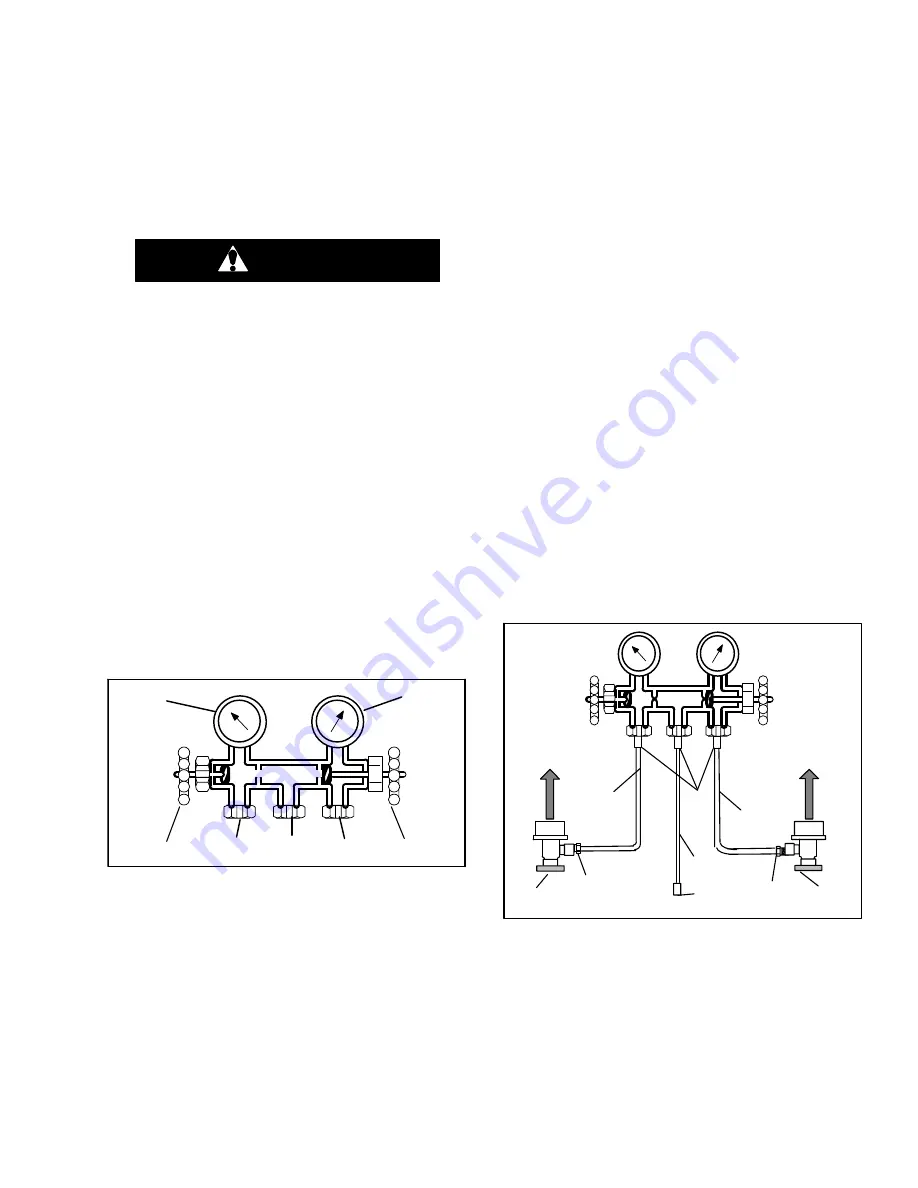
6
−
1
T-364
SECTION 6
SERVICE
NOTE
Use a refrigerant recovery system whenever
removing refrigerant. When working with refrig-
erants you must comply with all local govern-
ment environmental laws. In the U.S.A., refer to
EPA section 608.
WARNING
EXPLOSION HAZARD Failure to follow this
WARNING can result in death, serious
personal injury and / or property damage.
Never use air or gas mixtures containing
oxygen (O
2
) for leak testing or operating the
product.
Charge only with R
−
134a: Refrigerant must
conform to AHRI Standard 700
specification.
6.1 SECTION LAYOUT
Service procedures are provided in this section
beginning with refrigeration system service, then
refrigeration system component service, electrical
system service, temperature recorder service and
general service. Refer to the Table of Contents to locate
specific topics.
6.2 MANIFOLD GAUGE SET
The manifold gauge set (see Figure 6
1) is used to
determine system operating pressure, add refrigerant
charge, and to equalize or evacuate the system.
1. Suction Pressure Valve (shown backseated)
2. Suction Pressure Gauge
3. Discharge Pressure Gauge
4. Discharge Pressure Valve (shown frontseated)
5. High Side Connection
6. Utility Connection to:
a. Refrigerant cylinder
b. Vacuum Pump
c. Oil Container
7. Low Side Connection
Figure 6
−
1 Manifold Gauge Set
When the Suction Pressure Valve (1) is frontseated
(turned all the way in), the suction (low) pressure can be
checked at the Suction Pressure Gauge (2).
When the Discharge Pressure Valve (4) is frontseated,
the discharge (high) pressure can be checked at the
Discharge Pressure Gauge (3).
When both valves are backseated (all the way out), high
pressure vapor will flow into the low side.
When the Suction Pressure Valve (1) is open and the
Discharge Pressure Valve (4) shut, the system can be
charged through the Utility Connection (6). Oil can also
be added to the system.
A R-134a manifold gauge/hose set with self-sealing ho-
ses (see Figure 6
2) is required for service of the mod-
els covered within this manual. The manifold gauge/
hose set is available from Carrier Transicold. (Carrier
Transicold part number 07-00294-00, which includes
items 1 through 6, Figure 6
If the manifold gauge/hose set is new or was exposed to
the atmosphere, it will need to be evacuated to remove
contaminants and air as follows:
1. Backseat (turn counterclockwise) both field service
couplings (see Figure 6
2) and midseat both hand
valves.
2. Connect the yellow hose to a vacuum pump and re-
frigerant 134a cylinder.
3. Evacuate to 10 inches of vacuum and then charge
with R-134a to a slightly positive pressure of 0.1 kg/
cm
2
(1.0 psig).
4. Frontseat both manifold gauge set valves and dis-
connect from cylinder. The gauge set is now ready
for use.
Â
Â
ÂÂ
ÂÂ
Â
Â
To High Side
Access Valve
Â
To Low Side
Access Valve
1. RED Refrigeration and/or Evacuation Hose
(SAE J2196/R-134a)
2. Hose Fitting (0.5-16 Acme)
3. YELLOW Refrigeration and/or Evacuation Hose
(SAE J2196/R-134a)
4. Hose Fitting with O-ring (M14 x 1.5)
5. High Side Field Service Coupling (Red Knob)
6. BLUE Refrigeration and/or Evacuation Hose
(SAE J2196/R-134a)
7. Low Side Field Service Coupling (Blue Knob)
Figure 6
−
2 R-134a Manifold Gauge/Hose Set
Summary of Contents for 69NT40-561-201
Page 2: ......
Page 11: ......
Page 15: ......
Page 29: ......
Page 81: ......
Page 108: ...7 2 T 364 Based on Drawing 62 11753 Figure 7 2 SCHEMATIC DIAGRAM ...
Page 109: ...7 3 T 364 Based on Drawing 62 11753 Figure 7 3 UNIT WIRING DIAGRAM Sheet 1 of 2 ...
Page 110: ...7 4 T 364 Based on Drawing 62 11753 Figure 7 3 UNIT WIRING DIAGRAM Sheet 2 of 2 ...
Page 111: ......
Page 115: ......
Page 116: ......