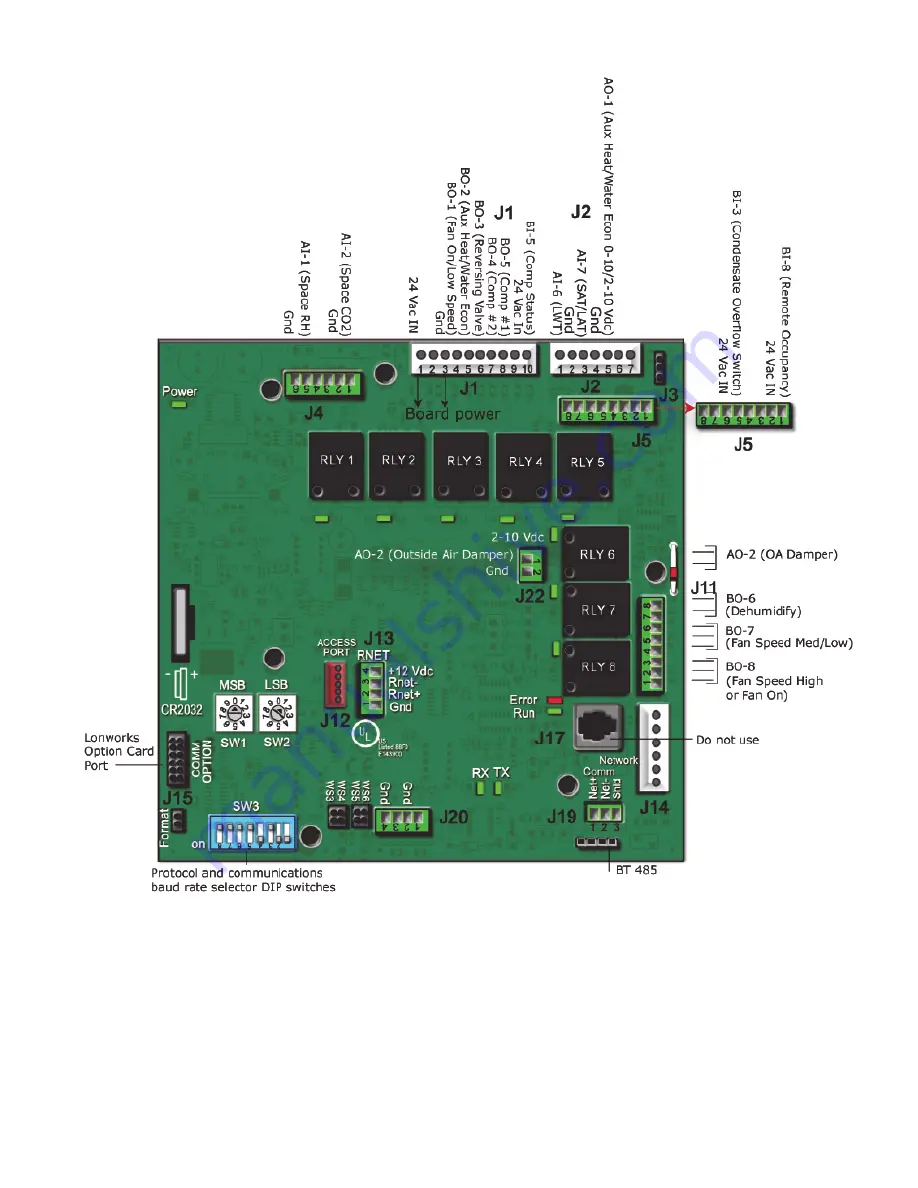
41
Fig. 25 — WSHP Open Control Board
AUXILIARY MODULATING HOT WATER / STEAM
HEATING REHEAT
The control can modulate a hot water or steam valve connected to
a coil on the discharge side of the unit and supplied by a boiler in
order to maintain the desired heating setpoint should the compres-
sor capacity be insufficient or a compressor failure occurs. Unless
the compressor fails, the valve will only operate to supplement the
heat provided by the compressor if the space temperature falls two
degrees or more below the desired heating setpoint. The valve will
be controlled so the SAT will not exceed the Maximum Heating
SAT limit.
2-POSITION HOT WATER / STEAM HEATING REHEAT
The control can operate a two position, NO or NC, hot water or
steam valve connected to a coil on the discharge side of the unit
and supplied by a boiler in order to maintain the desired heating
setpoint should the compressor capacity be insufficient or a com-
pressor failure occurs. Unless the compressor fails, the valve will
only open to supplement the heat provided by the compressor if
the space temperature falls two degrees or more below the desired
heating setpoint. The valve will be controlled so the SAT will not
exceed the Maximum Heating SAT limit and subject to a two min-
ute minimum OFF time to prevent excessive valve cycling.