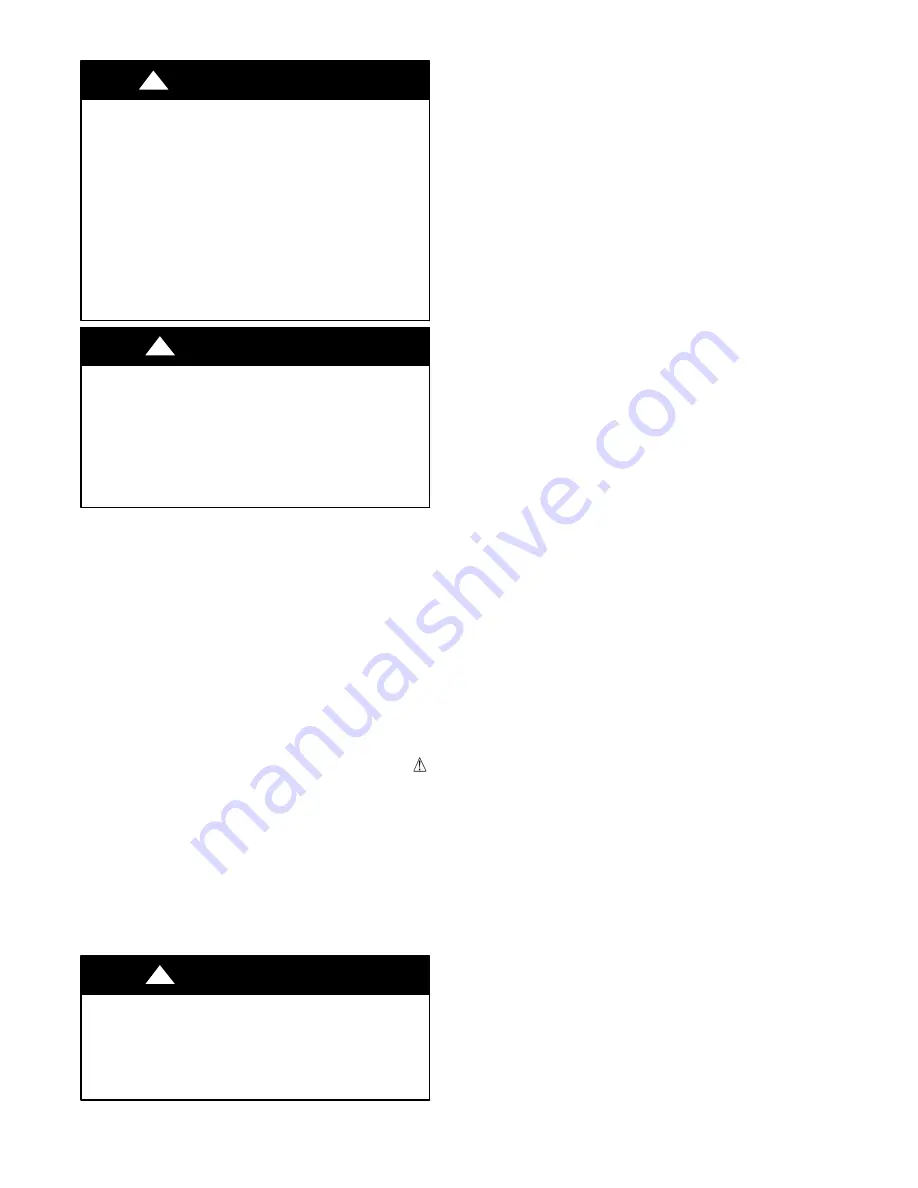
Specifications are subject to change without notice.
2
441 01 1422 00
SAFETY CONSIDERATIONS
FIRE, EXPLOSION, ELECTRICAL SHOCK, AND
CARBON MONOXIDE POISONING HAZARD
Failure to follow this warning could result in dangerous
operation, serious injury, death, or property damage.
Improper installation, adjustment, alteration, service,
maintenance, or use could cause carbon monoxide
poisoning, explosion, fire, electrical shock, or other
conditions which may cause personal injury or property
damage. Consult a qualified service agency, local gas
supplier, or your distributor or branch for information or
assistance. The qualified service agency must use only
factory
−
authorized and listed kits or accessories when
modifying this product.
!
WARNING
FURNACE RELIABILITY HAZARD
Improper installation or misapplication of furnace may
require excessive servicing or cause premature component
failure.
Application of this furnace should be indoors with special
attention given to vent sizing and material, gas input rate,
air temperature rise, unit leveling, and unit sizing.
CAUTION
!
Improper installation, adjustment, alteration, service,
maintenance, or use can cause explosion, fire, electrical shock, or
other conditions which may cause death, personal injury, or
property damage. Consult a qualified installer, service agency, or
your distributor or branch for information or assistance. The
qualified installer or agency must use factory
−
authorized kits or
accessories when modifying this product. Refer to the individual
instructions packaged with the kits or accessories when installing.
Follow all safety codes. Wear safety glasses, protective clothing,
and work gloves. Have a fire extinguisher available. Read these
instructions thoroughly and follow all warnings or cautions
include in literature and attached to the unit. Consult local
building codes, the current editions of the current edition of
National Fuel Gas Code (NFGC) NFPA 54/ANSI Z223.1 and the
current edition of National Electrical Code (NEC) NFPA 70.
Recognize safety information. This is the safety
−
alert symbol .
When you see this symbol on the unit and in instructions or
manuals, be alert to the potential for personal injury.
Understand the signal words
DANGER
,
WARNING
, and
CAUTION
. These words are used with the safety
−
alert symbol.
DANGER
identifies the most serious hazards which
will
result in
severe personal injury or death.
WARNING
signifies hazards
which
could
result in personal injury or death.
CAUTION
is
used to identify unsafe practices which
may
result in minor
personal injury or product and property damage.
NOTE
is used
to highlight suggestions which
will
result in enhanced
installation, reliability, or operation.
CUT HAZARD
Failure to follow this caution may result in personal injury.
Sheet metal parts may have sharp edges or burrs. Use care
and wear appropriate protective clothing, safety glasses and
gloves when handling parts and servicing furnaces.
CAUTION
!
1. Use only with type of gas approved for this furnace. Refer
to the furnace rating plate.
2. Install this furnace only in a location and position as spe-
cified in the “Location” section of these instructions.
3. Provide adequate combustion and ventilation air to the
furnace space as specified in “Air for Combustion and
Ventilation” section.
4. Combustion products must be discharged outdoors. Con-
nect this furnace to an approved vent system only, as spe-
cified in the “Venting” section of these instructions.
5. Never test for gas leaks with an open flame. Use a com-
mercially available soap solution made specifically for the
detection of leaks to check all connections, as specified in
the “Gas Piping” section.
6. Always install furnace to operate within the furnace’s in-
tended temperature
−
rise range with a duct system which
has an external static pressure within the allowable range,
as specified in the “Start
−
Up, Adjustments, and Safety
Check” section. See furnace rating plate.
7. When a furnace is installed so that supply ducts carry air
circulated by the furnace to areas outside the space con-
taining the furnace, the return air shall also be handled by
duct(s) sealed to the furnace casing and terminating out-
side the space containing the furnace. See “Air Ducts” sec-
tion.
8. A gas
−
fired furnace for installation in a residential garage
must be installed as specified in the warning box in the
“Location” section.
9. The furnace may be used for construction heat provided
that the furnace installation and operation complies with
the first CAUTION in the LOCATION section of these in-
structions.
10. These Multipoise Gas
−
Fired Furnaces are CSA (formerly
A.G.A. and C.G.A). design
−
certified for use with natural
and propane gases (see furnace rating plate) and for install-
ation in alcoves, attics, basements, closets, utility rooms,
crawlspaces, and garages. The furnace is factory
−
shipped
for use with natural gas. A CSA listed accessory gas con-
version kit is required to convert furnace for use with pro-
pane gas.
11. See Fig. 2 for required clearances to combustible construc-
tion.
12. Maintain a 1
−
in. (25 mm) clearance from combustible ma-
terials to supply air ductwork for a distance of 36 inches
(914 mm) horizontally from the furnace. See current edi-
tion of NFPA 90B or local code for further requirements.
13. These furnaces SHALL NOT be installed directly on car-
peting, tile, or any other combustible material other than
wood flooring. In downflow installations, factory access-
ory floor base MUST be used when installed on combust-
ible materials and wood flooring. Special base is not re-
quired when this furnace is installed on manufacturer’s
coil model numbers END4X, ENW4X or coil casing mod-
el number NAEAis used. See Fig. 2 for clearance to com-
bustible construction information.
INTRODUCTION
This 4
−
way multipoise Category I fan
−
assisted furnace is CSA
design
−
certified. A Category I fan
−
assisted furnace is an
appliance equipped with an integral mechanical means to either
draw or force products of combustion through the combustion
chamber and/or heat exchanger. The furnace is factory
−
shipped
for use with natural gas.
This furnace is not approved for installation in mobile homes,
recreational vehicles, or outdoors. This furnace is designed for
minimum continuous return
−
air temperature of 60
_
F (16
_
C)db
or intermittent operation down to 55
_
F (13
_
C) db such as when