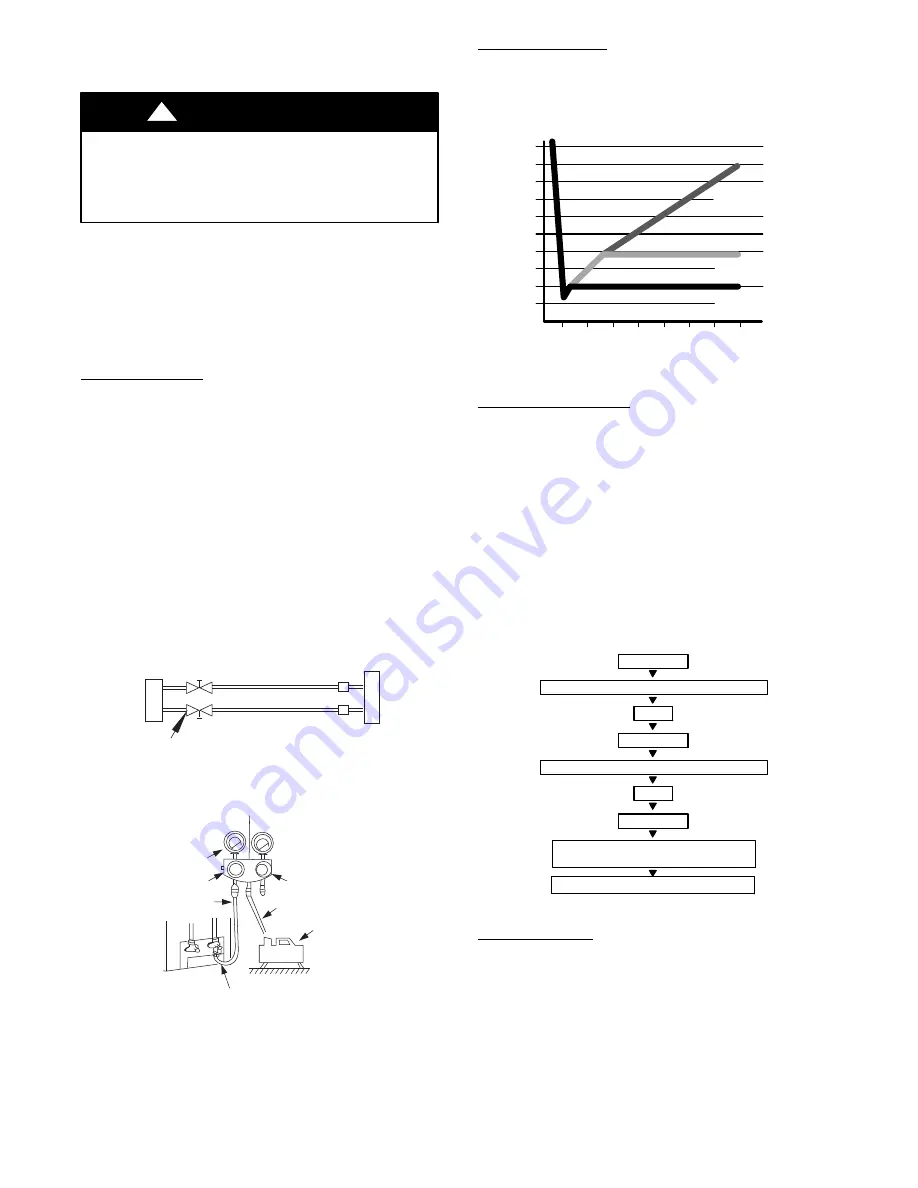
10
SYSTEM EVACUATION AND
CHARGING
UNIT DAMAGE HAZARD
Failure to follow this caution may result in equipment
damage or improper operation.
Never use the system compressor as a vacuum pump.
CAUTION
!
Refrigerant tubes and indoor coil should be evacuated using the
recommended deep vacuum method of 500 microns. The alternate
triple evacuation method may be used if the following procedure is
followed. Always break a vacuum with dry nitrogen.
NOTE: All units (except the 18,000 BTU model) have a Master
Suction and Liquid Line Service Valve.
System Vacuum and Charge
Using Vacuum Pump
1 Completely tighten the flare nuts (A, B, C, D, E). Fully
open all circuits service valves. Connect the manifold gage
charge hose to the charge port of the low side Master service
valve to evacuate all circuits at the same time (see Fig. 8).
2 Connect the charge hose to the vacuum pump.
3 Fully open the low side of manifold gage (see Fig. 9).
4 Start the vacuum pump
5 Evacuate using the triple evacuation method.
6 After evacuation is complete, fully close the low side of
manifold gage and stop the vacuum pump operation.
7 The factory charge contained in the outdoor unit is good for
up to 25ft. (8 m) of line length.
8 Disconnect the charge hose from the charge connection of
the low side service valve.
9 Securely tighten the service valves caps.
Outdoor Unit
Indoor Unit
Refrigerant
Service Valve
Low Side
High Side
A
B
C
D
Fig. 8 – Service Valve
Manifold Gage
500 microns
Low side valve
High side valve
Charge hose
Charge hose
Vacuum pump
Low side valve
Fig. 9 – Manifold
Deep Vacuum Method
The deep vacuum method requires a vacuum pump capable of
pulling a vacuum of 500 microns and a vacuum gage capable of
accurately measuring this vacuum depth. The deep vacuum method
is the most positive way of assuring a system is free of air and
liquid water (see Fig. 10).
500
MINUTES
0
1
2
3
4
5
6
7
1000
1500
LEAK IN
SYSTEM
VACUUM TIGHT
TOO WET
TIGHT
DRY SYSTEM
2000
MICRONS
2500
3000
3500
4000
4500
5000
Fig. 10 – Deep Vacuum Graph
Triple Evacuation Method
The triple evacuation method should be used. Refer to Fig. 11 and
proceed as follows:
1 Pump system down to 500 MICRONS of mercury and
allow the pump to continue operating for an additional 15
minutes. Unit must maintain 500 microns or less for 30
minutes or more to ensure a dry system.
2 Close the service valves and shut off the vacuum pump.
3 Connect a nitrogen cylinder and regulator to the system and
open until the system pressure is 2 psig.
4 Close the service valve and allow the system to stand for 10
minutes. During this time, dry nitrogen will be able to
diffuse throughout the system absorbing moisture.
5 Repeat this procedure as indicated in Fig. 11. The system
will then be free of any contaminants and water vapor.
CHECK FOR TIGHT, DRY SYSTEM
(IF IT HOLDS DEEP VACUUM)
EVACUATE
BREAK VACUUM WITH DRY NITROGEN
WAIT
EVACUATE
RELEASE CHARGE INTO SYSTEM
BREAK VACUUM WITH DRY NITROGEN
EVACUATE
WAIT
Fig. 11 – Triple Evacuation Method
Final Tubing Check
IMPORTANT:
Check to be certain factory tubing on both
indoor and outdoor unit has not shifted during shipment.
Ensure tubes are not rubbing against each other or any sheet
metal. Pay close attention to feeder tubes, making sure wire ties
on feeder tubes are secure and tight.