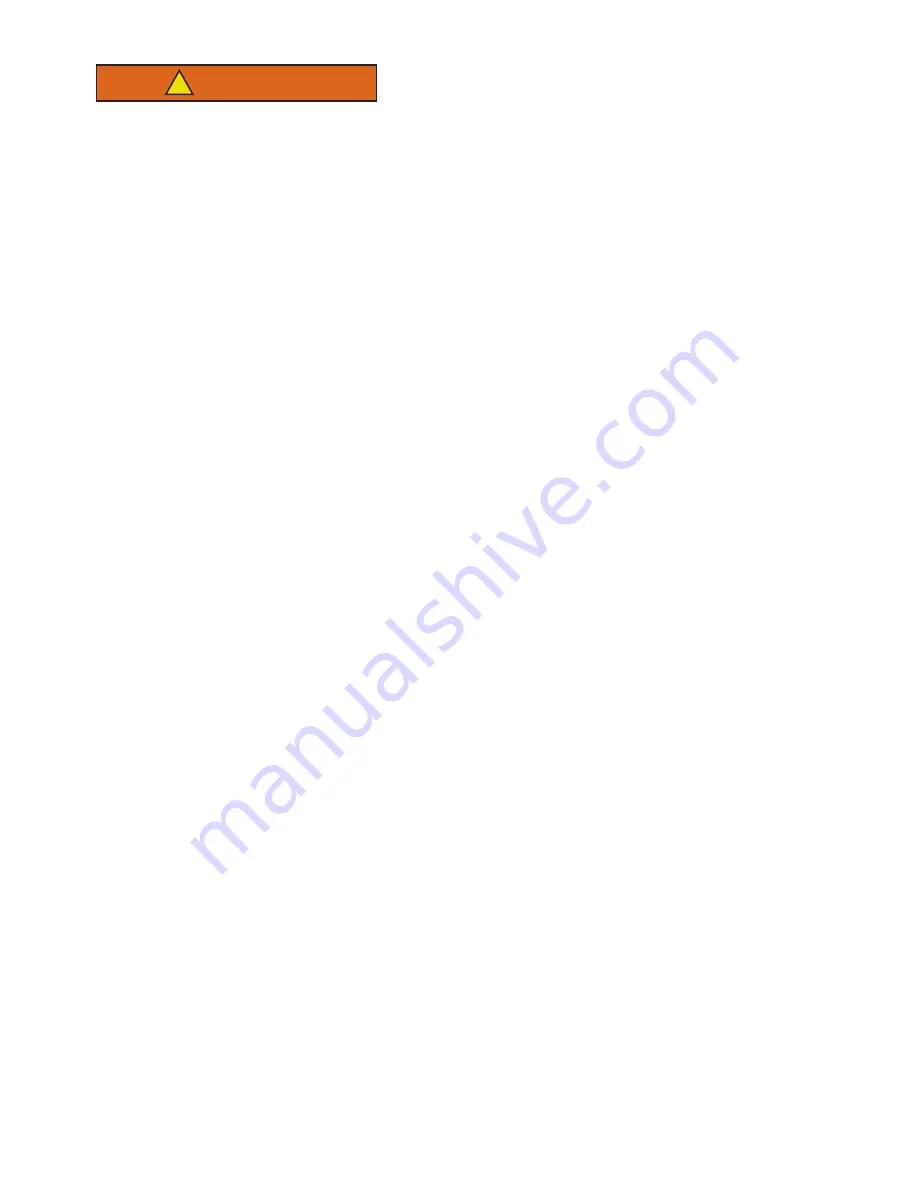
62-11637
8–26
WARNING
!
Do not use a nitrogen cylinder without a
pressure regulator. Cylinder pressure is
approximately 2350 psig (159.9 bar). Do
not use oxygen in or near a refrigerant
system as an explosion may occur. (See
4. Connect a cylinder of dry nitrogen. Use the nitro-
gen to increase the compressor pressure 20 to
150 psig (1.4 to 10.2 bar) to detect the leak. The
larger the leak the less pressure is required. The
smaller the leak, the greater pressure required
5. The recommended procedure for finding leaks
from a compressor is with an electronic leak
detector. Checking joints with soapsuds is satis-
factory only for locating large leaks, or pinpoint-
ing small leaks once a general area has been
located.
6. Once leak checking is complete, remove the
refrigerant/ nitrogen vapor from the compressor.
7. If no leaks are found the compressor is ready for
evacuation. (Skip to Step 10)
8. If any leaks are found they must be repaired
before proceeding.
9. Repeat steps 4 thru 9 as necessary.
10. Disconnect the nitrogen cylinder. Evacuate the
compressor after all leaks are repaired. (Refer
to
.
8.7.4
Evacuation and Dehydration
Moisture is detrimental to refrigerant systems. The
presence of moisture in a refrigeration system can
have many undesirable effects such as: copper plating,
acid sludge formation, “freeze-up” of the expansion
valve, and formation of acids, resulting in metal corro-
sion. Proper evacuation of the system will remove any
moisture from inside the system.
NOTES
• Essential tools to properly evacuate any system
include a good vacuum pump (5 cfm/8mH vol-
ume displacement, Carrier Transicold part num-
ber 07-00176-11) and a good vacuum indicator
s u c h a s a t h e r m o c o u p l e v a c u u m g a u g e
(micrometer). (Carrier Transicold part number
07-00414-00)
• The use of a compound gauge is not recom-
mended for use in determining when the evacu-
ation process is completed because of its
inherent inaccuracy.
• Standard service hoses are not recommended
for evacuation purposes. Evacuation hoses are
recommended for this procedure.
a. Evacuation of the Complete System
1. Evacuate only after leak check. (Refer to
2. If possible keep the temperature of the major
components (condenser, evaporator, compres-
sor and receiver) above 60°F (15.6°C) to speed
evaporation of moisture. If the temperature is
lower than 60°F (15.6°C), ice might form before
moisture removal is complete. Heat lamps, heat
guns or alternate sources of heat may be used
to raise system temperature.
3. The recommended method to evacuate the sys-
tem is to connect three evacuation hoses with
vacuum pump and vacuum indicator (see
4. Ensure that the operator message panel dis-
plays “RECOVER/LEAK CHK/EVAC MODE”
during the evacuation and dehydration proce-
dures. (Refer to
.) If the control
system switches to Charge Mode during the
process, switch it back to the “RECOVER/LEAK
CHK/EVAC MODE”.
5. Backseat (turn counter-clockwise) the liquid line
service valve, suction service and discharge
service valves.
6. With the unit service valves closed (back seated)
and the vacuum pump and vacuum indicator
valves open, start the pump and draw a deep
vacuum. Shut off the pump and check to see if
the vacuum holds. This operation is to test the
evacuation setup for leaks. Repair if necessary.
7. Midseat the refrigerant system service valves.
Ensure that the operator message panel dis-
plays “RECOVER/LEAK CHK/EVAC MODE”.
8. Start the vacuum pump. Evacuate unit until the
vacuum indicator indicates 2000 microns. Close
the vacuum pump valve and shut off the pump.
Wait a few minutes to ensure the vacuum holds.
9. Break the vacuum with dry nitrogen through the
discharge service valve. Raise system pressure
to approximately 2 psig (0.1 bar). Ensure that
the control system does not switch to the
Charge Mode. If this occurs, switch it back to the
“RECOVER/LEAK CHK/ EVAC MODE” (Refer
to
)
10. Purge nitrogen from system at the suction ser-
vice valve.
Summary of Contents for Transicold X4 7300
Page 21: ...62 11637 1 6 1 3 SAFETY DECALS ...
Page 22: ...1 7 62 11637 62 03958 ...
Page 23: ...62 11637 1 8 ...
Page 24: ...1 9 62 11637 ...
Page 119: ...62 11637 SECTION 6 MESSAGECENTER PARAGRAPH NUMBER Page 6 1 MESSAGECENTER MESSAGES 6 1 ...
Page 278: ......