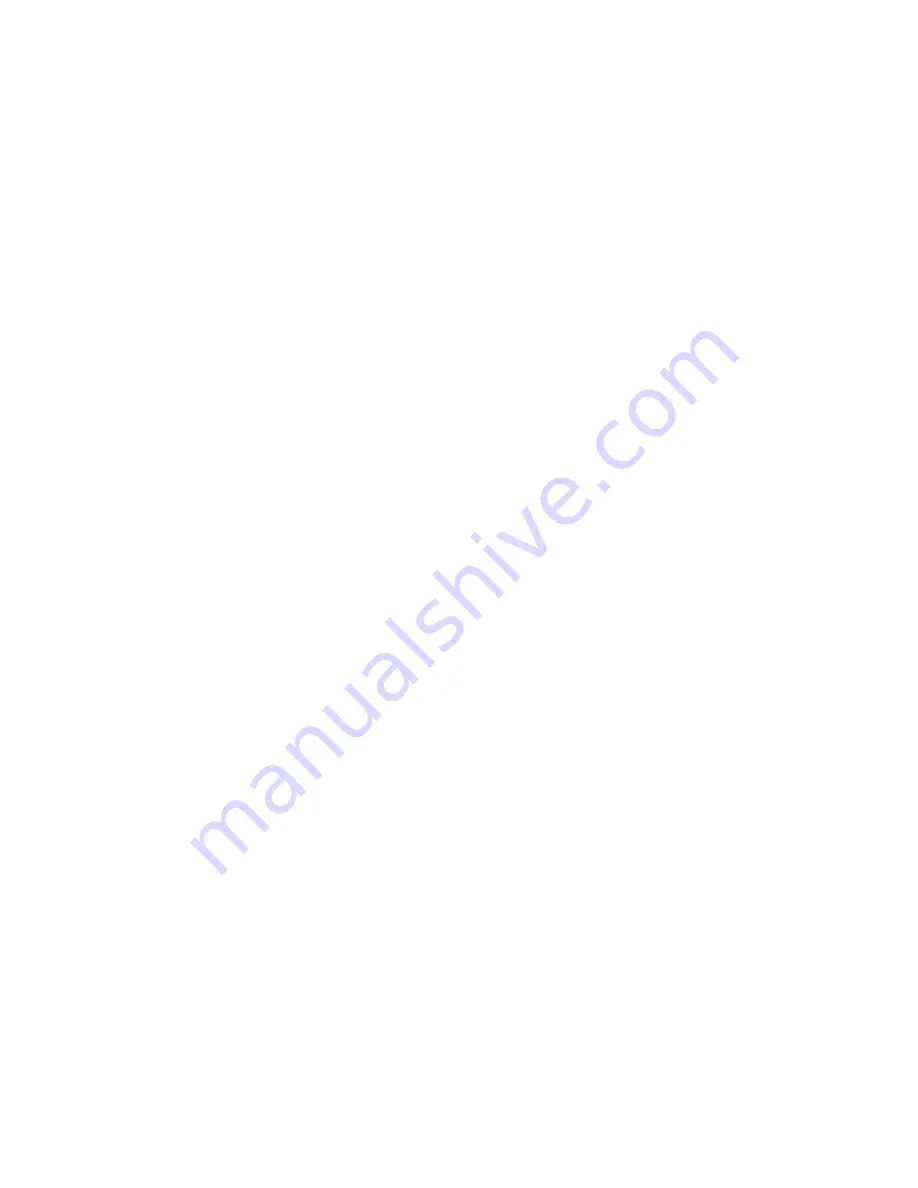
5-15
62-11863
5.9.4
Removing Oil from the Compressor
a. Close suction service valve (frontseat) and pump unit down to 2 to 4 psig (0.1 to 0.3 kg/cm). Frontseat dis-
charge service valve and slowly bleed remaining refrigerant.
b. Remove the oil drain plug from compressor and drain the proper amount of oil from the compressor.
Replace the plug securely back into the compressor.
c. Open service valves and run unit to check oil level, repeat as required to ensure proper oil level.
5.10 COMPRESSOR UNLOADER VALVE
The compressor unloader (located on the compressor cylinder head) is controlled by relay UFR and the tempera-
ture controller.
5.10.1
Checkout Procedure
a. Connect manifold gauges to the compressor suction and discharge service valves and start unit in cooling
with the set point at least 5°F (2.8°C) below box temperature. The compressor will be fully loaded (unloader
coil de-energized). Note suction pressure.
b. Increase set point slowly until unloader valve is energized. Use a ferrous material, such as a screw driver to
check for a magnetic field on the coil when it is energized. Verify suction pressure rise of approximately 3
psig (0.2 bars).
NOTE
If either unloader coil energizes and the suction pressure does not change, the unloader assembly
must be checked.
5.10.2
Solenoid Coil Replacement
NOTE
The coil may be removed without pumping the unit down.
a. Disconnect leads and lift off coil. (see
b. Verify coil type, voltage, and frequency of old and new coil. This information appears on the coil housing.
c. Place new coil over enclosing tube, retainer, and connect wiring.
5.10.3
Replacing Solenoid Valve Internal Parts
a. Pump down the unit (refer to
). Frontseat both service valves to isolate the compressor.
b. Remove coil.
c. Remove enclosing tube collar (
). using installation/removal tool supplied with repair kit.
d. Check plunger for restriction due to: (a) Corroded or worn parts; (b) Foreign material lodged in valve; (c)
Bent or dented enclosing tube.
e. Install new parts. Do not over-tighten enclosing tube assembly. Torque to a value of 100 inch pounds (1.15 mkg).
f. Remove supplied installation/removal tool. Install coil, voltage plate.
g. Evacuate and dehydrate the compressor (refer to
h. Backseat both service valves and open slowly.
i. Start unit and check unloader operation (refer to
Summary of Contents for SUPRA 950Mt
Page 2: ......
Page 4: ......
Page 16: ...62 11863 1 6 1 10 SAFETY DECALS ...
Page 17: ...1 7 62 11863 ...
Page 18: ......
Page 68: ......
Page 74: ......
Page 100: ......
Page 109: ...Figure 8 2 Electrical Schematic Wiring Diagram Sheet 2 of 2 Based on Drawing 62ï ï04104ï ïART ...
Page 110: ......
Page 111: ......
Page 112: ......
Page 115: ......