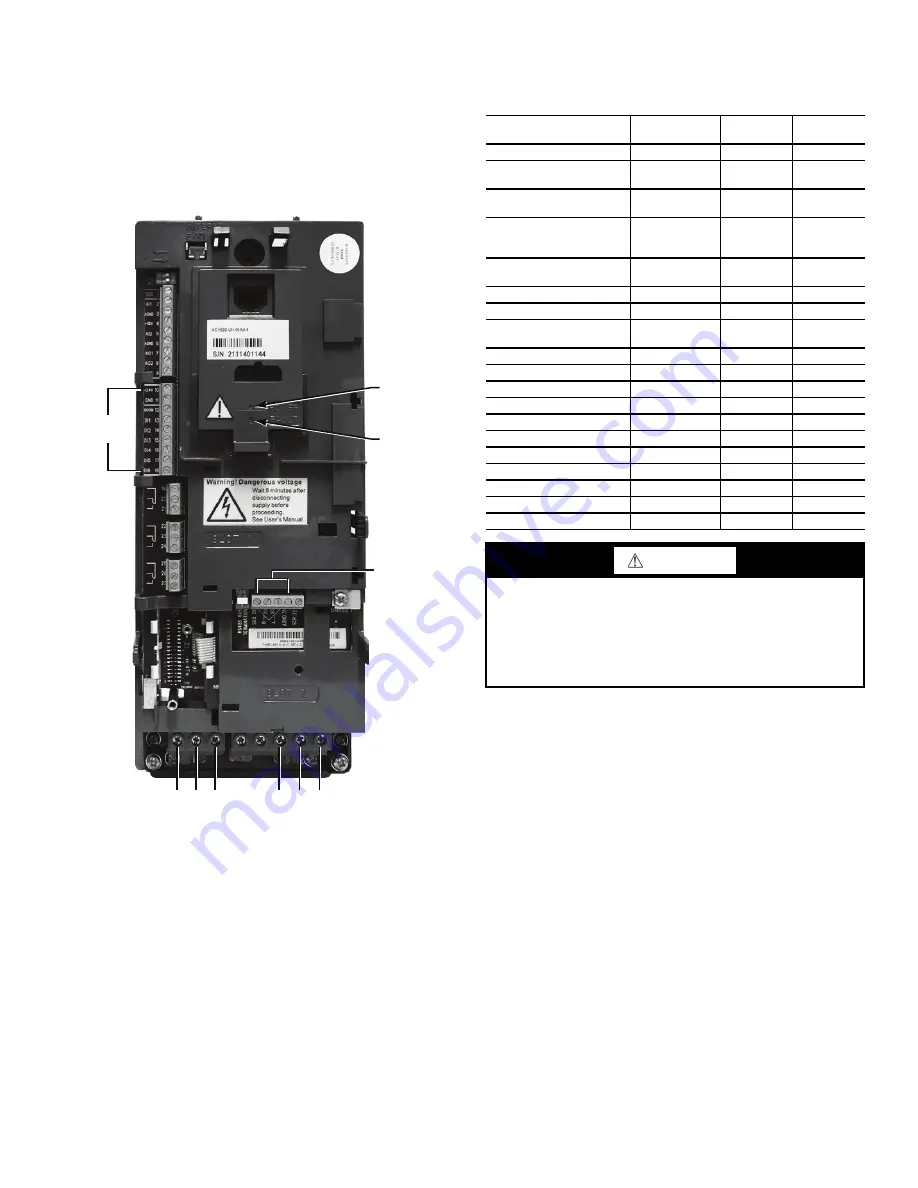
121
APPENDIX C — VARIABLE FREQUENCY DRIVE (VFD)
On units equipped with supply fan VFDs, the indoor fan motor is
controlled by a 3-phase VFD. The supply fan VFD is located in
the supply fan section behind the access door. These units use
ABB VFDs. The VFD varies the frequency of the AC voltage
supplied to the indoor fan. This allows the variance in the speed of
the fan. The VFD is always powered during normal operation and
the fan is stopped by driving the speed to 0. Fig. A and Table P
show the VFD terminals and connections.
Fig. A — Variable Frequency Drive (VFD) Terminals
and Connections - Unit Shown with Front Cover
Removed
The VFD is factory-configured to match the current and power
requirements for each motor selection and all wiring connections
are completed by the factory; no field adjustments or connec-
tions are necessary. While the basic VFD retains all of its stan-
dard capabilities, this application uses only a limited portion of
these features to provide discrete output speeds to the motor.
Consequently the VFD is not equipped with a keypad. A keypad
is available as an accessory (P/N CRDISKIT001A00) for field-
installation or expanded service access to VFD parameter and
troubleshooting tables. The VFD used has soft start capabilities
to slowly ramp up the speeds, eliminating any high inrush of air
volume during speed changes.
The VFDs communicate to the
Comfort
Link MBB over the local
equipment network (LEN). The VFD speed is controlled directly
by the
Comfort
Link controls over the LEN. The VFD parameters
required to allow the VFD to communicate on the LEN are shown
in Table Q. These are factory set and would only need to be adjust-
ed if replacing the drive. Table R shows VFD parameters that are
set by the
Comfort
Link controls, and sent to the VFD over the
LEN at power up of the VFD. These are hard-coded to be set as
listed. The parameters listed in Table S have corresponding
Com-
fort
Link configurations (
Configuration
I.FAN
S.VFD
). The
factory sets these parameters per motor installed in the unit and
these should not be adjusted in the field. These are only provided
for drive or motor replacement or future adjustments. Table T lists
the status information the VFD sends to the
Comfort
Link controls,
and Table U lists the information the
Comfort
Link controls send to
the VFD. This table is updated at every scan the
Comfort
Link con-
trols perform of the LEN. This occurs approximately once every
second.
TERMINALS
10 – 16
TERMINALS
28 – 31
U1 V1 W1
U2
V2 W2
POWER
LED
FAULT
LED
Table P — VFD Connections
POINT DESCRIPTION
TYPE OF I/O TERMINAL
NUMBER
TERMINAL
NAME
LOW VOLTAGE INPUTS
Low Voltage Power
(jumped to DI1 & DI4)
24vdc 10 24v
Low Voltage Common
(jumped to DCOM)
Ground 11 GND
Discrete Inputs
Common (jumped from
GND)
Ground 12
DCOM
Discrete Input 1
(jumped from 24v)
Switch Input
13
DI1
Not Used
Switch Input
14
DI2
Not Used
Switch Input
15
DI3
Discrete Input 4
(jumped from 24v)
Switch Input
16
DI4
Shielded Cable Ground
Shield 28 SCR
LEN Communication
LEN 29 B+
LEN Communication
LEN 30 A-
LEN Communication
LEN 31
AGND
HIGH VOLTAGE
Voltage Leg from C-11
Voltage Input
U1
MAINS
Voltage Leg from C-13
Voltage Input
V1
MAINS
Voltage Leg from IFTB
Voltage Input
W1
MAINS
Voltage Leg to IFM-3
Voltage Output
U2
MOTOR
Voltage Leg to IFM-2
Voltage Output
V2
MOTOR
Voltage Leg to IFM-1
Voltage Output
W2
MOTOR
WARNING
EQUIPMENT DAMAGE/PERFORMANCE HAZARD
Failure to follow this caution may result in damage to the unit
or
in degradation of unit performance.
Do not run the Carrier Assistant through the VFD keypad.
This will cause parameters to change value that are not de-
sired on these applications.
Summary of Contents for /50HC 04-28
Page 69: ...69 Fig 24 Typical Control Diagram for 48HC 04 14 Units 48HC 08 09 shown ...
Page 70: ...70 Fig 25 Typical Power Diagram for 48HC 04 14 Units 48HC 08 09 shown ...
Page 71: ...71 Fig 26 Typical Control Diagram for 50HC 04 14 Units 50HC 14 shown ...
Page 72: ...72 Fig 27 Typical Power Diagram for 50HC 04 14 Units 50HC 14 Non Humidi MiZer shown ...
Page 73: ...73 Fig 28 Typical Control Diagram 48HC 17 28 Units ...
Page 74: ...74 Fig 29 Typical Control Diagram 50HC 17 28 Units ...
Page 75: ...75 Fig 30 Typical Humid MiZer Power Diagram and Component Arrangement 48 50HC 17 28 Units ...
Page 76: ...76 Fig 31 Typical Non Humid MiZer Power Diagram and Component Arrangement 48 50HC 17 28 Units ...
Page 89: ...89 Fig 42 Modulating ERV Wiring Schematic ...
Page 90: ...90 Fig 43 EnergyX ERV Control Box Component Layouts ...
Page 101: ...101 Fig 59 Exhaust Fan Assembly Removal Exhaust Fan Assembly ...
Page 141: ......