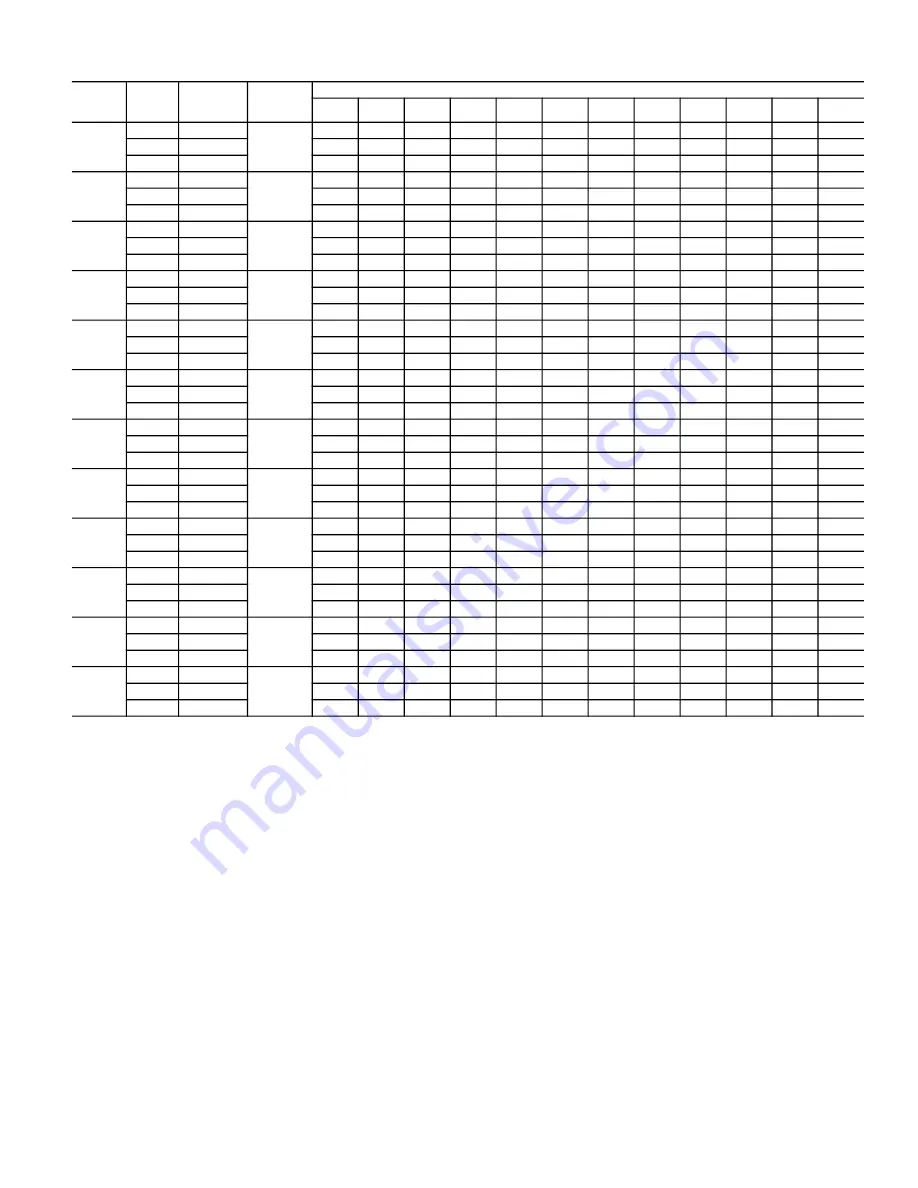
43
Table 11 —
50PS Blower Performance, Standard Motor - PSC for 007-012, Constant Torque ECM for 015-070
50PS
MODEL
SIZE
TAP #
MOTOR
SPEED
DEFAULT
FACTORY
SETTING
AVAILABLE EXTERNAL STATIC PRESSURE (INCHES OF WATER COLUMN)
0.1
0.2
0.3
0.4
0.5
0.6
0.7
0.8
0.9
1
1.1
1.2
007
3
High
LOW
430
420
390
360
335
310
260
—
—
—
—
—
2
Medium
420
390
365
335
310
270
—
—
—
—
—
—
1
Low
370
360
340
315
285
245
—
—
—
—
—
—
009
3
High
MED
430
420
390
360
335
310
260
—
—
—
—
—
2
Medium
420
390
365
335
310
270
—
—
—
—
—
—
1
Low
370
360
340
315
285
245
—
—
—
—
—
—
012
3
High
HI
450
435
415
400
385
360
330
305
—
—
—
—
2
Medium
425
405
385
375
360
335
310
—
—
—
—
—
1
Low
390
380
365
350
335
315
290
—
—
—
—
—
015
3
High
MED/2
710
685
650
610
575
545
460
370
—
—
—
—
2
Medium
530
510
480
445
405
360
—
—
—
—
—
—
1
Low
430
410
370
335
290
245
—
—
—
—
—
—
018
3
High
MED/2
808
795
768
736
703
658
576
495
—
—
—
—
2
Medium
615
575
540
500
460
420
—
—
—
—
—
—
1
Low
540
510
480
445
405
360
—
—
—
—
—
—
024
3
High
MED/2
975
945
910
880
855
825
790
750
—
—
—
—
2
Medium
905
885
855
825
790
755
700
650
—
—
—
—
1
Low
725
700
670
640
585
530
—
—
—
—
—
—
030
3
High
MED/2
1225
1195
1170
1140
1110
1075
1010
940
745
—
—
—
2
Medium
1110
1075
1045
1015
985
955
915
880
700
—
—
—
1
Low
955
925
890
860
825
790
750
715
685
—
—
—
036
3
High
MED/2
1440
1420
1400
1380
1345
1315
1240
1165
1005
845
—
—
2
Medium
1340
1315
1290
1270
1245
1225
1180
1135
990
845
—
—
1
Low
1190
1165
1140
1115
1090
1065
1040
1020
915
810
—
—
042
3
High
MED/2
1645
1635
1610
1585
1560
1535
1510
1485
1460
1430
—
—
2
Medium
1455
1425
1400
1375
1345
1320
1290
1260
1225
1190
—
—
1
Low
1220
1190
1160
1130
1100
1070
1015
955
895
830
—
—
048
3
High
MED/2
1840
1820
1795
1775
1745
1720
1695
1670
1645
1615
—
—
2
Medium
1655
1635
1610
1585
1560
1535
1510
1485
1460
1430
—
—
1
Low
1455
1425
1400
1375
1345
1320
1290
1260
1225
1190
—
—
060
3
High
MED/2
2225
2195
2165
2135
2105
2075
2045
2015
1980
1945
1900
1850
2
Medium
2070
2045
2015
1990
1960
1925
1895
1870
1840
1810
1685
1600
1
Low
1815
1785
1755
1725
1695
1665
1630
1595
1555
1515
1425
—
070
3
High
MED/2
2560
2520
2480
2440
2400
2360
2320
2275
2245
2210
2150
2050
2
Medium
2440
2400
2360
2320
2280
2245
2200
2155
2120
2085
2000
1900
1
Low
1920
1880
1835
1795
1745
1695
1655
1615
1570
1520
1425
—
Summary of Contents for AQUAZONE 50PSH
Page 17: ...17 Fig 15 PSC Motor Single Phase Single Stage WSHP Open Control ...
Page 20: ...20 Fig 18 Constant Torque Motor Single Phase Single Stage WSHP Open Control ...
Page 23: ...23 Fig 21 Constant Airflow Single Phase WSHP Open ...
Page 26: ...26 Fig 24 PSC Motor Three Phase Single Stage WSHP Open ...
Page 29: ...29 Fig 27 Constant Torque Motor Three Phase Single Stage WSHP Open ...
Page 32: ...32 Fig 30 Constant Airflow Motor Three Phase Single Stage WSHP Open ...