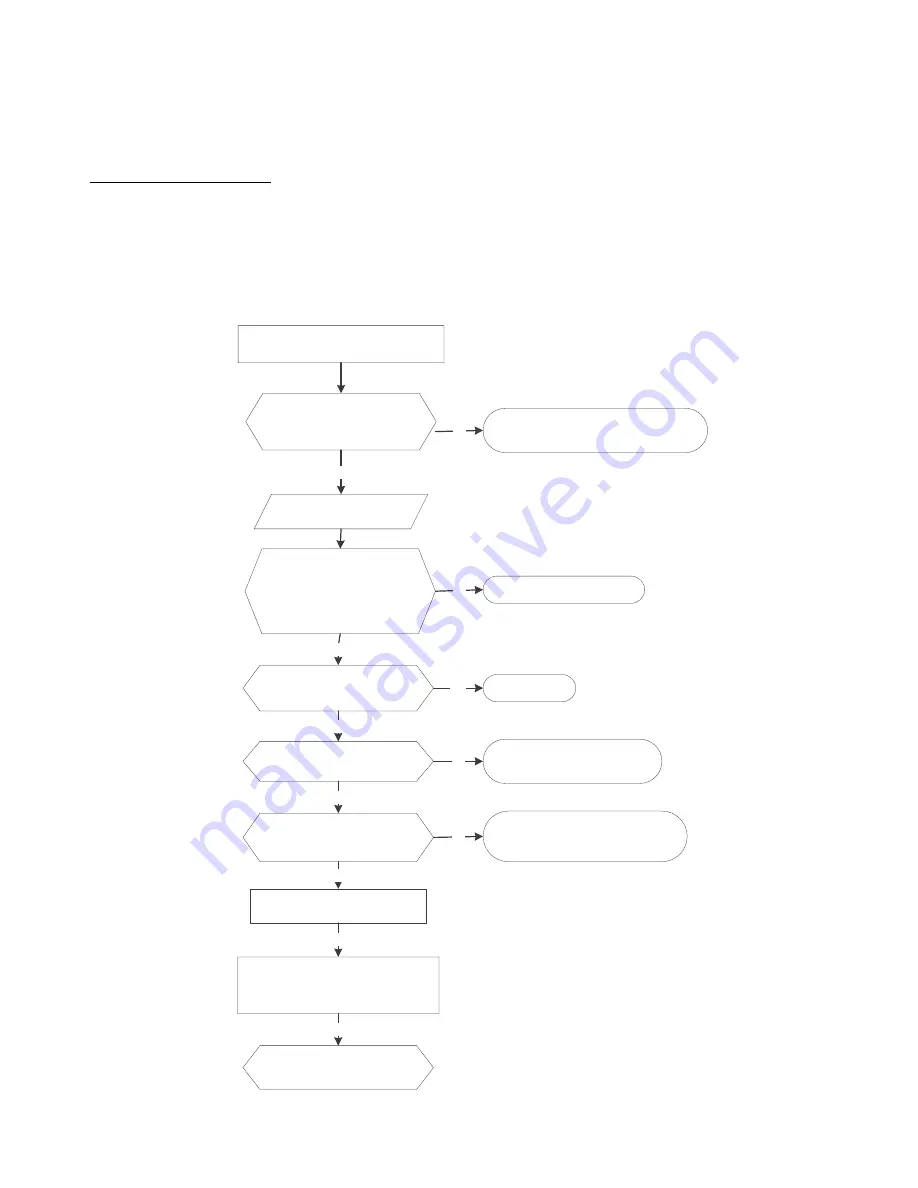
SG-38MARB-01 Specifications subject to change without notice.
53
DIAGNOSIS AND SOLUTION (CONT)
Low Pressure Protection (PC03)
Description:
The outdoor pressure switch shuts the unit down because the low pressure is lower than 0.13 MPa and the LED displays the failure
code.
Recommended parts to repair:
• Connection wires
• Outdoor PCB
• Low pressure protector
• Refrigerant
Troubleshooting
Yes
Yes
No
No
No
Yes
No
No
Yes
Yes
No
No
Low pressure protection
Are the low pressure protector
and the main control
board wired properly?
Reconnect the low pressure protector and
the main control board.
Is the low pressure
protector broken?
Method: Disconnect the plug.
Measure the low pressure protector
resistance. If the protector is normal,
the value is 0.
Does the problem still exist?
Replace the low pressure protector.
Is the outdoor ambient temperature
too low?
Stop the unit.
Is the valve core of the high
pressure valve fully opened?
Is the indoor fan running properly
in the cooling mode?
Replace the outdoor main board.
Does a problem still exist?
When the refrigerant level is not
sufficient, does the system function
properly after more refrigerant is added?
Check whether the refrigerant
system is functioning properly.
Open the valve core of the
high pressure valve.
Refer to the “Fan Speed is operating
outside of Normal Range” malfunction.