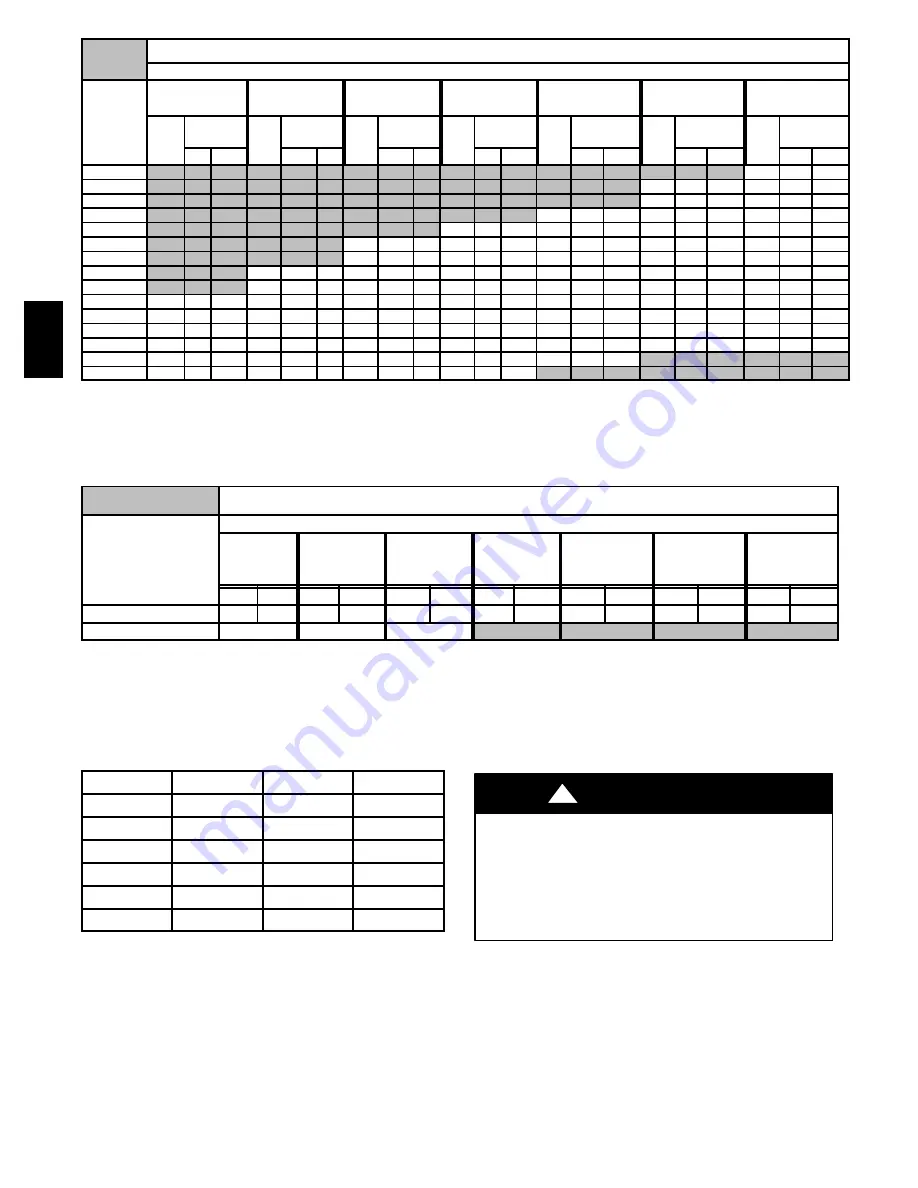
36
Table 7
NATURAL GAS MANIFOLD PRESSURE (in wc)
20,000 BTU per burner
MEAN ELEVATION ABOVE SEA LEVEL ft(m)
HEATING
VALUE at
ALTITUDE
BTU/CU.
FT.
0 to 2000
(0 to 609.6)
2001 to 3000
{
(609.9 to 914.4)
{
3001 to 4000
(914.7 to 1219.2)
4001 to 5000
(1219.5 to 1524)
5001 to 6000
(1524.3 to 1828.8)
6001 to 7000
(1829.1 to 2133.6)
7001 to 8000
(2133.9 to 2438.4)
Orifice
No.
Manifold
Pressure
Orifice
No.
Manifold
Pressure
Orifice
No.
Manifold
Pressure
Orifice
No.
Manifold
Pressure
Orifice
No.
Manifold
Pressure
Orifice
No.
Manifold
Pressure
Orifice
No.
Manifold
Pressure
HI
LO
HI
LO
HI
LO
HI
LO
HI
LO
HI
LO
HI
LO
700
----
----
----
----
----
----
----
----
----
----
----
----
----
----
----
----
----
----
44
3.7
1.8
725
----
----
----
----
----
----
----
----
----
----
----
----
----
----
----
44
3.7
1.8
44
3.4
1.7
750
----
----
----
----
----
----
----
----
----
----
----
----
----
----
----
44
3.5
1.7
44
3.2
1.6
775
----
----
----
----
----
----
----
----
----
----
----
----
44
3.5
1.7
44
3.2
1.6
46
3.8
1.9
800
----
----
----
----
----
----
----
----
----
44
3.6
1.8
44
3.3
1.6
45
3.7
1.8
46
3.6
1.7
825
----
----
----
----
----
----
44
3.7
1.8
44
3.4
1.7
45
3.8
1.8
46
3.6
1.8
47
3.8
1.9
850
----
----
----
----
----
----
44
3.5
1.7
44
3.2
1.6
46
3.7
1.8
46
3.4
1.7
47
3.6
1.7
875
----
----
----
44
3.5
1.7
44
3.3
1.6
46
3.8
1.9
46
3.5
1.7
47
3.7
1.8
48
3.8
1.9
900
----
----
----
44
3.3
1.6
45
3.7
1.8
46
3.6
1.8
47
3.8
1.8
47
3.5
1.7
48
3.6
1.8
925
44
3.7
1.8
44
3.2
1.5
46
3.7
1.8
46
3.4
1.7
47
3.6
1.8
48
3.7
1.8
48
3.4
1.7
950
44
3.5
1.7
45
3.6
1.8
46
3.5
1.7
47
3.7
1.8
47
3.4
1.7
48
3.5
1.7
49
3.8
1.9
975
44
3.3
1.6
46
3.6
1.8
47
3.8
1.9
47
3.5
1.7
48
3.7
1.8
48
3.4
1.6
49
3.6
1.8
1000
44
3.2
1.6
46
3.4
1.7
47
3.6
1.8
48
3.8
1.8
48
3.5
1.7
49
3.8
1.8
49
3.4
1.7
1050
46
3.6
1.8
47
3.5
1.7
48
3.7
1.8
48
3.4
1.7
49
3.7
1.8
----
----
----
----
----
----
1100
47
3.8
1.8
48
3.7
1.8
48
3.4
1.7
49
3.7
1.8
----
----
----
----
----
----
----
----
----
Conversion: 1 in wc = 249 Pa
Bold
-- indicates factory orifice size.
NOTE
: Propane data is based on 1.53 specific gravity. For fuels with different specific gravity consult the National Fuel Gas Code ANSI
Z223.1--2006/NFPA 54--2006 or National Standard of Canada, Natural Gas and Propane Installation Code CSA B149.1--05.
In the USA,
derating of these furnaces at 2% (Natural Gas) and 4% (Propane Gas) has been tested and design--certified by CSA.
{
In Canada
, the input rating must be derated 5% (Natural Gas) and 10% (Propane Gas) for altitudes of 2,000 to 4,500 (609.6 to 1371.6m)
above sea level. Use the 2001 to 3000 (609.9 to 914.4m) column in
Table 7
and
Table 8
.
Table 8
PROPANE GAS MANIFOLD PRESSURE (in wc)
20,000 BTU per burner
MEAN ELEVATION FEET ABOVE SEA LEVEL ft(m)
HEATING VALUE
at ALTITUDE
BTU/CU. FT.
0 to 2000
(0 to 609.6)
2001 to 3000
{
(609.9 to
914.4)
{
3001 to 3999
(914.7 to
1219.2)
4001 to 5000
(1219.5 to 1524)
5001 to 6000
(1524.3 to
1828.8)
6001 to 7000
(1829.1 to
2133.6)
7001 to 8000
(2133.9 to
2438.4)
Hi
Lo
Hi
Lo
Hi
Lo
Hi
Lo
Hi
Lo
Hi
Lo
Hi
Lo
2500
10.0
4.9
8.9
4.4
8.4
4.1
10.0
4.9
10.0
4.9
10.0
4.9
10.0
4.9
Orifice Size
#55
#55
#55
#56
#56
#56
#56
Conversion: 1 in wc = 249 Pa
NOTE
:
Propane data is based on 1.53 specific gravity. For fuels with different specific gravity consult the National Fuel Gas Code A
NSI
Z223.1--2006/NFPA 54--2006 or National Standard of Canada, Natural Gas and Propane Installation Code CSA B149.1--05.
In the USA,
derating of these furnaces at 2% (Natural Gas) and 4% (Propane Gas) has been tested and design--certified by CSA.
{
In Canada
, the input rating must be derated 5% (Natural Gas) and 10% (Propane Gas) for altitudes of 2,000 to 4,500 (609.6 to 1371.6m)
above sea level. Use the 2001 to 3000 (609.9 to 914.4m) column in
Table 7
and
Table 8
.
The burner orifice part numbers are as follows:
Orifice
Part #
Orifice
Part #
41
333730--701
42
333730--702
43
333730--703
44
333730--704
45
333730--705
46
333730--709
47
333730--710
48
333730--711
49
333730--712
54
333730--706
55
333730--707
56
333730--708
Changing Orifices for High Altitude
ELECTRICAL
SHOCK, FIRE
OR
EXPLOSION
HAZARD
Failure to follow this warning could result in personal injury,
death, and/or property damage.
Turn OFF electric power (at disconnect) and gas supply (at
manual valve in gas line) when installing orifices. Installation
of orifices requires a qualified service technician.
!
WARNING
NOTE:
Main burner orifices can be changed for high altitudes.
1. Disconnect gas line from gas valve.
2. Remove manifold from furnace.
3. Remove the orifices from the manifold and replace them
with properly sized orifices.
4. Tighten orifices so it is seated and gas tight. (See Fig. 39.)
58H
D
V