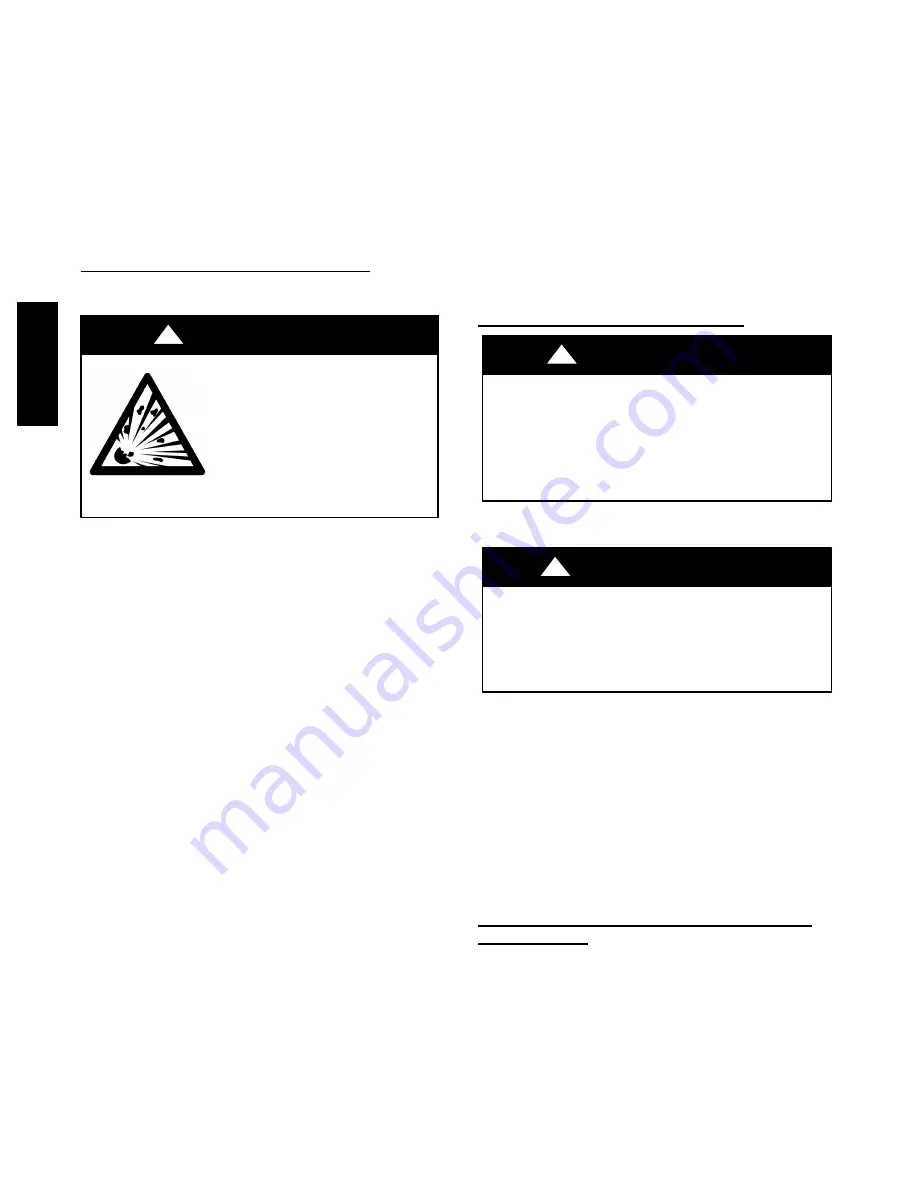
18
Step 2 — Start--Up Adjustments
Complete the required procedures given in the Pre--Start--Up
section before starting the unit. Do not jumper any safety devices
when operating the unit. Do not operate the unit in Cooling mode
when the outdoor temperature is below 40
_
F (4
_
C) (unless
accessory low--ambient kit is installed).
IMPORTANT
: Three--phase, scroll compressors are direction
oriented. Unit must be checked to ensure proper compressor
3--phase power lead orientation. If not corrected within 5 minutes,
the internal protector will shut off the compressor. The 3--phase
power leads to the unit must be reversed to correct rotation. When
turning backwards, the difference between compressor suction and
discharge pressures may be near zero.
Checking and Adjusting Refrigerant Charge
The refrigerant system is fully charged with Puron (R--410A)
refrigerant and is tested and factory sealed.
EXPLOSION HAZARD
Failure to follow this warning could
result in death, serious personal injury,
and/or property damage.
Never use air or gases containing
oxygen for leak testing or operating
refrigerant compressors. Pressurized
mixtures of air or gases containing
oxygen can lead to an explosion.
!
WARNING
NOTE
:
Adjustment of the refrigerant charge is not required
unless the unit is suspected of not having the proper Puron
(R--410A) charge.
NOTE
:
Some units have fixed orifice refrigerant metering
devices. There is a different charging procedure for both expansion
devices. Refer to the correct procedure for your unit.
The charging label and the tables shown refer to system
temperatures and pressures in cooling mode only. A refrigerant
charging label is attached to the inside of the compressor access
panel. (See Fig. 18 Subcool chart for units with TXV and
superheat chart for units with fixed orifice.) The chart includes the
required liquid line temperature at given discharge line pressures
and outdoor ambient temperatures.
A superheat chart is attached to the inside of the compressor access
panel for the unit with fixed metering device. Refer to the charging
procedure on the label.
An accurate thermocouple-- or thermistor--type thermometer, and a
gauge manifold are required when using the subcooling charging
method for evaluating the unit charge. Do not use mercury or small
dial--type thermometers because they are not adequate for this type
of measurement.
NOTE
: Allow system to operate for a minimum of 15 minutes
before checking or adjusting refrigerant charge.
IMPORTANT
:
When evaluating the refrigerant charge, an
indicated adjustment to the specified factory charge must always be
very minimal. If a substantial adjustment is indicated, an abnormal
condition exists somewhere in the cooling system, such as
insufficient airflow across either coil or both coils.
Proceed as follows:
1. Remove caps from low-- and high--pressure service fittings.
2. Using hoses with valve core depressors, attach low-- and
high--pressure gauge hoses to low-- and high--pressure
service fittings, respectively.
3. Start unit and let run until system pressures stabilize.
4. Measure and record the following:
a. Outdoor ambient--air temperature (
F [
C] db).
b. Liquid line temperature (
F [
C]) at TXV.
c. Discharge (high--side) pressure (psig).
d. Suction (low--side) pressure (psig) (for reference only).
5. Using Cooling Charging Charts compare outdoor--air
temperature (
F [
C] db) with the discharge line pressure
(psig) to determine desired system operating liquid line
temperature (See Fig. 18).
6. Compare actual liquid line temperature with desired liquid
line temperature. Using a tolerance of
2
F (
1.1
C), add
refrigerant if actual temperature is more than 2
F (1.1
C)
higher than proper liquid line temperature, or remove
refrigerant if actual temperature is more than 2
F (1.1
C)
lower than required liquid line temperature.
NOTE
:
If the problem causing the inaccurate readings is a
refrigerant leak, refer to Check for Refrigerant Leaks section.
Indoor Airflow and Airflow Adjustments
UNIT OPERATION HAZARD
Failure to follow this caution may result in unit damage.
For cooling operation, the recommended airflow is 350 to
450 cfm for each 12,000 Btuh of rated cooling capacity. For
heating operation, the airflow must produce a temperature
rise that falls within the range stamped on the unit rating
plate.
CAUTION
!
NOTE
: Be sure that all supply--and return--air grilles are open,
free from obstructions, and adjusted properly.
ELECTRICAL SHOCK HAZARD
Failure to follow this warning could result in personal
injury or death.
Disconnect electrical power to the unit and install lockout
tag before changing blower speed.
!
WARNING
This unit is factory-set up for use with a single cooling fan speed.
In addition, this unit has the field-selectable capability to run two
different cooling fan speeds: The rated cooling fan speed (350~400
CFM/Ton) and an enhanced dehumidification fan speed (As low as
320 CFM/Ton) for use with either a dehumidistat or a thermostat
that supports dehumidification.
The cooling speed is marked “LOW” on the interface fan board
(IFB) (See Fig. 16) . The factory-shipped settings are noted in
Table 5. There are 4 additional speed tap wires available for use in
either electric heating or cooling (For color coding on the indoor
fan motor leads, see Table 3). The additional 4 speed tap wires are
shipped loose with vinyl caps and are located in the control box,
near the interface fan board (IFB) (See Fig. 16).
Single Cooling Fan Speed Set-up (Dehumidification
feature not used)
To change cooling speed:
1. Remove the vinyl cap off of the desired speed tap wire
(Refer to Table 3 for color coding). Add the wet coil
pressure drop in Table 8 to the system static to determine the
correct cooling airflow speed in Table 5 that will deliver the
nominal cooling airflow as listed in Table 1 for each size.
2. Remove the current speed tap wire from the “LOW”
terminal on the interface fan board (IFB) (See Fig. 16) and
place vinyl cap over the connector on the wire.
3. Connect the desired speed tap wire to the “LOW” terminal
on the interface fan board (IFB).
607C
--
--
C
Summary of Contents for bryant 607C-C
Page 3: ...3 Fig 2 24 30 Unit Dimensions 607C C ...
Page 4: ...4 Fig 3 36 60 Unit Dimensions 607C C ...
Page 11: ...11 A150518 Fig 12 Connection Wiring Schematics 208 230 1 60 607C C ...
Page 12: ...12 A150519 Fig 12 Cont Ladder Wiring Schematics 208 230 1 60 607C C ...
Page 13: ...13 A150520 Fig 13 Connection Wiring Schematics 208 230 3 60 607C C ...
Page 14: ...14 A150521 Fig 13 Cont Ladder Wiring Schematics 208 230 3 60 607C C ...
Page 15: ...15 A150522 Fig 14 Connection Wiring Diagram 460 3 60 607C C ...
Page 16: ...16 A150523 Fig 14 Cont Ladder Wiring Diagram 460 3 60 607C C ...