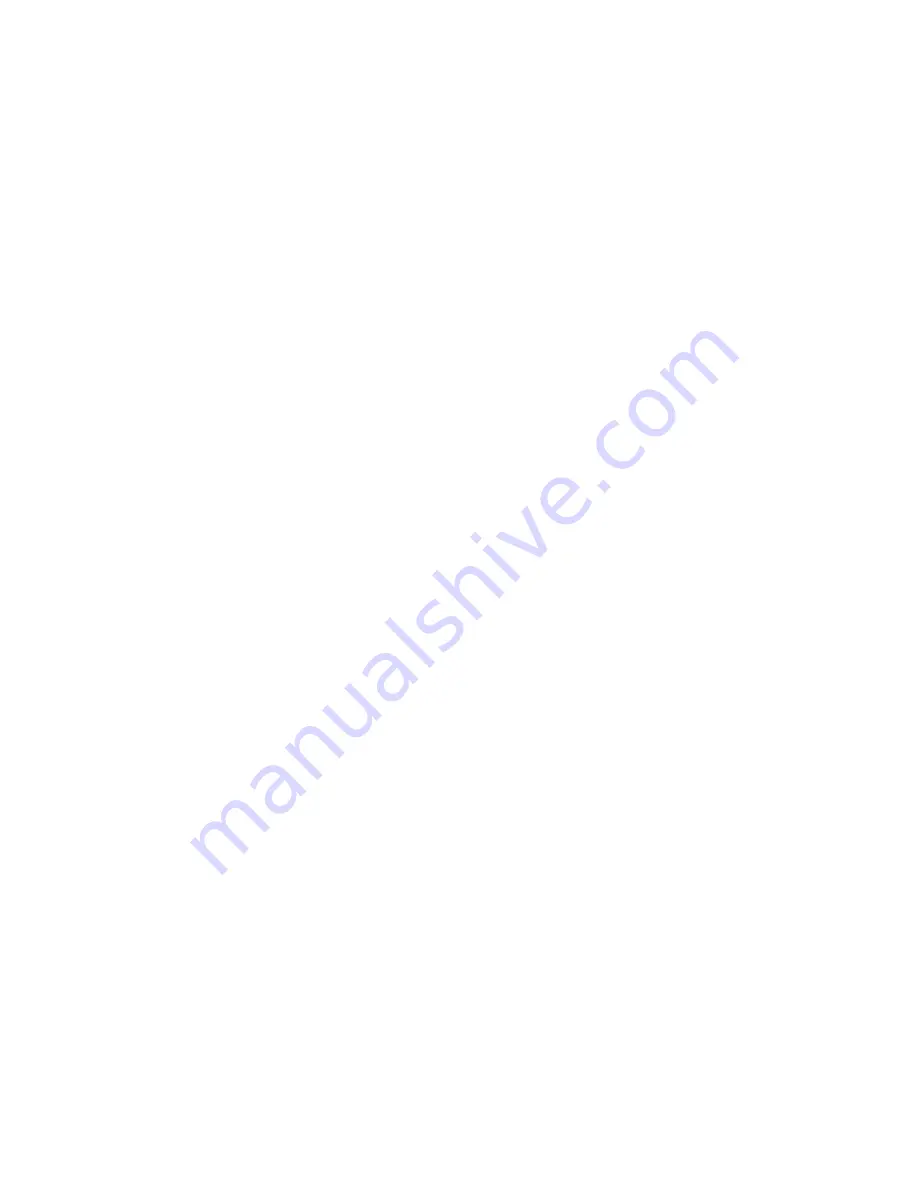
53
High Temp Cap Override (H.TMP)
If stages of mechanical cooling are on and the error is greater
than twice
Y.PLU
, and the rate of change of error is greater
than 0.5
F per minute, then a stage of mechanical cooling will
be added every 30 seconds. This override is intended to react to
situations where the load rapidly increases.
Low Temp Cap Override (L.TMP)
If the error is less than twice
Y.MIN
, and the rate of change of
error is less than –0.5
F per minute, then a mechanical stage
will be removed every 30 seconds. This override is intended to
quickly react to situations where the load is rapidly reduced.
Pull Down Cap Override (PULL)
If the error from set point is above 4
F, and the rate of change
is less than –1
F per minute, then pulldown is in effect, and
“SUM” is set to 0. This keeps mechanical cooling stages from
being added when the error is very large, but there is no load in
the space. Pulldown for units is expected to rarely occur, but is
included for the rare situation when it is needed. Most likely
pulldown will occur when mechanical cooling first becomes
available shortly after the control goes into an occupied mode
(after a warm unoccupied mode).
Slow Change Cap Override (SLOW)
With a rooftop unit, the design rise at 100% total unit capacity
is generally around 30
F. For a unit with 4 stages, each stage
represents about 7.5
F of change to EDT (evaporator discharge
temperature). If stages could reliably be cycled at very fast
rates, the set point could be maintained very precisely. Since it
is not desirable to cycle compressors more than 6 cycles per
hour, slow change override takes care of keeping the PID under
control when “relatively” close to set point.
Humidi-MiZer® Capacity (CAPC)
This variable represents the total reheat capacity currently in
use during a Humidi-MiZer mode. A value of 100% indicates
that all of the discharge gas is being bypassed around the con
-
denser and into the Humidi-MiZer dehumidification/reheat coil
(maximum reheat). A value of 0% indicates that all of the flow
is going through the condenser before entering the Humidi-
MiZer dehumidification/reheat coil (dehum/subcooling mode).
Condenser EXV Position (C.EXV)
This variable represents the position of the condenser EXV
(percent open).
Bypass EXV Position (B.EXV)
This variable represents the position of the bypass EXV (per
-
cent open).
Humidi-MiZer 3-Way Valve (RHV)
This variable represents the position of the 3-way valve used to
switch the unit into and out of a Humidi-MiZer mode. A value
of 0 indicates that the unit is in a standard cooling mode. A val
-
ue of 1 indicates that the unit has energized the 3-way valve
and entered into a Humidi-MiZer mode.
Cooling Control Point (C.CPT)
Displays the current cooling control point (a target value for air
temperature leaving the evaporator coil location). During a Hu
-
midi-MiZer mode, this variable will take on the value of the
dehumidify cool set point (
Configuration
DEHU
D.C.SP)
.
Compressors will stage up or down to meet this temperature.
Evaporator Discharge Temperature (EDT)
Displays the temperature measured between the evaporator
coils and the Humidi-MiZer dehumidification/reheat coil.
Units configured with Humidi-MiZer system have a thermistor
grid installed between these 2 coils to provide the measure
-
ment. This temperature can also be read at
Tempera
-
tures
AIR.T
CCT.
Heating Control Point (H.CPT)
Displays the current heating control point for Humidi-MiZer sys
-
tem. During a Reheat mode, this temperature will be either an off
-
set subtracted from return air temperature (
D.V.RA
) or the Vent
Reheat Set Point (
D.V.HT
). During a Dehumidification mode, this
temperature will take on the value of the original cooling control
point so that the supply air is reheated just enough to meet the sen
-
sible demand in the space. The Humidi-MiZer modulating valves
will adjust to meet this temperature set point.
Leaving Air Temperature (LAT)
Displays the leaving air temperature after the Humidi-MiZer
reheat/dehumidification coil.
SumZ Operation
The SumZ algorithm is an adaptive PID style of control. The
PID (proportional, integral, derivative) is programmed within
the control and the relative speed of staging can only be influ
-
enced by the user through the adjustment of the
Z.GN
configu
-
ration. The capacity control algorithm uses a modified PID al
-
gorithm with a self-adjusting gain, which compensates for
varying conditions, including changing flow rates across the
evaporator coil.
Previous implementations of SumZ made static assumptions
about the actual size of the next capacity jump up or down.
This control uses a “rise per percent capacity” technique in the
calculation of SumZ, instead of the previous “rise per stage”
method. For each jump up or down in capacity, the control will
know beforehand the exact capacity change brought on. Better
overall staging control can be realized with this technique.
SUM Calculation
— The PID calculation of the “SUM” is
evaluated once every 80 seconds.
SUM = Error + “SUM last time through” +
(3 * Error Rate)
Where:
SUM = the PID calculation
Error = EDT – Cooling Control Point
Error Rate = Error – “Error last time through”
NOTE: “Error” is clamped between –10 and +50 and “Error
rate” is clamped between –5 and +5.
This “SUM” will be compared against the “Z” calculations in de
-
termining whether cooling stages should be added or subtracted.
Z Calculation
— For the “Z” calculation, the control attempts
to determine the entering and leaving-air temperature of the
evaporator coil, and based upon the difference between the 2
during mechanical cooling, determines whether to add or sub
-
tract a stage of cooling. This is the adaptive element.
The entering-air temperature is referred to as
MAT
(mixed-air
temperature) and the leaving-air temperature of the evaporator
coil is referred to as
EDT
(evaporator discharge temperature).
They are found at the local display under the
Tempera
-
tures
CTRL
submenu.
The main elements to be calculated and used in the calculation
of SumZ are:
1. the rise per percent capacity (
R.PCT
)
2. the amount of expected rise for the next cooling stage
addition
3. the amount of expected rise for the next cooling stage sub
-
traction
The calculation of “Z” requires 2 variables:
Z.PLU
, used when
adding a stage, and
Z.MIN
, used when subtracting a stage.
They are calculated with the following formulas:
Z.PLU
=
Z.GN
* (10 + (4*(–
ADD.R
))) * 0.6
Z.MIN
=
Z.GN
* (–10 + (4*(–
SUB.R
))) * 0.6
Summary of Contents for WeatherExpert 48N2
Page 135: ...135 Fig 18 48 50N Typical Power Schematic Nominal 075 Ton Unit Shown ...
Page 136: ...136 Fig 19 48 50N Typical Power Schematic Nominal Ton 90 150 Units Shown ...
Page 137: ...137 Fig 20 48 50N Main Base Board Input Output Connections ...
Page 138: ...138 Fig 21 48 50N RXB EXB CEM Input Output Connections a48 9307 ...
Page 139: ...139 Fig 22 48 50N EXV SCB Input Output Connections a48 9308 ...
Page 140: ...140 Fig 23 48N Typical Modulating Gas Heat Unit Control Wiring ...
Page 141: ...141 Fig 24 50N Typical Electric Heat Unit Control Wiring ...
Page 144: ...144 Fig 27 48N Typical Gas Heat Section Wiring Nominal Ton 120 to 150 Units ...
Page 145: ...145 Fig 28 48 50N Typical Power Component Control Wiring 460 v ...
Page 146: ...146 Fig 29 48 50N Component Control Wiring 575 v Nominal Ton 075 to 150 Units ...
Page 147: ...147 Fig 30 48 50N Component Arrangement Power Box ...
Page 148: ...148 Fig 31 48 50N Component Arrangement Control Box ...
Page 240: ...240 APPENDIX D VFD INFORMATION CONT Fig G VFD Bypass Wiring Diagram WHEN USED ...