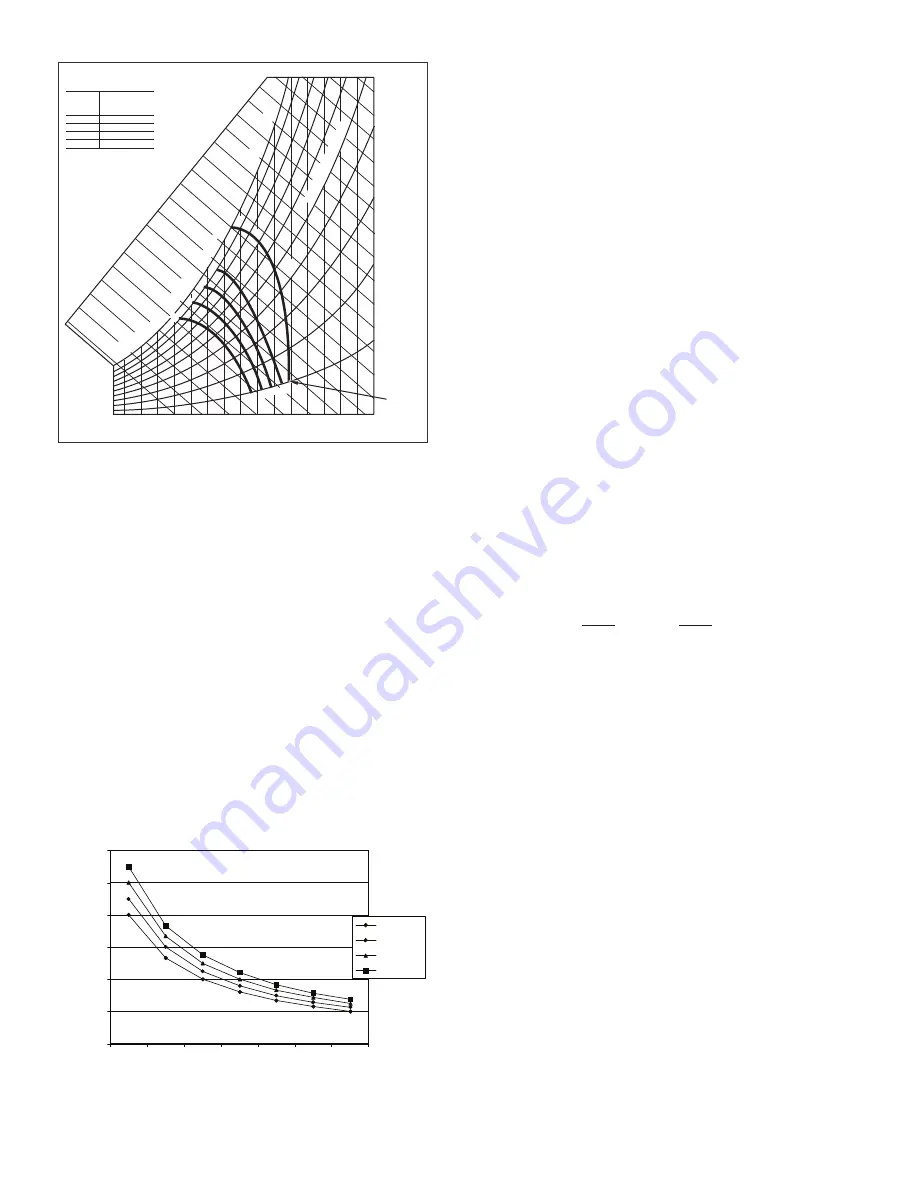
36
Fig. 65 — Enthalpy Changeover Set Points
Indoor Air Quality (IAQ) Sensor Input
The IAQ input can be used for demand controlled ventilation
control based on the level of CO
2
measured in the space or
return air duct.
Mount the accessory IAQ sensor according to manufacturer
specifications. The IAQ sensor should be wired to the AQ and
AQ1 terminals of the controller. Adjust the DCV potentiome-
ters to correspond to the DCV voltage output of the indoor air
quality sensor at the user-determined set point. See Fig. 66.
If a separate field-supplied transformer is used to power the
IAQ sensor, the sensor must not be grounded or the
EconoMi$er
®
IV control board will be damaged.
When using demand controlled ventilation, the minimum damper
position represents the minimum ventilation position for VOC
(volatile organic compounds) ventilation requirements. The maxi-
mum demand ventilation position is used for fully occupied venti-
lation.
When demand controlled ventilation is not being used, the
minimum position potentiometer should be used to set the oc-
cupied ventilation position. The maximum demand ventilation
position should be turned fully clockwise.
Fig. 66 — CO
2
Sensor Maximum Range Settings
Exhaust Set Point Adjustment
The exhaust set point will determine when the exhaust fan runs
based on damper position (if accessory power exhaust is in-
stalled). The set point is modified with the Exhaust Fan set
point (EXH SET) potentiometer. See Fig. 64. The set point rep-
resents the damper position above which the exhaust fans will
be turned on. When there is a call for exhaust, the EconoMi$er
IV controller provides a 45 ± 15 second delay before exhaust
fan activation to allow the dampers to open. This delay allows
the damper to reach the appropriate position to avoid unneces-
sary fan overload.
Minimum Position Control
There is a minimum damper position potentiometer on the
EconoMi$er IV controller. See Fig. 64. The minimum damper
position maintains the minimum airflow into the building
during the occupied period.
When using demand controlled ventilation, the minimum
damper position represents the minimum ventilation position
for Volatile Organic Compound (VOC) ventilation require-
ments. The maximum demand ventilation position is used for
fully occupied ventilation.
When demand controlled ventilation is not being used, the
minimum position potentiometer should be used to set the oc-
cupied ventilation position. The maximum demand ventilation
position should be turned fully clockwise.
Adjust the minimum position potentiometer to allow the mini-
mum amount of outdoor air, as required by local codes, to enter
the building. Make minimum position adjustments with at least
10°F temperature difference between the outdoor and return-
air temperatures.
To determine the minimum position setting, perform the fol-
lowing procedure:
1. Calculate the appropriate mixed air temperature using the
following formula:
T
O
= Outdoor-Air Temperature
OA= Percent of Outdoor Air
T
R
= Return-Air Temperature
RA= Percent of Return Air
T
M
= Mixed-Air Temperature
As an example, if local codes require 10% outdoor air during
occupied conditions, outdoor-air temperature is 60°F, and
return-air temperature is 75°F.
(60 x 0.10) + (75 x 0.90) = 73.5°F
2. Disconnect the supply air sensor from terminals T and T1.
3. Ensure that the factory-installed jumper is in place across
terminals P and P1. If remote damper positioning is being
used, make sure that the terminals are wired according to
Fig. 59 and that the minimum position potentiometer is
turned fully clockwise.
4. Connect 24 vac across terminals TR and TR1.
5. Carefully adjust the minimum position potentiometer until
the measured mixed air temperature matches the calcu-
lated value.
6. Reconnect the supply air sensor to terminals T and T1.
Remote control of the EconoMi$er IV damper is desirable
when requiring additional temporary ventilation. If a field-sup-
plied remote potentiometer (Honeywell P/N: S963B1128) is
wired to the EconoMi$er IV controller, the minimum position
of the damper can be controlled from a remote location.
To control the minimum damper position remotely, remove the
factory-installed jumper on the P and P1 terminals on the
EconoMi$er IV controller. Wire the field-supplied potentiometer
CONTROL
CURVE
A
B
C
D
CONTROL POINT
APPROX.
deg. F (deg. C)
AT 50
%
RH
73 (23)
70 (21)
67 (19)
63 (17)
12
14
16
1
8
20
2
2
2
4
2
6
28
30
32
3
4
3
6
38
40
42
4
4
46
9
0
1
0
0
80
7
0
60
50
40
30
20
10
E
NTHALPY
BTU PER
POUN
D DRY
AI
R
85
(29)
90
(32)
95
(35)
100
(38)
105
(41)
110
(43)
3
5
(2)
35
(2)
40
(4)
40
(4)
105
(41)
110
(43)
45
(7)
45
(7)
50
(10)
50
(10)
55
(13)
55
(13)
60
(16)
60
(16)
65
(18)
65
(18)
70
(21)
70
(21)
75
(24)
75
(24)
80
(27)
80
(27)
85
(29)
90
(32)
95
(35)
100
(38)
A
A
B
B
C
C
D
D
RELA
TI
VE HUMI
DI
TY (
%
)
HIGH LIMIT
CURVE
APPROXIMATE DRY BULB TEMPERATURE--degree
s
F (degree
s
C)
0
1000
2000
3
000
4000
5000
6000
2
3
4
5
6
7
8
RANGE
C
ONFIGURA
TION
(ppm)
DAMPER VOLTAGE FOR MAX VENTILATION RATE
CO
S
EN
S
OR MAX RANGE
S
ETTING
2
8
00 ppm
900 ppm
1000 ppm
1100 ppm
(T
O
OA
) + (T
R
x
RA
) = T
M
100
100
x
Summary of Contents for 50FC A04 Series
Page 96: ...96 APPENDIX D WIRING DIAGRAMS Fig J 50FC 04 06 208 230 1 60 Unit with RTU Open Controller...
Page 97: ...97 APPENDIX D WIRING DIAGRAMS Fig K 50FC 04 06 208 230 3 60 Unit with RTU Open Controller...
Page 98: ...98 APPENDIX D WIRING DIAGRAMS Fig L 50FC 04 06 460 575 3 60 Unit with RTU Open Controller...
Page 99: ...99 APPENDIX D WIRING DIAGRAMS Fig M 50FC 07 208 230 Unit with RTU Open Controller...
Page 100: ...100 APPENDIX D WIRING DIAGRAMS Fig N 50FC 07 460 575 Unit with RTU Open Controller...
Page 101: ...101 APPENDIX D WIRING DIAGRAMS Fig O 50FC 04 06 Power Wiring Diagram 208 230 1 60...
Page 102: ...102 APPENDIX D WIRING DIAGRAMS Fig P 50FC 04 07 Power Wiring Diagram 208 230 3 60...
Page 103: ...103 APPENDIX D WIRING DIAGRAMS Fig Q 50FC 04 07 Power Wiring Diagram 460 575 3 60...
Page 104: ...104 APPENDIX D WIRING DIAGRAMS Fig R 50FC 04 06 SystemVu Control Wiring Diagram All Voltages...
Page 105: ...105 APPENDIX D WIRING DIAGRAMS Fig S 50FC 07 SystemVu Control Wiring Diagram All Voltages...
Page 106: ...106 APPENDIX D WIRING DIAGRAMS Fig T 50FC 04 06 SystemVu Power Wiring Diagram 208 230 1 60...
Page 107: ...107 APPENDIX D WIRING DIAGRAMS Fig U 50FC 04 07 SystemVu Power Wiring Diagram 208 230 3 60...
Page 108: ...108 APPENDIX D WIRING DIAGRAMS Fig V 50FC 04 07 SystemVu Power Wiring Diagram 460 575 3 60...