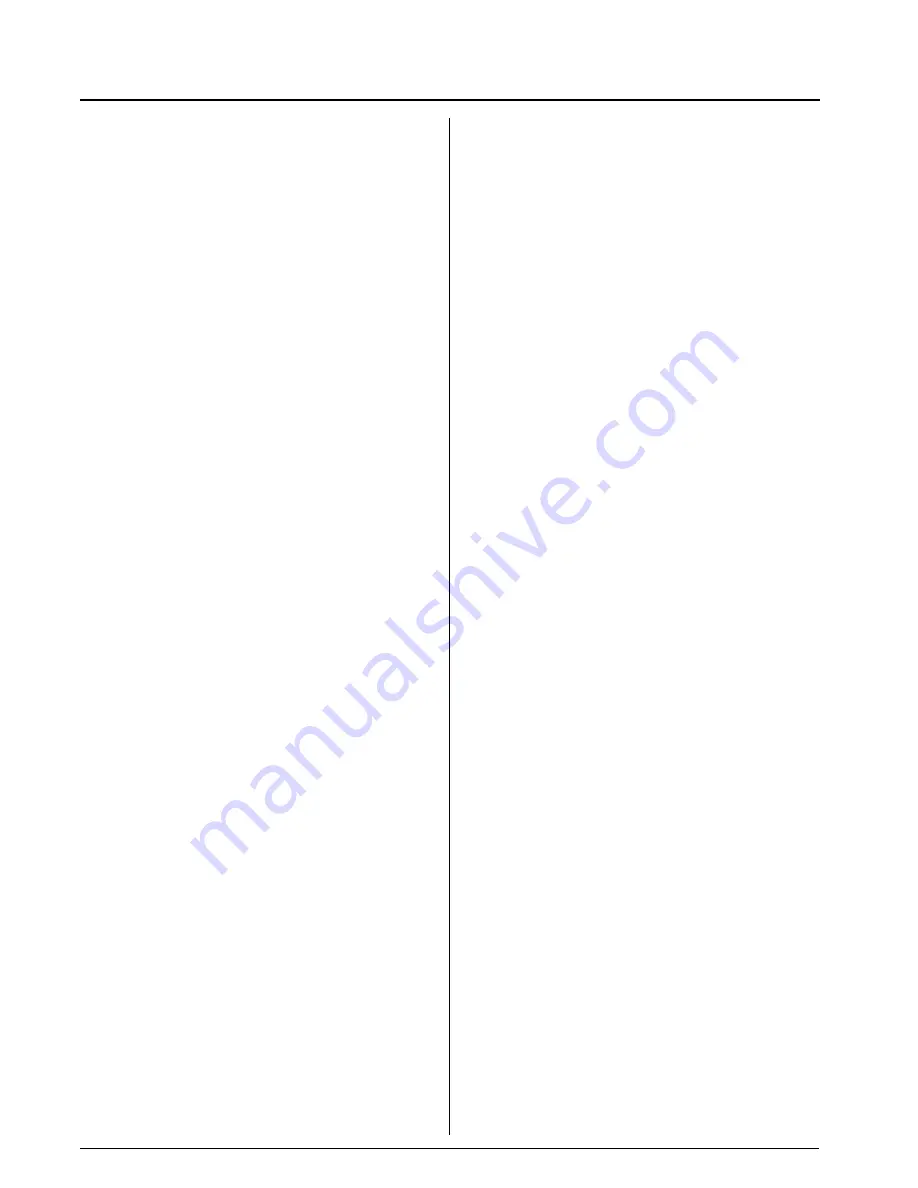
42 GW
GB - 4
General Information
Unit installation
Read this instruction manual thoroughly before starting
installation.
• This unit complies with the low-voltage (EEC/73/23) and
electromagnetic compatibility (EEC/ 89/336) directives.
• The installation should be carried out by a qualified installer.
• Follow all current national safety code requirements.
In particular ensure that a properly sized and connected ground
wire is in place.
• Check that the voltage and frequency of the mains power supply
are as required for the unit to be installed; the available power
source must be adeguate to operate all other appliances
connected to the same line.
Also ensure that national safety code requirements have been
followed for the main supply circuit.
• Where necessary, use field-supplied 25 mm I.D. PVC pipe of
appropriate length and with the correct thermal insulation for the
condensate drain extension.
• After installation thoroughly test system operation and explain all
system functions to the owner.
• Use this unit only for factory approved applications: the unit
cannot be used in laundry or steam pressing premises.
WARNING:
Disconnect the mains power supply switch before servicing
the system or handling any internal parts of the unit.
• The manufacturer declines any liability for damage resulting
from modifications or errors in the electrical or water
connections.
Failure to observe the installation instructions, or use of the
unit under conditions other than those indicated in Table
"Operating limits" of the unit installation manual, will
immediately invalidate the unit warranty.
• Failure to observe electric safety codes may cause a fire hazard in
the event of short circuits.
• Inspect equipment for damage during transport. In case of
damage file an immediate claim with the shipping company.
Do not install or use damaged units.
• In case of malfunction turn the unit off, disconnect the mains
power supply and contact a qualified service engineer.
• Maintenance must only be carried out by qualified personnel.
• All of the manufacturing and packaging materials used for
this appliance are biodegradable and recyclable.
• Dispose of the packaging material in accordance with local
requiremements.
Choosing the installation site
Positions to avoid:
• Exposure to direct sunlight.
• Areas close to heat sources.
• On damp walls or in positions that may be exposed to water
hazard.
• Where curtains or furniture may obstruct free air circulation.
Recommendations:
• Choose an area free from obstructions which may cause uneven
air distribution and/or return.
• Consider using an area where installation is easy.
• Choose a position that allows for the clearances required.
• Look for a position in the room which ensures the best possible air
distribution.
• Install unit in a position where condensate can easily be piped to an
appropriate drain.