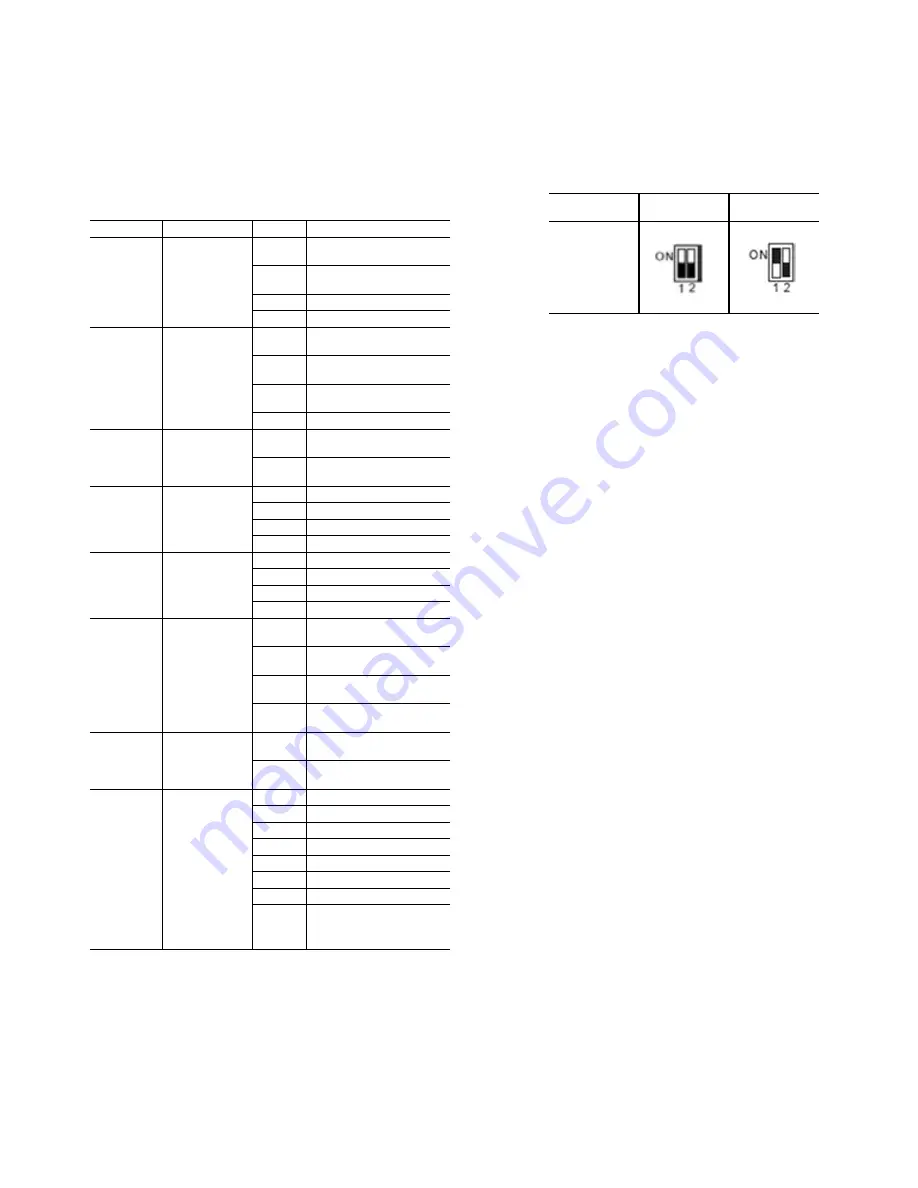
25
Advanced Settings
• Hold the “MENU (SW4)” button down for five seconds
to enter the menu.
• Press “UP(SW5) / DOWN(SW6)” button to select and
set the item. When the number is chosen, the number will
flash. Then press “OK(SW3)” to confirm and set the next
number. Use Table 19 below as reference.
• Hold “OK(SW3)” again to exit the main menu.
Table 19 — List of Menu Functions
Snow-Blowing Function
1.
Press SW5 button on spot check box of the header
outdoor unit to enter the snow-blowing function. It will
display “Sn0” for 15 seconds.
2.
Press SW5 button again to exit the snow-blowing
function. It will display “Sn1” for 15 seconds.
The snow-blowing modes can be selected through S11 dip
switch on spot check box as shown in Fig. 42..
Fig. 42 —S11 - Snow-Blowing Modes
If the unit receives a startup signal, it will exit the snow-
blowing function.
Pre-Start Check
• Check that the refrigerant pipe line and communication
wire with indoor and outdoor unit have been connected
to the same refrigeration system.
• Outdoor units require either 208/230-3-60 or 460-3-60
power. Verify that the power and phase requirements are
correct and all three legs are present.
• Check that power source’s voltage is within 10% of the
rated voltage.
• Check and confirm that the power and control wire are
correctly connected.
• Check that the wired controllers are properly connected.
• Before powering on, confirm there is no short circuit for
each line.
• Check that all units have passed a nitrogen pressure test
for 24 hours.
• Provide the customer accurate “as-built” drawings and
documents, including actual piping lengths and
locations, unit addresses, settings, etc.
• Ensure additional refrigerant charge calculations are
correct, and that the system is charged accordingly.
• Energize outdoor units for at least 24 hours before
startup to ensure proper oil temperature.
• Ensure all refrigerant valves on outdoor units are fully
open. Ensure oil balancing valves are open for 2 and 3-
module systems. If these valves are not fully open,
equipment damage may occur.
SYMBOL
FUNCTION
ITEM
DESCRIPTION
_n1_
Special
function for
debugging
_n12
Forced cooling (62.6
F
of IDU)
_n13
Forced heating (86
F of
IDU)
_n14
Cooling test
_n15
Heating Test
_n2_
Refrigerant
recycle
function
_n21
Refrigerant recycled to
outdoor units
_n22
Refrigerant recycled to
indoor units
_n23
Refrigerant recycled to
piping
_n26
Maintenance operation
_n3_
Malfunction
query
_n31
Historical malfunction
query
_n32
Clear the historical mal-
function
_n4_
Night time
setting
_n41
6/10H (default)
_n42
6/12H
_n43
8/10H
_n44
8/12H
_n5_
Silent mode
setting
_n51
Night silent mode
_n52
Silent mode
_n53
Super silent mode
_n54
Silent mode off (default)
_n8_
Static pressure
mode setting
_n81
Standard static pressure
mode (default)
_n82
Low static pressure
mode (reserved)
_n83
Medium static pressure
mode (reserved)
_n84
High static pressure
mode (reserved)
_nb_
Temperature
unit setting
_nb1
Temperature unit
(Celsius)
_nb2
Temperature unit
(Fahrenheit)
_nC_
T4 sensor
(outdoor
temperature)
threshold to
enable
Auxiliary Heat.
Aux heat will
enable when
outdoor
temperature
falls 1.8 F
below this
temperature.
_nC1
Auxiliary heat disabled
_nC2
5
°
F
_nC3
15
°
F
_nC4
25
°
F
_nC5
35
°
F
_nC6
45
°
F
_nC7
55
°
F
_nC8
65
°
F
Mode
Heavy Snow
Mode
Light Snow
Mode
S11