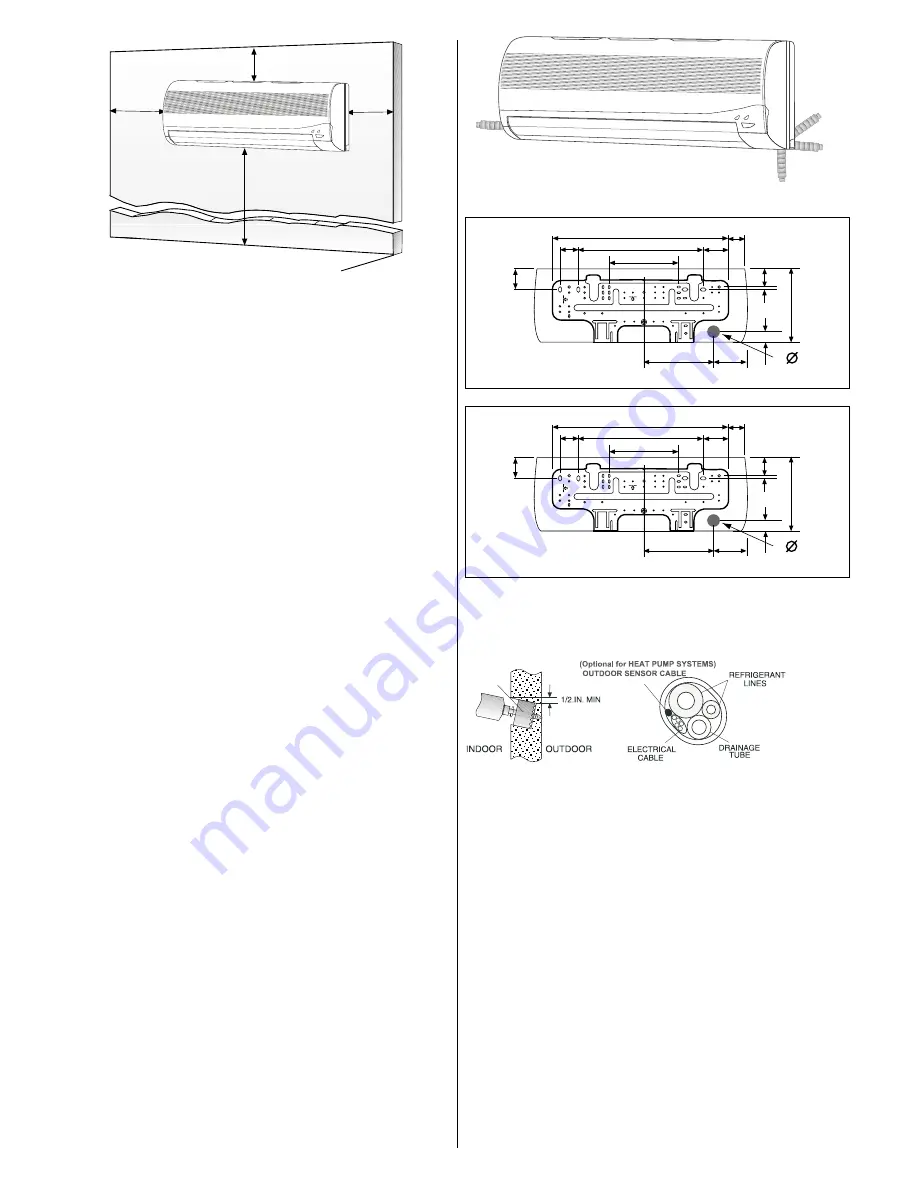
6
6" (0.15m) min.
8"
(0.2m)
min.
6'-8'3"
8"
(0.2m)
min.
(1.8-2.5m)
1
3
2
4
G-2
270
125
260
45
9
45
90
80
635
450
250
66
54
A
09, 12
ALL DIMENSIONS ARE IN mm
G-2
10.63
4.92
10.24
1.77
0.35
1.77
3.5
3.15
25
17.72
9.84
2.6
2.1
A
09, 12
ALL DIMENSIONS ARE IN inches
2.5
64
2.5-IN.
Fig. 2 — Indoor Unit Clearances
INSTALLATION
Plan the installation carefully to avoid component failures
and make installation easier.
Indoor Unit Installation
REFRIGERANT LINE ROUTING — The refrigerant lines may
be routed in any of the four directions shown in Fig. 3.
INSTALL THE MOUNTING BRACKET
1. Carefully remove the mounting bracket, which is
connected to the back of the indoor unit's base with screws.
2. Position the mounting bracket on the wall and level it
using a spirit level (see Fig. 2 for minimum required
clearance distances).
3. Mark the four drilling holes on the wall, as they appear in
Fig. 4.
4. Drill the holes, insert the wall plugs and use four long
screws to attach the mounting bracket to the wall.
5. Check that the bracket is leveled and securely fastened to
the wall.
DRILL A HOLE IN THE WALL FOR DRAINAGE
AND INTER-UNIT CONNECTIONS-
To make the connections between the indoor and outdoor units,
drill a 2.5-in. hole through the wall for the refrigerant lines, drain-
age hose and control cable passage as shown in Fig. 5.
1. Mark the center of the hole to be drilled according to the
refrigerant line routing used and dimensions shown in Fig.
4.
2. Make sure to drill outwards and downwards, so that the
opening in the outside wall is at least 1/2" lower than the
opening on the inside.
3. Make sure the drainage hose is at the bottom side of the
hole.
4 . If refrigerant line route no. 1,2 or 4 are used, use a small
saw blade to carefully remove the corresponding plastic
covering on the side panel.
5. Run the outdoor sensor cable, electrical cable, refrigerant
lines, and drainage tube through the hole.
6. Fill the remaining wall hole gap with an appropriate
sealant material.
Fig. 3 — Refrigerant Lines
Fig. 4 — Mounting Bracket 38BNC/BNQ 009, 012
Fig. 5 — Drill Holes