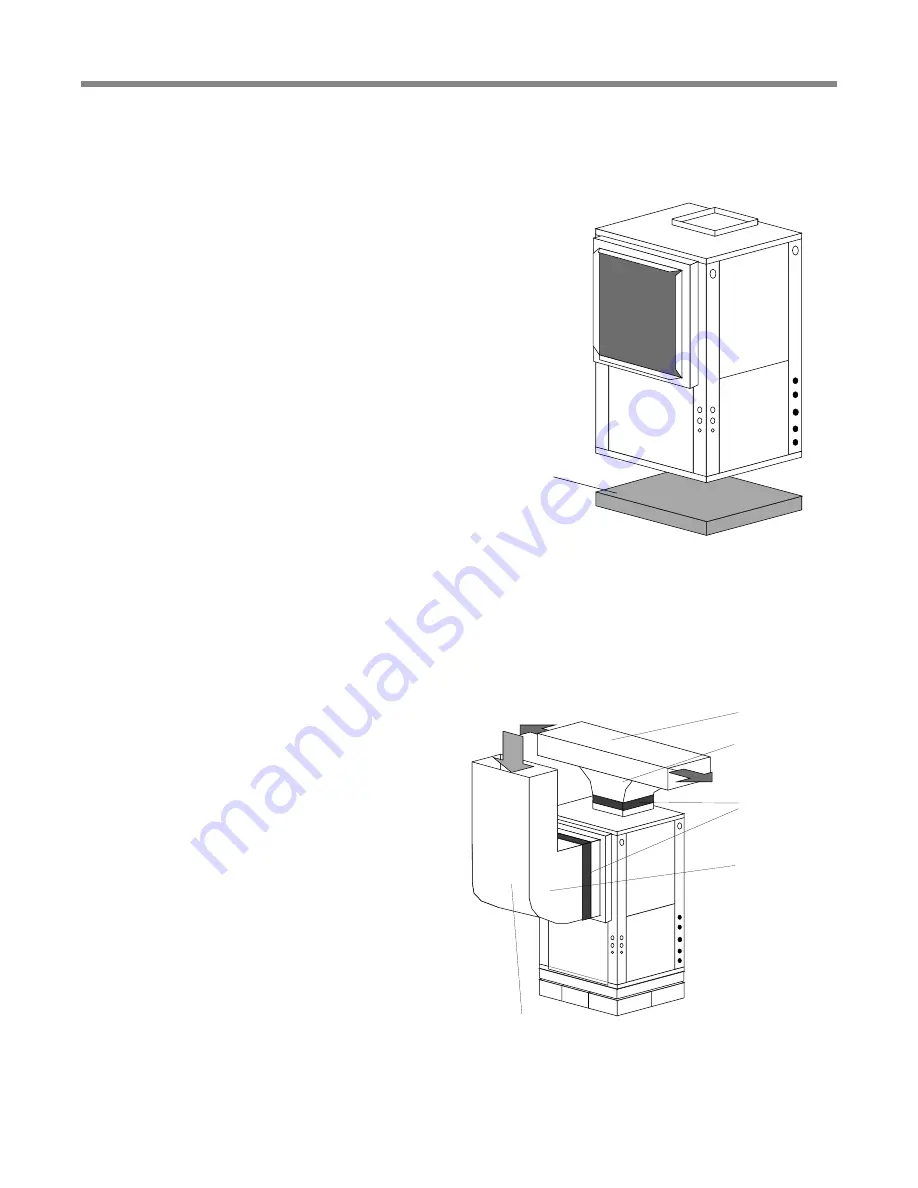
9
R e s i d e n t i a l P a c k a g e d U n i t s - 6 0 H z P u r o n
®
R e v. : 4 J a n . , 2 0 1 2
Vertical Installation
Flexible canvas duct
connector to reduce
noise and vibration
Use turning vanes in
supply transition
Internally insulate supply
duct for first 1.2 m each way
to reduce noise
Internally insulate return
transition duct to reduce
noise
Rounded return
transition
Rev.: 6/2/09S
Figure 7: Vertical Unit Mounting
Figure 8: Typical Vertical Unit Installation Using Ducted
Return Air
$LU3DGRUH[WUXGHG
SRO\VW\UHQHLQVXODWLRQERDUG
Vertical Unit Location
Units are not designed for outdoor installation. Locate
the unit in an INDOOR area that allows enough space for
service personnel to perform typical maintenance or repairs
without removing unit from the mechanical room/closet.
Vertical units are typically installed in a mechanical room
or closet. Never install units in areas subject to freezing or
where humidity levels could cause cabinet condensation
(such as unconditioned spaces subject to 100% outside air).
Consideration should be given to access for easy removal of
the fi lter and access panels. Provide suffi cient room to make
water, electrical, and duct connection(s).
If the unit is located in a confi ned space, such as a closet,
provisions must be made for return air to freely enter the
space by means of a louvered door, etc. Any access panel
screws that would be diffi cult to remove after the unit is
installed should be removed prior to setting the unit. Refer to
Figures 7 and 8 for typical installation illustrations. Refer to
unit specifi cations catalog for dimensional data.
1. Install the unit on a piece of rubber, neoprene or other
mounting pad material for sound isolation. The pad
should be at least 3/8” [10mm] to 1/2” [13mm] in
thickness. Extend the pad beyond all four edges of the
unit.
2. Provide adequate clearance for fi lter replacement
and drain pan cleaning. Do not block fi lter access
with piping, conduit or other materials. Refer to unit
specifi cations for dimensional data.
3. Provide access for fan and fan motor maintenance and
for servicing the compressor and coils without removing
the unit.
4. Provide an unobstructed path to the unit within the
closet or mechanical room. Space should be suffi cient to
allow removal of the unit, if necessary.
5. Provide access to water valves and fi ttings and
screwdriver access to the unit side panels, discharge
collar and all electrical connections.
Downfl ow units may be installed directly on the fl oor. The
optional internal electric heat is rated for zero clearance to
combustible materials.
The installation of water source heat pump units and all
associated components, parts and accessories which make
up the installation shall be in accordance with the regulations
of ALL authorities having jurisdiction and MUST conform to
all applicable codes. It is the responsibility of the installing
contractor to determine and comply with ALL applicable
codes and regulations.