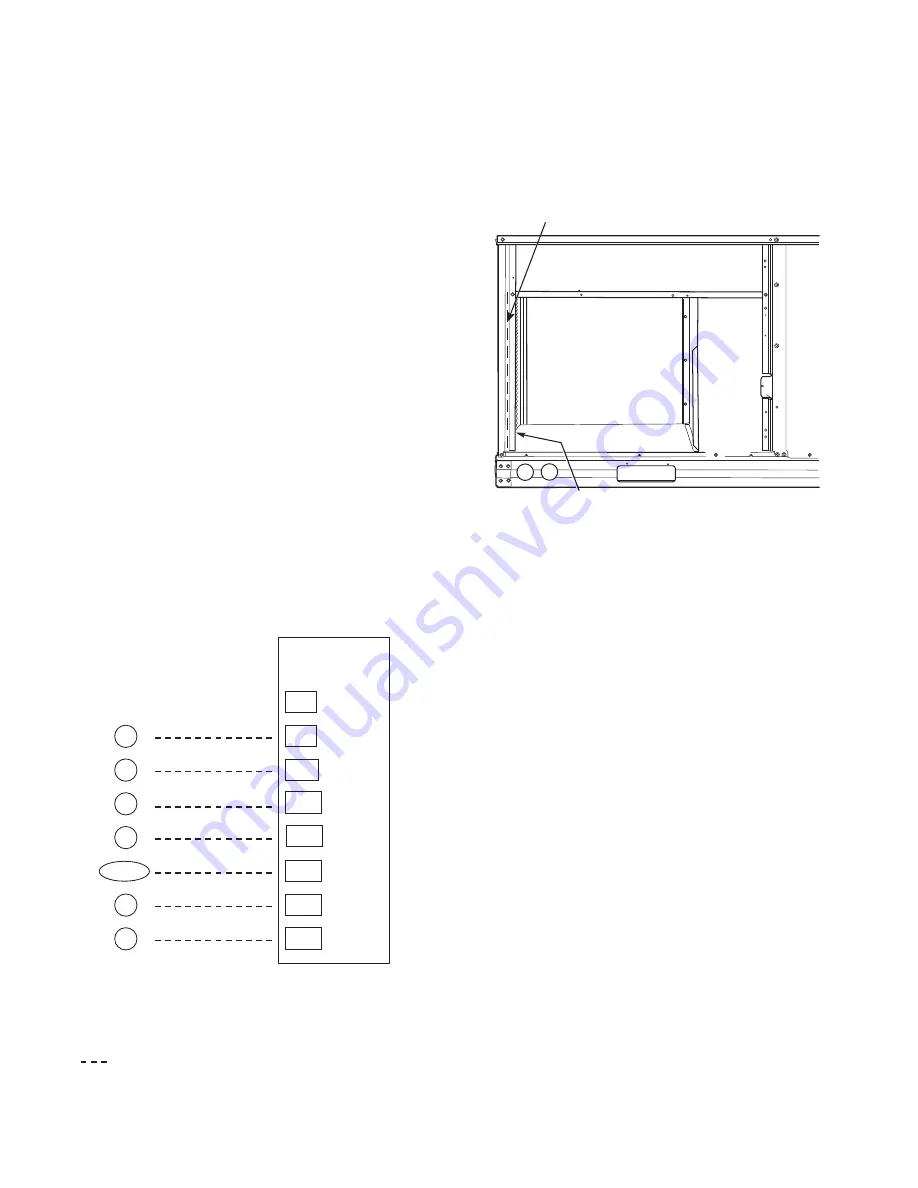
20
FIELD CONTROL WIRING
The 50HC unit requires an external temperature control device.
This device can be a thermostat (field-supplied) or a Premier-
Link™ controller (available as factory-installed option or as field-
installed accessory, for use on a Carrier Comfort Network
®
or as a
stand-alone control) or the RTU Open Controller for Building
Management Systems using non-CCN protocols (RTU Open is
available as a factory-installed option only).
THERMOSTAT
Select a Carrier-approved accessory thermostat. When electric
heat is installed in the 50HC unit, the thermostat must be capable
of energizing the G terminal (to energize the Indoor Fan Contac-
tor) whenever there is a space call for heat (energizing the W1 ter-
minal). The accessory thermostats listed on the unit price pages
can provide this signal but they are not configured to enable this
signal as shipped.
Install the accessory thermostat according to installation instruc-
tions included with the accessory.
Locate the thermostat accessory on a solid wall in the conditioned
space to sense average temperature in accordance with the ther-
mostat installation instructions.
If the thermostat contains a logic circuit requiring 24-v power, use
a thermostat cable or equivalent single leads of different colors
with minimum of seven leads. If the thermostat does not require a
24-v source (no “C” connection required), use a thermostat cable
or equivalent with minimum of six leads. See Fig. 35. Check the
thermostat installation instructions for additional features which
might require additional conductors in the cable.
For wire runs up to 50 ft. (15 m), use no. 18 AWG (American
Wire Gage) insulated wire [35°C (95°F) minimum]. For 50 to
75 ft. (15 to 23 m), use no. 16 AWG insulated wire [35°C (95°F)
minimum]. For over 75 ft. (23 m), use no. 14 AWG insulated wire
[35°C (95°F) minimum]. Wire sizes larger than no. 18 AWG can-
not be directly connected to the thermostat and will require a junc-
tion box and splice at the thermostat.
Fig. 35 — Low-Voltage Thermostat Connections
Thermostat Wiring, Units Without Thru-Base Connection Kit
Pass the thermostat control wires through the hole provided in the
corner post; then feed the wires through the raceway built into the
corner post to the control box. Pull the wires over to the terminal
strip on the upper-left corner of the Controls Connection Board.
See Fig. 36.
NOTE: If thru-the-bottom connections accessory is used, refer to
the accessory installation instructions for information on routing
power and control wiring.
Fig. 36 — Field Control Wiring Raceway
HEAT ANTICIPATOR SETTINGS
Set heat anticipator settings at 0.14 amp for the first stage and
0.14 amp for second-stage heating, when available.
ELECTRIC HEATERS
The 50HC units may be equipped with factory or field-installed
electric heaters. The heaters are modular in design, with heater
frames holding open coil resistance wires strung through ceramic
insulators, line-break limit switches and a control contactor. One
or two heater modules may be used in a unit.
Heater modules are installed in the compartment below the indoor
(supply) fan outlet. Access is through the indoor access panel.
Heater modules slide into the compartment on tracks along the
bottom of the heater opening. See Fig. 37-39.
Not all available heater modules may be used in every unit. Use
only those heater modules that are UL listed for use in a specific
size unit. Refer to the label on the unit cabinet for the list of ap-
proved heaters.
Unit heaters are marked with heater model numbers, but accessory
heaters are ordered as and shipped in cartons marked with a corre-
sponding heater sales package part number.
NOTE: The value in position 9 of the part number differs between
the sales package part number (value is 1) and a bare heater model
number (value is 0).
X
C
G
W2
R
C
W2
G
W1
O/B/Y2
Y2
W1
R
Y1
Y1
Typical
Thermostat
Connections
T
H
E
R
M
O
S
T
A
T
(Note 1)
(Note 2)
(Note 3)
1. Typical multi-function marking. Follow manufacturer’s configuration
instructions to select Y2.
2. Y2 to Y2 connection required on single-stage cooling units when
integrated economizer function is desired
3. W2 connection not required on units with single-stage heating.
Field Wiring
Central
Terminal
Board
Notes:
RACEWAY
HOLE IN END PANEL (HIDDEN)
Summary of Contents for 50HC Series
Page 4: ...4 Fig 2 50HC 04 06 Units Built On and After 4 15 2019...
Page 5: ...5 Fig 3 50HC 04 06 Units Built Prior to 4 15 2019...
Page 6: ...6 Fig 4 50HC 04 06 Corner Weights and Clearances...
Page 7: ...7 Fig 5 50HC 04 06 Base Rail Details...
Page 8: ...8 Fig 6 50HC 04 06 Thru the Base Charts...
Page 25: ...25 Fig 47 Electro Mechanical Control Wiring Diagram...
Page 26: ...26 Fig 48 Electro Mechanical Control Wiring Diagram with Humidi MiZer System...
Page 27: ...27 Fig 49 Electro Mechanical Control Power Wiring Diagram...
Page 31: ...31 Fig 53 PremierLink Wiring Schematic...
Page 32: ...32 Fig 54 PremierLink Wiring Schematic with Humidi MiZer System...
Page 33: ...33 Fig 55 RTU Open System Control Wiring Diagram...
Page 34: ...34 Fig 56 RTU Open System Control Wiring Diagram with Humidi MiZer System...
Page 49: ......